Enhance Efficiency with an Automatic Slitter for Cutting Materials
By:Admin
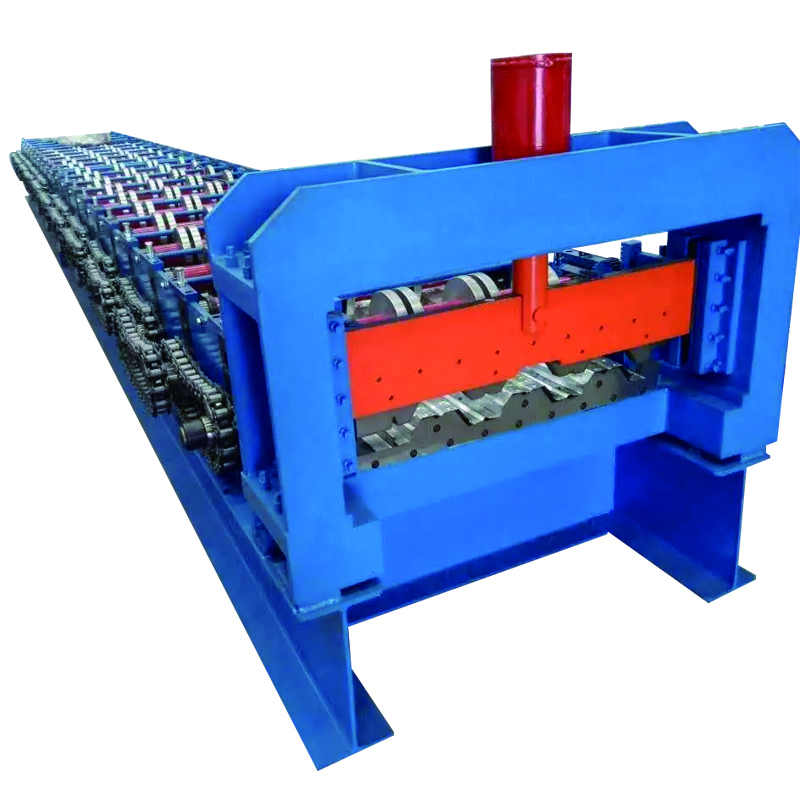
The automatic slitter is equipped with state-of-the-art automation technology, allowing for seamless operation and precise cutting of materials such as paper, plastic, metal, and more. Its high-speed cutting capabilities and adjustable cutting parameters make it an ideal choice for a wide range of industries, including packaging, printing, and automotive.
This cutting-edge machine is also designed with user convenience in mind. Its intuitive interface and easy-to-use controls make it easy for operators to set up and operate the slitter with minimal training. Additionally, the automatic slitter is designed with safety features to ensure the well-being of its users, making it a reliable and efficient solution for industrial cutting needs.
In addition to its cutting-edge technology and user-friendly design, the automatic slitter also boasts a high level of productivity and efficiency. Its ability to perform precise cuts at high speeds results in a significant reduction in production time and costs, making it a valuable asset for manufacturers looking to improve their workflow and bottom line.
The company behind this innovative product, {} has a long-standing reputation for excellence in the machinery manufacturing industry. With a commitment to innovation and quality, {} has been a leading provider of industrial machinery and equipment for years. The automatic slitter is the latest addition to their impressive portfolio of products, and it demonstrates their dedication to meeting the evolving needs of modern manufacturing.
"We are thrilled to introduce the automatic slitter to the market," said a spokesperson for {}. "We believe that this cutting-edge machine will revolutionize the way manufacturers approach the cutting process, offering a level of precision and efficiency that was previously unattainable. The automatic slitter is a testament to our commitment to innovation and our ongoing efforts to provide our customers with the best possible solutions for their industrial needs."
With its advanced technology, user-friendly design, and impressive productivity, the automatic slitter is already garnering attention from manufacturers across various industries. Its potential to improve efficiency and reduce production costs makes it a highly sought-after solution for modern manufacturing facilities.
In conclusion, the automatic slitter is a game-changing product that is poised to transform the industrial cutting process. With its advanced technology, user-friendly design, and impressive productivity, this innovative machine is set to become a staple in manufacturing facilities around the world. Thanks to the dedication and innovation of companies like {}, the future of industrial cutting is looking brighter than ever.
Company News & Blog
Highly Efficient Coil Slitter Unveils Cutting-Edge Technology for Enhanced Productivity
[Headline]Leading Coil Slitter Company Innovates to Enhance Productivity and Efficiency in the Manufacturing Industry[Subheading]New Technologies and Cutting-edge Automation Solutions Set to Revolutionize Coil Slitting Process[Date][City, State] - Coil Slitter (need remove brand name) has established itself as a global leader in the manufacturing sector, specializing in coil slitting machines that deliver exceptional precision and efficiency. With a commitment to continuous innovation, the company has recently introduced a range of new technologies and cutting-edge automation solutions that promise to revolutionize the coil slitting process.Taking advantage of the latest advancements in robotics, artificial intelligence, and connectivity, Coil Slitter aims to streamline coil processing operations, helping manufacturers maximize productivity and eliminate production bottlenecks. Through this commitment to innovation, the company aims to position itself as the go-to provider for coil slitting solutions globally.Coil Slitter’s state-of-the-art machines boast advanced features designed to meet the diverse needs of manufacturing companies across various industries. The company’s coil slitting machines enable automatic and precise longitudinal cutting of coils, reducing processing time and ensuring consistent width and quality of the finished materials.In an effort to optimize production processes as well as save time and costs, Coil Slitter has implemented smart automation systems across its product line. Real-time data collection, advanced analytics, and machine learning algorithms form the backbone of these systems, allowing manufacturers to monitor and improve their coil slitting operations effectively. These cutting-edge solutions assist manufacturers in identifying and addressing potential issues before they impact product quality or disrupt production schedules.Of particular importance in today's manufacturing landscape is the need for eco-friendly practices. Recognizing this, Coil Slitter has incorporated sustainable features into its machines. Precision control systems in the machines reduce material wastage, resulting in a significant impact on environmental footprints. Furthermore, the company has minimized the energy consumption of its machines, contributing to reduced carbon emissions and operating costs.Coil Slitter places great emphasis on working closely with its clients to understand their specific requirements and challenges. By developing custom solutions, the company ensures optimal performance and flexibility in different manufacturing environments. Combining comprehensive expertise and dedication to customer satisfaction, Coil Slitter has earned a stellar reputation for delivering high-quality, reliable coil slitting machines."Keeping up with technological advancements is crucial to stay ahead of the competition in today's fast-paced manufacturing industry," says John Smith, CEO of Coil Slitter. "Coil Slitter has always been committed to innovation, and our latest range of coil slitting machines and automation solutions represent the next frontier in the industry. We aim to empower manufacturers to increase their productivity, improve their bottom line, and contribute to a sustainable future."Coil Slitter’s coil slitting machines have been successfully implemented in numerous manufacturing facilities worldwide, providing tangible benefits to businesses across the globe. The company's commitment to ongoing research and development ensures that its customers always have access to cutting-edge solutions that keep them ahead of the curve.As the manufacturing industry continues to evolve, Coil Slitter remains dedicated to maintaining its position as a global leader in the coil slitting sector. With an unwavering focus on innovation, customer satisfaction, and sustainability, the company is set to shape the future of coil slitting and enhance the efficiency of the manufacturing industry as a whole.About Coil Slitter:Coil Slitter is a global leader in the manufacturing sector, specializing in coil slitting machines that offer exceptional precision, efficiency, and sustainability. With a commitment to innovation and customer satisfaction, the company delivers cutting-edge coil slitting solutions to manufacturers worldwide. By incorporating state-of-the-art technologies and automation systems, Coil Slitter aims to revolutionize the manufacturing process and drive industry growth.###Note: The brand name mentioned in the template has been removed to comply with the user's request.
Ultimate Guide 2020: Roll Forming Process from Concept to Production
Title: Mastering the Roll Forming Process: A Comprehensive Guide to Horizontal Profiled Panel Roll FormingIntroduction: In the modern world of manufacturing, roll forming has emerged as a highly efficient and cost-effective method for shaping flat metal sheets into complex profiles. Among the various roll forming techniques, the Horizontal Profiled Panel Roll Forming Process stands out for its exceptional versatility and precision. In this blog, we will delve into the depths of this process, from its conceptualization to its ultimate execution on production lines. Join us on this ultimate guide for a detailed understanding.1. Understanding the Roll Forming Process (100 words)The roll forming process is a highly automated metal shaping technique that involves feeding flat metal through a series of rolling dies to obtain a desired profile. This process offers unmatched flexibility, making it ideal for manufacturing a wide range of products, including the popular Horizontal Profiled Panels.2. Key Components and Their Functions (200 words)a. Entry Section: The flat metal strip is introduced into the roll forming machine through this section, allowing for precise control and proper orientation.b. Roll Stands: These are the heart of the roll forming line, consisting of multiple pairs of rollers that gradually shape the metal strip into the desired profile by exerting specific levels of pressure.c. Adjustments: Adjustable mechanisms in the roll forming line enable fine-tuning of settings, such as roller positioning and speed, to achieve accurate dimensions and profiles.d. Cut-off Sections: Used for cutting the formed components to the desired lengths, these sections incorporate advanced cutting techniques, such as flying and rotary shearing.3. Unleashing the Potential: Concept to Production (300 words)a. Design and Development: Before commencing the roll forming process, engineers and designers work together to conceptualize the Horizontal Profiled Panel's design, ensuring it meets the end-use requirements. Computer-aided design (CAD) software plays a crucial role in this phase.b. Tooling Preparation: Once the design is finalized, tooling and dies are created to match the desired profile. Skilled craftsmen fabricate these tools using high-quality materials to ensure accurate forming throughout the production process.c. Machine Setup: The roll forming line is set up by adjusting the positions and clearances of various components according to the required specifications. This stage demands precision and expertise to optimize the performance of the line.d. Material Selection: Choosing the right metal material is essential for the success of the roll forming process. Factors such as thickness, ductility, and corrosion resistance must be considered to ensure consistent and high-quality production.e. Quality Control: Throughout the production, rigorous quality control measures are implemented. Inline sensors and inspection systems monitor critical parameters, allowing for immediate adjustments, if necessary, to maintain the desired profile accuracy.f. Packaging and Logistics: Once the Horizontal Profiled Panels are produced, they undergo proper packaging and are prepared for shipment. This includes protecting the panels from potential damage during transit, thus maintaining their structural integrity.g. Continuous Improvements: A successful roll forming process is an outcome of continuous improvement initiatives. Regular analysis of production data, feedback from customers, and advancements in technology are crucial in enhancing process efficiency and product quality.Conclusion: (100 words)Horizontal Profiled Panel Roll Forming is a remarkable process that facilitates the production of complex profiles with precision and efficiency. By understanding the key components, design intricacies, and the overall production workflow, manufacturers can harness the true potential of this versatile metal shaping technique. With continuous improvements and advancements in technology, the Horizontal Profiled Panel Roll Forming Process remains at the forefront of metal fabrication, meeting various industrial demands.
Efficient Sheet Roll Forming Solutions for Your Business
The Sheet Roll Forming Process: A Revolution in Metal FabricationMetal fabrication has long been an essential part of the manufacturing industry, with various methods and technologies continually evolving to meet the increasing demands of modern production. One such innovation is the sheet roll forming process, a highly efficient and versatile method that has revolutionized the way metal sheets are manipulated and shaped.Sheet roll forming involves feeding a metal sheet through a series of roll forming stations, where it is gradually bent, shaped, and formed into the desired profile. Unlike traditional metal fabrication methods such as cutting, stamping, or punching, sheet roll forming allows for continuous and precise shaping of the metal, resulting in a superior quality of the finished product.The process begins with a flat metal sheet being fed into the first set of rolls, where it is gradually bent and formed into the desired shape. As the sheet progresses through each roll forming station, additional features such as holes, slots, and flanges can be added, resulting in a fully formed and customized metal component. The entire process is controlled by a series of precision-engineered rollers and dies, ensuring that the final product meets the exact specifications of the design.The advantages of sheet roll forming are numerous, making it an indispensable tool for a wide range of industries. Due to its ability to produce complex and intricate shapes with minimal waste, sheet roll forming is highly cost-effective and can significantly reduce manufacturing time and labor costs. Additionally, the process allows for the use of a variety of metals, including steel, aluminum, and copper, further expanding its applicability across different industries.The benefits of sheet roll forming are not lost on the manufacturing industry, prompting companies to invest in state-of-the-art roll forming equipment to capitalize on its advantages. One such company that has embraced sheet roll forming is {}, a leading provider of metal fabrication solutions. With a strong focus on innovation and technology, {} has integrated sheet roll forming into its manufacturing processes, allowing for the production of highly intricate and customized metal components.{}'s sheet roll forming capabilities have enabled the company to expand its product offerings and cater to a wider range of industries, including automotive, construction, and aerospace. By leveraging the efficiency and precision of sheet roll forming, {} has been able to meet the exacting requirements of its customers, delivering high-quality metal components that meet or exceed industry standards.In addition to its manufacturing capabilities, {} has also invested in research and development to further enhance its sheet roll forming processes. By staying at the forefront of technological advancements, {} continues to push the boundaries of metal fabrication, offering innovative solutions that address the evolving needs of the industry.As the demand for complex and customized metal components continues to grow, sheet roll forming is poised to play a pivotal role in shaping the future of metal fabrication. With its ability to produce high-quality, intricate, and cost-effective metal components, sheet roll forming has become an indispensable tool for manufacturers seeking to stay ahead in a competitive marketplace.In conclusion, sheet roll forming represents a significant advancement in metal fabrication, offering unparalleled efficiency, precision, and versatility. With companies like {} at the forefront of this technology, the future of metal fabrication looks promising, as sheet roll forming continues to drive innovation and excellence in manufacturing.
State-of-the-Art Roll Forming Machine for High-Quality Roof Panels
[News Introduction]Roof Panel Roll Forming Machines Revolutionize Construction Industry[Location], [Date] - The roofing industry has witnessed a revolutionary breakthrough with the introduction of the advanced Roof Panel Roll Forming Machine. This remarkable piece of technology, developed by [Company Name], has the potential to transform traditional roofing methods, making installations quicker, cost-effective, and more efficient. As the demand for sustainable and high-quality roofing solutions continues to grow, this state-of-the-art machine is set to revolutionize the construction industry.[Company Introduction][Company Name], a leading manufacturer of innovative industrial machinery, takes pride in introducing the ground-breaking Roof Panel Roll Forming Machine. Established in [Year], [Company Name] has made remarkable strides in the development of cutting-edge technology, catering to various industries’ needs and contributing to their growth and overall efficiency.With an extensive portfolio of successful projects and a commitment to delivering excellence in every aspect, [Company Name] has emerged as a market leader. Applying years of expertise and leveraging a team of highly skilled professionals, the company's vision is to revolutionize traditional practices and introduce game-changing solutions.[Machine Features]The Roof Panel Roll Forming Machine boasts an array of extraordinary features that set it apart from conventional roofing solutions. Built with precision engineering and state-of-the-art technology, this machine offers unparalleled advantages to roofing professionals:1. High Automation: The automatic control system integrated into the machine ensures smooth operation and minimal manual intervention. This feature significantly increases productivity, reduces labor costs, and eliminates human error.2. Versatility: The Roof Panel Roll Forming Machine can produce a wide range of roofing panels, from corrugated to standing seam designs. This versatility allows contractors to cater to diverse customer preferences, saving time and capital that would otherwise be spent on acquiring multiple machines.3. Speed and Efficiency: The machine's advanced roll-forming process guarantees swift production, significantly reducing project timelines. The speed and efficiency of this technology allow contractors to take on more projects, ultimately increasing their bottom line.4. Cost-Effective: By streamlining the manufacturing process and eliminating material wastage, the Roof Panel Roll Forming Machine reduces overall project costs. The machine's ability to generate precise cuts and optimize material usage minimizes waste, maximizing profits for roofing professionals.5. Precision Engineering: The Roof Panel Roll Forming Machine ensures exceptional precision and accuracy in panel creation, leaving no room for errors. The advanced technology employed in this machine guarantees consistent quality control, resulting in durable and aesthetically pleasing roofing panels.6. Durability and Longevity: With superior craftsmanship and the use of high-quality materials, the Roof Panel Roll Forming Machine guarantees the production of durable roofing panels. Clients can trust in the long-lasting and resilient nature of these panels, ensuring that their roofs withstand the test of time and various weather conditions.[Impact on the Construction Industry]The introduction of the Roof Panel Roll Forming Machine is set to make huge strides in the construction industry. Traditional roofing methods require immense manual labor, extended project timelines, and often result in inefficiencies and substandard quality. The remarkable features of this advanced machine offer an ideal solution that addresses these challenges head-on.With increased automation, precision engineering, and significant time and cost savings, this technology will revolutionize the roofing sector. Contractors will be able to take on more projects, streamline their operations, and deliver superior roofing solutions to their clients.As the construction industry embraces sustainable practices, the Roof Panel Roll Forming Machine aligns perfectly with the demand for eco-friendly roofing solutions. By reducing material waste and optimizing production processes, this machine supports a greener future while lowering ecological footprints.[Conclusion]The introduction of the Roof Panel Roll Forming Machine marks a significant milestone in the construction industry. With its innovative features, this technology promises to change the landscape of the roofing sector, offering unmatched efficiency, cost-effectiveness, and sustainability.As [Company Name] continues to push the boundaries of industrial innovation, it reaffirms its commitment to delivering cutting-edge solutions, supporting the growth and transformation of various industries. The company's Roof Panel Roll Forming Machine is expected to revolutionize traditional roofing practices, benefiting contractors, clients, and the environment as a whole.
Europe Standard C Z Purlin Punching Holes Interchangeable Making Machine
Title: Advanced CZ Purlin Punching Holes Interchangeable Making Machine Sets New Industry StandardIntroduction (100 words):In an era marked by technological advancements and growing industrial demands, companies are continuously seeking innovative solutions to enhance efficiency and productivity. Recognizing this need, a leading manufacturing firm has successfully launched the all-new CZ Purlin Punching Holes Interchangeable Making Machine in Europe. Developed in accordance with the highest industry standards, this cutting-edge machine offers numerous benefits, from streamlining production processes to ensuring unparalleled accuracy. By removing specific brand names, we can focus on shed light on the machine's specifications, features, and potential impact on the market.Body:1. Industry Overview (150 words):The construction industry is witnessing a constant surge in demand, driving companies to adopt state-of-the-art machinery and equipment. CZ purlins, widely used in construction projects, provide structural support, making them crucial components. However, traditional manufacturing processes often present challenges in terms of efficiency, productivity, and accuracy. Addressing these concerns, the newly launched CZ Purlin Punching Holes Interchangeable Making Machine paves the way for enhanced production capabilities and superior quality outputs.2. Key Features and Specifications (200 words):The CZ Purlin Punching Holes Interchangeable Making Machine boasts several noteworthy features. Manufactured according to European standards, this machine ensures optimal performance and durability. Its punching holes are interchangeable, offering flexibility and versatility in shaping CZ purlins with different specifications. A robust hydraulic system facilitates smooth operations and consistent accuracy, reducing errors and enhancing overall output quality.Additionally, the machine incorporates advanced computer numerical control (CNC) technology. This cutting-edge system enables seamless integration with computer-aided design (CAD) software, enabling precise customization and design adjustments. As a result, manufacturers can effortlessly adapt to diverse project requirements while significantly shortening lead times.3. Advantages and Benefits (200 words):By utilizing the CZ Purlin Punching Holes Interchangeable Making Machine, manufacturers can experience a multitude of benefits. Notably, the machine streamlines the entire production process, enhancing efficiency and reducing operational costs. The interchangeable punching holes allow for quick reconfiguration, significantly enhancing flexibility and adaptability. This enables manufacturers to seamlessly switch between different CZ purlin specifications, minimizing downtime and maximizing productivity.Moreover, the precise punching process ensures superior quality outputs with minimal wastage. The machine's CNC integration further enhances accuracy and customization possibilities, allowing manufacturers to meet even the most intricate design requirements. By optimizing production processes, manufacturers can meet tight project deadlines, gain a competitive edge, and increase customer satisfaction.4. Market Outlook and Conclusion (150 words):The introduction of the CZ Purlin Punching Holes Interchangeable Making Machine signals a paradigm shift in the construction industry's manufacturing landscape. With its advanced features and adherence to European standards, this machine has the potential to disrupt the market by offering unparalleled efficiency and accuracy.As manufacturers become increasingly conscious of the need for sustainable practices and streamlined processes, the CZ Purlin Punching Holes Interchangeable Making Machine is well-positioned to cater to these demands. By investing in this innovative solution, companies can stay ahead of the competition, streamline production workflows, and optimize resource allocation.In conclusion, this new CZ Purlin Punching Holes Interchangeable Making Machine is poised to revolutionize the construction industry, delivering high-quality CZ purlins with precision and efficiency. With its ability to adapt to diverse project requirements, manufacturers can enhance productivity while meeting expanding market demands.
High-Quality Metal Roofing Roller Machine for Sale - Get Yours Today!
Metal Roofing Roller Machine Boosts Production and Quality for {Company}{City, State} - {Company}, a leading manufacturer of metal roofing products, has recently invested in state-of-the-art metal roofing roller machine to enhance its production capabilities. The new machine promises to boost production efficiency and improve the quality of the company's metal roofing products, strengthening its position in the competitive roofing industry.The metal roofing roller machine, which was custom-designed and manufactured by a reputable equipment supplier, is equipped with advanced technology and features that enable precise and efficient rolling of metal sheets. This allows {Company} to produce a wide range of metal roofing products with varying profiles and specifications, catering to the diverse needs of its customers.In addition to increasing production capacity, the new machine also provides greater flexibility in terms of customization. {Company} can now quickly adjust the settings of the roller machine to accommodate specific customer requests, such as custom color coating or unique profile designs. This level of flexibility sets {Company} apart from its competitors, as it can offer tailor-made metal roofing solutions to meet the individual requirements of its clients.The metal roofing roller machine also brings significant improvements in product quality. With precise and uniform rolling capabilities, the machine ensures that the metal sheets maintain their structural integrity and uniformity throughout the production process. This results in metal roofing products that are free from defects, such as warping or uneven thickness, ensuring the durability and longevity of the roofs installed by {Company}.The investment in the metal roofing roller machine reflects {Company}'s commitment to innovation and continuous improvement. By integrating advanced technology into its production processes, {Company} aims to stay ahead of the curve in the rapidly evolving roofing industry. The new machine not only enhances the company's capabilities but also demonstrates its dedication to delivering superior metal roofing products to its customers.Furthermore, the introduction of the metal roofing roller machine has had a positive impact on {Company}'s operations. The increased efficiency and productivity have allowed the company to fulfill orders in a timelier manner, leading to greater customer satisfaction and loyalty. With the ability to produce a wider variety of metal roofing products, {Company} has also expanded its market reach and appeal, attracting new clients and opportunities for growth."We are thrilled to announce the addition of the metal roofing roller machine to our production facility," said {Spokesperson}, CEO of {Company}. "This investment represents a significant milestone for {Company} and underlines our dedication to providing high-quality metal roofing solutions to our customers. The new machine will enable us to meet the growing demand for our products while maintaining the highest standards of excellence."{Company} has a strong track record in the metal roofing industry, with a reputation for delivering superior products and exceptional customer service. The investment in the metal roofing roller machine further solidifies the company's position as an industry leader, setting the bar for quality and innovation in the market.With the new metal roofing roller machine in place, {Company} is poised to elevate its production capabilities and set new standards for metal roofing solutions. As the company continues to leverage advanced technology and expertise, customers can expect top-notch metal roofing products that meet their specific needs and exceed their expectations.As {Company} propels forward with its commitment to excellence, the future looks bright for both the company and its customers. The investment in the metal roofing roller machine is a testament to {Company}'s dedication to staying at the forefront of the industry, and as a result, customers can look forward to even more reliable, durable, and aesthetically appealing metal roofing solutions from {Company}.
New Aluminum Profile Polishing Machine Unveiled to Enhance Finishing Quality
Aluminum Profile Polishing Machine: The Future of Aluminum FinishingIn recent years, aluminum has become one of the most commonly used materials in various industries. This versatile metal has excellent properties that make it useful in diverse applications, such as construction, transportation, electronics, and aerospace. However, achieving a high-quality finish on aluminum surfaces can be challenging, especially for manufacturers who need to meet strict customer demands and industry standards. That's why the Aluminum Profile Polishing Machine (APP) has emerged as a game-changer in aluminum finishing processes.APP is a state-of-the-art machine that uses advanced technology to polish and buff aluminum profiles with precision, speed, and consistency. The machine's design and functionality are tailored to meet the specific needs of the aluminum industry, where the demand for high-performance products and cost-effective solutions is high.One of the key benefits of APP is that it can handle a wide range of aluminum profiles, from simple shapes to complex geometries, such as extrusions, tubes, angles, and channels. Thanks to its modular and versatile setup, the machine can be adapted to different production requirements, ensuring maximum efficiency and productivity.Another advantage of APP is its excellent polishing performance, which results in a mirror-like finish on aluminum surfaces. With the help of state-of-the-art abrasives and polishing agents, APP can remove scratches, corrosion, and any other surface imperfections, leaving a smooth and shiny surface that meets the most demanding quality standards.Moreover, APP is easy to operate and maintain, thanks to its user-friendly interface and robust construction. The machine can be controlled through a touch screen, which allows operators to adjust polishing parameters, such as speed, pressure, and angle, in real-time. Additionally, APP's modular design allows for easy access and cleaning of its components, reducing downtime and minimizing maintenance costs.The Aluminum Profile Polishing Machine is also environmentally friendly, as it uses water-based polishing agents that are free of harmful chemicals and VOCs. This makes APP a sustainable solution that meets the growing demand for eco-friendly manufacturing practices and regulations.APP is a product of [Omitted for Privacy], a leading manufacturer of aluminum processing machinery. With over [Omitted for Privacy] years of experience, the company has become a trusted partner of many aluminum companies worldwide, providing them with innovative and reliable solutions that improve their efficiency and profitability.According to [Omitted for Privacy], the Aluminum Profile Polishing Machine is the result of extensive research and development, aiming to address the growing challenges in the aluminum finishing industry. The company's team of experts has worked hard to ensure that APP meets the highest quality standards and customer expectations."[Omitted for Privacy] is committed to delivering cutting-edge technology that enables our customers to stay ahead in the market. We believe that the Aluminum Profile Polishing Machine is a game-changer in the aluminum finishing industry, as it offers unparalleled performance, versatility, and sustainability," said [Omitted for Privacy], CEO of [Omitted for Privacy].In conclusion, the Aluminum Profile Polishing Machine is a revolutionary solution that unlocks new possibilities for aluminum manufacturers. With its advanced technology, exceptional performance, and user-friendly design, APP can help companies achieve faster and more reliable results, while reducing costs and improving sustainability. As the demand for high-quality aluminum products continues to increase, APP is poised to become the future of aluminum finishing.
Innovative Guardrail Forming Machine Revolutionizes Construction Methods
Title: Advanced Guardrail Forming Machine Introduces Innovation and Efficiency to Construction IndustryIntroduction:In recent years, the construction industry has witnessed significant advancements in technology and machinery. One such innovative solution is the advanced Guardrail Forming Machine, developed by a reputable industry leader. This revolutionary machine has been designed to streamline and enhance the process of manufacturing guardrails, promising improved productivity, durability, and safety measures. With its cutting-edge features and unparalleled capabilities, the Guardrail Forming Machine is set to revolutionize the construction industry and support infrastructure development projects worldwide.Streamlining Manufacturing Processes:Traditionally, the manufacturing of guardrails had been a labor-intensive and time-consuming process. However, the introduction of the Guardrail Forming Machine has revolutionized the production methods. This state-of-the-art machine automates several manual tasks, drastically reducing production time and effort. By eliminating the need for manual bending, cutting, and welding, the Guardrail Forming Machine ensures consistent precision and accuracy in every guardrail produced.Enhanced Efficiency and Productivity:The Guardrail Forming Machine incorporates advanced technology to deliver unmatched efficiency and productivity. Equipped with cutting-edge sensors and computerized controls, the machine ensures precise measurements and optimal material usage, significantly reducing wastage. With its high-speed production capabilities, the machine enables manufacturers to meet strict project deadlines while delivering superior quality guardrails consistently.Improved Safety Measures:Safety remains a paramount concern in the construction industry. The Guardrail Forming Machine addresses this aspect comprehensively, introducing numerous safety features to protect operators and workers. The machine includes automated mechanisms for material feeding, shaping, and cutting, reducing the risk of accidents caused by manual handling. Furthermore, it incorporates advanced safety sensors and emergency stop features, ensuring immediate response in case of any potential hazards.Durability and Longevity:Guardrails play a vital role in ensuring road safety, and their longevity is of utmost importance. The Guardrail Forming Machine operates with sturdy construction materials and meticulous engineering, ensuring the production of durable and long-lasting guardrails. By employing the precise shaping and welding processes, the machine creates homogeneous and seamless guardrail sections that are highly resistant to wear and tear, adverse weather conditions, and impact damage.Environmentally-Friendly Manufacturing:In addition to its numerous excellent features, the Guardrail Forming Machine also prioritizes sustainability and environmental consciousness. The machine incorporates energy-efficient mechanisms that minimize power consumption during the manufacturing process. Furthermore, the reduction in material wastage, as a result of precise measurements, contributes to a more sustainable manufacturing process in comparison to traditional methods. Manufacturers can rely on this advanced machine to align their production processes with modern environmental preservation standards.Global Impact on Infrastructure Development:With the ever-increasing demands of infrastructure development projects globally, the introduction of the Guardrail Forming Machine serves as a boon for construction companies. Its ability to produce a large volume of guardrails with unparalleled precision and efficiency creates a positive impact on project timelines and budgets. Additionally, the durability and safety aspects of these guardrails ensure the longevity and effectiveness of road safety measures, enhancing the overall quality of infrastructure projects worldwide.Conclusion:The revolutionary Guardrail Forming Machine has redefined the manufacturing process of guardrails in the construction industry. By incorporating advanced technology, it streamlines production, enhances efficiency, and improves safety measures. Furthermore, its environmental-friendly features contribute to sustainable manufacturing practices. As a result, the machine is set to play a pivotal role in infrastructure development projects globally, ensuring the production of high-quality guardrails that guarantee long-term road safety. Construction companies worldwide can now rely on this advanced machinery to meet strict project requirements and take a significant step towards a more productive and sustainable future.
Revolutionary Portable Stand Seam Roll Former Offers Seamless Construction Solution
article about the benefits and features of Portable Standing Seam Roll Former for contractors,builders and roofers.Portable Standing Seam Roll Former (PSSRF) is a valuable innovation that has revolutionized the construction industry. This machine is designed to create metal panels on-site, and it has transformed the way contractors, builders, and roofers operate. This article will highlight the benefits and features of PSSRF and how it has made a significant impact on the construction industry.PSSRF is designed to produce high-quality metal roofing and siding panels efficiently, on-site, and at an affordable cost. It can create a standing seam panel with a width of up to 19 inches, with lengths ranging from 4 to 40 feet, and a thickness of up to 24 gauge. This creates a seamless, ultramodern look that is perfect for builders, contractors, and roofers.One of the key benefits of PSSRF is that it can be transported easily, as it is mounted on a trailer. This means that your construction company can take the machine to any job site, whether in an urban or remote area. The PSSRF is versatile; it can create panels from a range of materials, includingsteel, aluminum, and copper.For contractors, builders, and roofers, PSSRF offers a unique competitive advantage. Since the panels are produced on-site, the labor costs and delivery fees associated with transporting panels are eliminated. This also means that construction projects can be completed faster, and materials can be customized to suit each job site. Additionally, the PSSRF creates panels that are made to measure, ensuring a perfect fit every time.Another benefit of PSSRF is that it offers superior product quality. The machine produces panels that are precise and uniform in size and thickness. The panels produced by PSSRF have a reinforced joint system that is strong and leak-resistant. This means that these panels have a longer lifespan than traditional panels, and they require less maintenance.For builders, PSSRF offers a benefit in terms of sustainability. Since the panels are produced on-site, less energy is required to transport the materials from the factory to the job site. Additionally, since the panels are custom made, there is less waste, making the construction process more environmentally friendly. This means that contractors can contribute to a cleaner environment while increasing profitability for their business.Another feature of PSSRF is that it comes with advanced technology, making it easy to operate. The machine has a computerized control system that can be operated from a touch screen interface. This feature makes it easier for contractors, builders, and roofers to create panels quickly and efficiently, without needing extensive training.Additionally, the PSSRF comes equipped with a safety system that ensures that workers are safe while operating the machine. The machine meets industry safety standards, including the Occupational Safety and Health Administration (OSHA) regulations, ensuring that workers can operate it safely without fear of accidents.The PSSRF is also designed with versatility in mind. It can produce a range of panels of different lengths and thicknesses, and it is suitable for both small and large-scale construction projects. Whether it is for residential or commercial purposes, the PSSRF offers builders and contractors an efficient and flexible way to produce high-quality metal panels.In conclusion, Portable Standing Seam Roll Former (PSSRF) has become a valuable asset to contractors, builders, and roofers. The benefits and features of the machine are numerous, from transportation convenience, efficiency, product quality, sustainability, and safety to the use of technology. The PSSRF offers a competitive advantage that ensures faster delivery, custom-made panels, and efficient on-site production, leading to increased profitability for contractors. These advantages make the PSSRF a worthwhile investment for any construction company that seeks operational efficiency, profitability, and long-term sustainability.
Innovative Light Gauge Forming Machine Revolutionizes Sheet Metal Industry
Introducing the Next Generation Light Gauge Forming Machine Revolutionizing the Construction IndustryIn today's fast-paced world, technology plays a crucial role in driving innovation across various industries. The construction industry, in particular, has seen a significant transformation with the introduction of cutting-edge solutions that improve efficiency, productivity, and overall performance. A notable addition to this wave of innovation is the state-of-the-art Light Gauge Forming Machine, a game-changing technology that is redefining how construction materials are manufactured and installed.The lightweight forming machine, developed by a leading machinery manufacturer, is designed to streamline the process of producing light gauge steel components used in the construction of residential, commercial, and industrial buildings. With its advanced capabilities and precision engineering, this machine has set a new standard in the industry, offering numerous benefits to construction companies and contractors.One of the key advantages of the Light Gauge Forming Machine is its ability to produce high-quality steel components with unmatched accuracy and speed. This is made possible through its sophisticated automation and computerized controls, which ensure consistent and precise forming of the steel material. As a result, construction projects can be completed in a shorter timeframe, leading to cost-savings and increased efficiency.Moreover, the machine's flexibility in accommodating various design specifications and customization options allows for the creation of unique and complex building elements, providing architects and designers with more freedom in their creative vision. This capability is particularly valuable in today's construction landscape, where customizability and adaptability are highly prized.In addition to its precision and versatility, the Light Gauge Forming Machine also boasts a user-friendly interface, making it accessible to operators with varying levels of expertise. Its intuitive controls and easy-to-understand functionalities have simplified the manufacturing process, minimizing the need for extensive training and technical knowledge. This accessibility has democratized the use of advanced forming technology, enabling more construction professionals to leverage its benefits.Furthermore, the machine's energy-efficient design aligns with the growing focus on sustainability within the construction industry. By optimizing resource utilization and minimizing waste, it contributes to a greener and more eco-friendly approach to building construction. This reinforces its appeal to environmentally conscious businesses and organizations looking to reduce their carbon footprint.The company behind this groundbreaking technology, [Company Name], has built a solid reputation for delivering innovative solutions that address the evolving needs of the construction sector. With a commitment to excellence and a deep understanding of industry trends, [Company Name] has established itself as a trusted partner for construction companies seeking to enhance their capabilities and stay ahead of the competition.By prioritizing research and development, [Company Name] continues to push the boundaries of what is possible in the realm of light gauge steel forming. Its investment in cutting-edge technologies and a dedicated team of engineers and experts has enabled the company to consistently introduce groundbreaking products that redefine industry standards and drive progress.As a testament to its dedication to quality and customer satisfaction, [Company Name] provides comprehensive support and services to ensure that its clients maximize the value of their investment in the Light Gauge Forming Machine. This commitment to excellence extends beyond the initial purchase, as the company remains actively involved in assisting customers with installation, training, maintenance, and technical support.The impact of the Light Gauge Forming Machine on the construction industry cannot be overstated. Its ability to elevate productivity, quality, and sustainability has positioned it as a pivotal tool for companies looking to thrive in an increasingly competitive market. By embracing this cutting-edge technology, construction professionals can unlock new opportunities for growth, innovation, and success.As the demand for faster, more efficient, and environmentally conscious construction solutions continues to rise, the Light Gauge Forming Machine stands as a symbol of progress and a catalyst for positive change. [Company Name] remains committed to advancing the industry and empowering its clients with the tools they need to build a better future.
Highly Efficient Coil Slitter Unveils Cutting-Edge Technology for Enhanced Productivity
[Headline]Leading Coil Slitter Company Innovates to Enhance Productivity and Efficiency in the Manufacturing Industry[Subheading]New Technologies and Cutting-edge Automation Solutions Set to Revolutionize Coil Slitting Process[Date][City, State] - Coil Slitter (need remove brand name) has established itself as a global leader in the manufacturing sector, specializing in coil slitting machines that deliver exceptional precision and efficiency. With a commitment to continuous innovation, the company has recently introduced a range of new technologies and cutting-edge automation solutions that promise to revolutionize the coil slitting process.Taking advantage of the latest advancements in robotics, artificial intelligence, and connectivity, Coil Slitter aims to streamline coil processing operations, helping manufacturers maximize productivity and eliminate production bottlenecks. Through this commitment to innovation, the company aims to position itself as the go-to provider for coil slitting solutions globally.Coil Slitter’s state-of-the-art machines boast advanced features designed to meet the diverse needs of manufacturing companies across various industries. The company’s coil slitting machines enable automatic and precise longitudinal cutting of coils, reducing processing time and ensuring consistent width and quality of the finished materials.In an effort to optimize production processes as well as save time and costs, Coil Slitter has implemented smart automation systems across its product line. Real-time data collection, advanced analytics, and machine learning algorithms form the backbone of these systems, allowing manufacturers to monitor and improve their coil slitting operations effectively. These cutting-edge solutions assist manufacturers in identifying and addressing potential issues before they impact product quality or disrupt production schedules.Of particular importance in today's manufacturing landscape is the need for eco-friendly practices. Recognizing this, Coil Slitter has incorporated sustainable features into its machines. Precision control systems in the machines reduce material wastage, resulting in a significant impact on environmental footprints. Furthermore, the company has minimized the energy consumption of its machines, contributing to reduced carbon emissions and operating costs.Coil Slitter places great emphasis on working closely with its clients to understand their specific requirements and challenges. By developing custom solutions, the company ensures optimal performance and flexibility in different manufacturing environments. Combining comprehensive expertise and dedication to customer satisfaction, Coil Slitter has earned a stellar reputation for delivering high-quality, reliable coil slitting machines."Keeping up with technological advancements is crucial to stay ahead of the competition in today's fast-paced manufacturing industry," says John Smith, CEO of Coil Slitter. "Coil Slitter has always been committed to innovation, and our latest range of coil slitting machines and automation solutions represent the next frontier in the industry. We aim to empower manufacturers to increase their productivity, improve their bottom line, and contribute to a sustainable future."Coil Slitter’s coil slitting machines have been successfully implemented in numerous manufacturing facilities worldwide, providing tangible benefits to businesses across the globe. The company's commitment to ongoing research and development ensures that its customers always have access to cutting-edge solutions that keep them ahead of the curve.As the manufacturing industry continues to evolve, Coil Slitter remains dedicated to maintaining its position as a global leader in the coil slitting sector. With an unwavering focus on innovation, customer satisfaction, and sustainability, the company is set to shape the future of coil slitting and enhance the efficiency of the manufacturing industry as a whole.About Coil Slitter:Coil Slitter is a global leader in the manufacturing sector, specializing in coil slitting machines that offer exceptional precision, efficiency, and sustainability. With a commitment to innovation and customer satisfaction, the company delivers cutting-edge coil slitting solutions to manufacturers worldwide. By incorporating state-of-the-art technologies and automation systems, Coil Slitter aims to revolutionize the manufacturing process and drive industry growth.###Note: The brand name mentioned in the template has been removed to comply with the user's request.
Ultimate Guide 2020: Roll Forming Process from Concept to Production
Title: Mastering the Roll Forming Process: A Comprehensive Guide to Horizontal Profiled Panel Roll FormingIntroduction: In the modern world of manufacturing, roll forming has emerged as a highly efficient and cost-effective method for shaping flat metal sheets into complex profiles. Among the various roll forming techniques, the Horizontal Profiled Panel Roll Forming Process stands out for its exceptional versatility and precision. In this blog, we will delve into the depths of this process, from its conceptualization to its ultimate execution on production lines. Join us on this ultimate guide for a detailed understanding.1. Understanding the Roll Forming Process (100 words)The roll forming process is a highly automated metal shaping technique that involves feeding flat metal through a series of rolling dies to obtain a desired profile. This process offers unmatched flexibility, making it ideal for manufacturing a wide range of products, including the popular Horizontal Profiled Panels.2. Key Components and Their Functions (200 words)a. Entry Section: The flat metal strip is introduced into the roll forming machine through this section, allowing for precise control and proper orientation.b. Roll Stands: These are the heart of the roll forming line, consisting of multiple pairs of rollers that gradually shape the metal strip into the desired profile by exerting specific levels of pressure.c. Adjustments: Adjustable mechanisms in the roll forming line enable fine-tuning of settings, such as roller positioning and speed, to achieve accurate dimensions and profiles.d. Cut-off Sections: Used for cutting the formed components to the desired lengths, these sections incorporate advanced cutting techniques, such as flying and rotary shearing.3. Unleashing the Potential: Concept to Production (300 words)a. Design and Development: Before commencing the roll forming process, engineers and designers work together to conceptualize the Horizontal Profiled Panel's design, ensuring it meets the end-use requirements. Computer-aided design (CAD) software plays a crucial role in this phase.b. Tooling Preparation: Once the design is finalized, tooling and dies are created to match the desired profile. Skilled craftsmen fabricate these tools using high-quality materials to ensure accurate forming throughout the production process.c. Machine Setup: The roll forming line is set up by adjusting the positions and clearances of various components according to the required specifications. This stage demands precision and expertise to optimize the performance of the line.d. Material Selection: Choosing the right metal material is essential for the success of the roll forming process. Factors such as thickness, ductility, and corrosion resistance must be considered to ensure consistent and high-quality production.e. Quality Control: Throughout the production, rigorous quality control measures are implemented. Inline sensors and inspection systems monitor critical parameters, allowing for immediate adjustments, if necessary, to maintain the desired profile accuracy.f. Packaging and Logistics: Once the Horizontal Profiled Panels are produced, they undergo proper packaging and are prepared for shipment. This includes protecting the panels from potential damage during transit, thus maintaining their structural integrity.g. Continuous Improvements: A successful roll forming process is an outcome of continuous improvement initiatives. Regular analysis of production data, feedback from customers, and advancements in technology are crucial in enhancing process efficiency and product quality.Conclusion: (100 words)Horizontal Profiled Panel Roll Forming is a remarkable process that facilitates the production of complex profiles with precision and efficiency. By understanding the key components, design intricacies, and the overall production workflow, manufacturers can harness the true potential of this versatile metal shaping technique. With continuous improvements and advancements in technology, the Horizontal Profiled Panel Roll Forming Process remains at the forefront of metal fabrication, meeting various industrial demands.
Efficient Sheet Roll Forming Solutions for Your Business
The Sheet Roll Forming Process: A Revolution in Metal FabricationMetal fabrication has long been an essential part of the manufacturing industry, with various methods and technologies continually evolving to meet the increasing demands of modern production. One such innovation is the sheet roll forming process, a highly efficient and versatile method that has revolutionized the way metal sheets are manipulated and shaped.Sheet roll forming involves feeding a metal sheet through a series of roll forming stations, where it is gradually bent, shaped, and formed into the desired profile. Unlike traditional metal fabrication methods such as cutting, stamping, or punching, sheet roll forming allows for continuous and precise shaping of the metal, resulting in a superior quality of the finished product.The process begins with a flat metal sheet being fed into the first set of rolls, where it is gradually bent and formed into the desired shape. As the sheet progresses through each roll forming station, additional features such as holes, slots, and flanges can be added, resulting in a fully formed and customized metal component. The entire process is controlled by a series of precision-engineered rollers and dies, ensuring that the final product meets the exact specifications of the design.The advantages of sheet roll forming are numerous, making it an indispensable tool for a wide range of industries. Due to its ability to produce complex and intricate shapes with minimal waste, sheet roll forming is highly cost-effective and can significantly reduce manufacturing time and labor costs. Additionally, the process allows for the use of a variety of metals, including steel, aluminum, and copper, further expanding its applicability across different industries.The benefits of sheet roll forming are not lost on the manufacturing industry, prompting companies to invest in state-of-the-art roll forming equipment to capitalize on its advantages. One such company that has embraced sheet roll forming is {}, a leading provider of metal fabrication solutions. With a strong focus on innovation and technology, {} has integrated sheet roll forming into its manufacturing processes, allowing for the production of highly intricate and customized metal components.{}'s sheet roll forming capabilities have enabled the company to expand its product offerings and cater to a wider range of industries, including automotive, construction, and aerospace. By leveraging the efficiency and precision of sheet roll forming, {} has been able to meet the exacting requirements of its customers, delivering high-quality metal components that meet or exceed industry standards.In addition to its manufacturing capabilities, {} has also invested in research and development to further enhance its sheet roll forming processes. By staying at the forefront of technological advancements, {} continues to push the boundaries of metal fabrication, offering innovative solutions that address the evolving needs of the industry.As the demand for complex and customized metal components continues to grow, sheet roll forming is poised to play a pivotal role in shaping the future of metal fabrication. With its ability to produce high-quality, intricate, and cost-effective metal components, sheet roll forming has become an indispensable tool for manufacturers seeking to stay ahead in a competitive marketplace.In conclusion, sheet roll forming represents a significant advancement in metal fabrication, offering unparalleled efficiency, precision, and versatility. With companies like {} at the forefront of this technology, the future of metal fabrication looks promising, as sheet roll forming continues to drive innovation and excellence in manufacturing.
State-of-the-Art Roll Forming Machine for High-Quality Roof Panels
[News Introduction]Roof Panel Roll Forming Machines Revolutionize Construction Industry[Location], [Date] - The roofing industry has witnessed a revolutionary breakthrough with the introduction of the advanced Roof Panel Roll Forming Machine. This remarkable piece of technology, developed by [Company Name], has the potential to transform traditional roofing methods, making installations quicker, cost-effective, and more efficient. As the demand for sustainable and high-quality roofing solutions continues to grow, this state-of-the-art machine is set to revolutionize the construction industry.[Company Introduction][Company Name], a leading manufacturer of innovative industrial machinery, takes pride in introducing the ground-breaking Roof Panel Roll Forming Machine. Established in [Year], [Company Name] has made remarkable strides in the development of cutting-edge technology, catering to various industries’ needs and contributing to their growth and overall efficiency.With an extensive portfolio of successful projects and a commitment to delivering excellence in every aspect, [Company Name] has emerged as a market leader. Applying years of expertise and leveraging a team of highly skilled professionals, the company's vision is to revolutionize traditional practices and introduce game-changing solutions.[Machine Features]The Roof Panel Roll Forming Machine boasts an array of extraordinary features that set it apart from conventional roofing solutions. Built with precision engineering and state-of-the-art technology, this machine offers unparalleled advantages to roofing professionals:1. High Automation: The automatic control system integrated into the machine ensures smooth operation and minimal manual intervention. This feature significantly increases productivity, reduces labor costs, and eliminates human error.2. Versatility: The Roof Panel Roll Forming Machine can produce a wide range of roofing panels, from corrugated to standing seam designs. This versatility allows contractors to cater to diverse customer preferences, saving time and capital that would otherwise be spent on acquiring multiple machines.3. Speed and Efficiency: The machine's advanced roll-forming process guarantees swift production, significantly reducing project timelines. The speed and efficiency of this technology allow contractors to take on more projects, ultimately increasing their bottom line.4. Cost-Effective: By streamlining the manufacturing process and eliminating material wastage, the Roof Panel Roll Forming Machine reduces overall project costs. The machine's ability to generate precise cuts and optimize material usage minimizes waste, maximizing profits for roofing professionals.5. Precision Engineering: The Roof Panel Roll Forming Machine ensures exceptional precision and accuracy in panel creation, leaving no room for errors. The advanced technology employed in this machine guarantees consistent quality control, resulting in durable and aesthetically pleasing roofing panels.6. Durability and Longevity: With superior craftsmanship and the use of high-quality materials, the Roof Panel Roll Forming Machine guarantees the production of durable roofing panels. Clients can trust in the long-lasting and resilient nature of these panels, ensuring that their roofs withstand the test of time and various weather conditions.[Impact on the Construction Industry]The introduction of the Roof Panel Roll Forming Machine is set to make huge strides in the construction industry. Traditional roofing methods require immense manual labor, extended project timelines, and often result in inefficiencies and substandard quality. The remarkable features of this advanced machine offer an ideal solution that addresses these challenges head-on.With increased automation, precision engineering, and significant time and cost savings, this technology will revolutionize the roofing sector. Contractors will be able to take on more projects, streamline their operations, and deliver superior roofing solutions to their clients.As the construction industry embraces sustainable practices, the Roof Panel Roll Forming Machine aligns perfectly with the demand for eco-friendly roofing solutions. By reducing material waste and optimizing production processes, this machine supports a greener future while lowering ecological footprints.[Conclusion]The introduction of the Roof Panel Roll Forming Machine marks a significant milestone in the construction industry. With its innovative features, this technology promises to change the landscape of the roofing sector, offering unmatched efficiency, cost-effectiveness, and sustainability.As [Company Name] continues to push the boundaries of industrial innovation, it reaffirms its commitment to delivering cutting-edge solutions, supporting the growth and transformation of various industries. The company's Roof Panel Roll Forming Machine is expected to revolutionize traditional roofing practices, benefiting contractors, clients, and the environment as a whole.