Highly Efficient Rolling Forming Machine for Studs
By:Admin
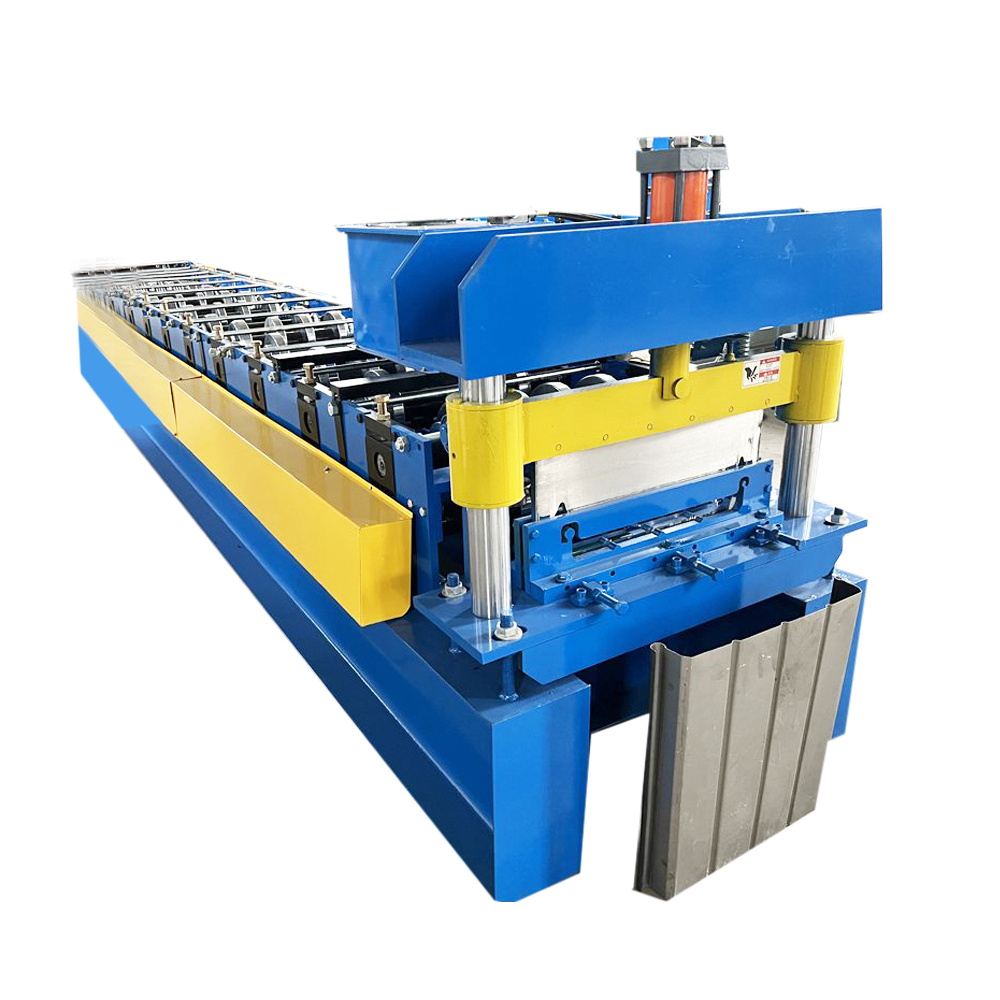
The construction industry is constantly evolving, with new technologies and innovations aimed at improving efficiency and productivity. One such innovation that is making waves in the industry is the Stud Rolling Forming Machine, a state-of-the-art equipment that is changing the way construction projects are executed.
The Stud Rolling Forming Machine, developed by a leading machinery company, is designed to streamline the process of forming studs, which are an essential component in the construction of various structures, from residential buildings to commercial establishments. Traditionally, forming studs required extensive manual labor and a significant amount of time, leading to delays and increased labor costs. However, with the introduction of the Stud Rolling Forming Machine, this process has been revolutionized, enabling construction companies to significantly improve their efficiency and productivity.
The machine's advanced technology and precision engineering allow for the seamless and rapid production of studs, eliminating the need for manual labor and reducing the likelihood of errors. This not only leads to cost savings for construction companies but also ensures that the quality of the studs produced is consistently high, ultimately contributing to the overall safety and stability of the structures being built.
Furthermore, the Stud Rolling Forming Machine is versatile and adaptable, capable of producing studs in various sizes and specifications to cater to the specific requirements of different construction projects. This flexibility makes it an invaluable asset for construction companies, as it enables them to effectively meet the diverse needs of their clients without compromising on quality or efficiency.
In addition to its technical capabilities, the Stud Rolling Forming Machine is also designed with user-friendliness in mind, featuring intuitive controls and interface that make it easy for operators to understand and operate the machine effectively. This ensures that construction companies can seamlessly integrate the machine into their existing operations without the need for extensive training or retooling, further contributing to its appeal and practicality.
The company behind the Stud Rolling Forming Machine has a long-standing reputation for excellence in manufacturing and engineering, with a track record of developing cutting-edge machinery that has significantly impacted various industries. Their commitment to innovation and quality is reflected in the design and performance of the Stud Rolling Forming Machine, which has quickly gained recognition and acclaim within the construction industry.
With a focus on continuous improvement and customer satisfaction, the company has invested significant resources into research and development, ensuring that the Stud Rolling Forming Machine remains at the forefront of technological advancements and is poised to meet the evolving needs of the construction industry.
In response to the overwhelmingly positive reception of the Stud Rolling Forming Machine, the company has also established a comprehensive support infrastructure, providing training, maintenance, and technical assistance to ensure that construction companies can fully maximize the potential of the machine and achieve optimal results in their projects. This commitment to customer service further underscores the company's dedication to driving positive change and progress within the construction industry.
As the construction industry continues to evolve and embrace new technologies, the Stud Rolling Forming Machine stands out as a game-changer that is reshaping the way studs are formed and utilized in construction projects. With its innovative design, efficiency, and performance, it has quickly become an indispensable tool for construction companies seeking to enhance their operations and deliver superior results to their clients.
In conclusion, the Stud Rolling Forming Machine represents a significant milestone in the advancement of construction technology, and its impact on the industry is set to be long-lasting and transformative. As more construction companies recognize the benefits and advantages it offers, its adoption is expected to become increasingly widespread, further solidifying its status as a game-changing innovation that is revolutionizing the construction industry.
Company News & Blog
High-Quality Color Steel Roll Forming Machine for GP GI Materials
{Company Name} is a leading manufacturer of roll forming machines, specializing in the production of high-quality and efficient machines to meet the needs of various industries. With a strong focus on innovation and technology, the company has consistently delivered state-of-the-art roll forming machines that have set industry standards.The latest addition to {Company Name}’s impressive lineup of roll forming machines is the GP GI Color Steel Roll Forming Machine. This machine is designed to meet the growing demand for high-quality and durable steel roll forming solutions. With its advanced features and precise engineering, the GP GI Color Steel Roll Forming Machine is set to revolutionize the steel forming industry.One of the key features of the GP GI Color Steel Roll Forming Machine is its ability to produce a wide range of steel profiles with precision and speed. The machine is equipped with advanced roll forming technology that allows for the quick and efficient production of high-quality steel products. This versatility makes the GP GI Color Steel Roll Forming Machine an ideal choice for companies looking to expand their product offerings and meet the diverse needs of their customers.In addition to its impressive production capabilities, the GP GI Color Steel Roll Forming Machine is also designed with user-friendly features that make operation and maintenance simple and efficient. This includes a user-friendly interface, easy-to-access components, and a durable construction that ensures longevity and reliability. With these features, operators can maximize productivity and minimize downtime, leading to greater profitability and customer satisfaction.Another standout feature of the GP GI Color Steel Roll Forming Machine is its ability to produce steel products with superior surface quality and color consistency. This is achieved through the machine's advanced color coating technology, which ensures that the final products have a consistent and vibrant color finish. This is a crucial advantage for companies that require high-quality steel products with a premium aesthetic appeal.Furthermore, the GP GI Color Steel Roll Forming Machine is designed with efficiency and sustainability in mind. The machine is equipped with energy-saving features and operates with minimal waste, making it an environmentally friendly choice for companies looking to reduce their carbon footprint and operating costs.As a trusted leader in the roll forming industry, {Company Name} is committed to providing comprehensive support and service for the GP GI Color Steel Roll Forming Machine. The company offers on-site installation, training, and ongoing technical assistance to ensure that customers can maximize the potential of their investment. This dedication to customer satisfaction and support further solidifies {Company Name}’s reputation as a reliable and value-driven partner in the industry.With the introduction of the GP GI Color Steel Roll Forming Machine, {Company Name} continues to uphold its reputation as a forward-thinking innovator in the roll forming industry. The machine's advanced features, precision engineering, and user-friendly design make it a standout choice for companies looking to elevate their steel forming capabilities and stay ahead of the competition.In conclusion, the GP GI Color Steel Roll Forming Machine from {Company Name} represents a significant advancement in the roll forming industry. With its advanced technology, versatility, and user-friendly design, this machine is set to redefine the standards for steel roll forming, providing companies with a reliable and efficient solution for their production needs. As {Company Name} continues to push the boundaries of innovation, the GP GI Color Steel Roll Forming Machine stands as a testament to the company's commitment to excellence and customer satisfaction.
Roll Forming Machine, Cold Roll Forming Machine, Sandwich Panel Machine, Roof Tile Roll Forming Machine, Wall Panel Roll Forming Machine, Steel Roll Forming Machine, Glazed Tile Roll Forming Machine, Ridge Cap Roll Forming Machine, IBR Roll Forming Machine, Corrugated Roll Forming Machine, Floor Deck Roll Forming Machine, Highway Guardrail Roll Forming Machine, Stud and Track Roll Forming Machine, Furring Channel Roll Forming Machine, Downpipe Roll Forming Machine, Gutter Machine, Roller Shutter Door Forming Machine, K Span Roll Forming Machine, Door Frame Roll Forming Machine, Standing Seam Roof Panel Roll Forming Machine, Bemo Panel Roll Forming Machine, Shelf Roll Forming Machine, Cable Tray Roll Forming Machine, Slitting & Cutting Machine, Roof Curving Machine, Embossing Machine
Title: Innovations in Roll Forming Machines - Revolutionizing Construction IndustryIntroduction:In the rapidly evolving construction industry, the use of advanced machinery and equipment has become crucial to enhance productivity and efficiency. Among the various technological innovations in this field, roll forming machines have emerged as indispensable tools. These machines play a pivotal role in the production of metal sheets and panels used in roofing, wall cladding, and other construction applications.Roll Forming Machine: Transforming Metal Sheets with PrecisionRoll forming machines, also known as roll formers, are highly versatile manufacturing machines used to transform flat metal sheets into complex and customized profiles used in construction. They utilize a continuous bending operation by passing the sheet metal through a series of rolling dies. The process involves shaping the metal into a desired cross-section profile while maintaining uniform thickness throughout the length.Cold Roll Forming Machine: Enhancing Precision and DurabilityCold roll forming machines have gained immense popularity due to their ability to work with a wide range of materials, including steel, aluminum, copper, and more. This type of roll forming machine operates at room temperature, minimizing the risk of thermal damage to the metal. Cold roll forming ensures higher uniformity in the end products, offering superior dimensional accuracy, strength, and durability.Sandwich Panel Machine: Efficient Insulation SolutionsThe use of sandwich panels in construction has gained significant traction, primarily due to their excellent thermal and sound insulation properties. Sandwich panel machines are specifically designed to produce panels with an insulating core material, such as EPS (Expanded Polystyrene), rock wool, or mineral wool, sandwiched between two outer sheets. These panels find applications in roofing, wall cladding, and other structural elements, offering energy efficiency and environmental benefits.Revolutionizing the Manufacturing Process:- EPS/Rock wool/Mineral wool sandwich panel machine: This advanced technology enables the efficient production of insulated panels, offering enhanced temperature regulation and noise reduction in buildings.- Glazed Tile Roll Forming Machine: Utilizing high-quality materials, this machine produces aesthetically appealing glazed tiles for roofing applications. The precise roll forming process ensures dimensional accuracy and long-lasting performance.- Standing Seam Roof Panel Roll Forming Machine: This machine revolutionizes the production of standing seam roof panels, which are popular for their exceptional weather resistance and stylish appearance.- Double Layer Roll Forming Machine: Ideal for large-scale projects, this machine efficiently produces two different profiles simultaneously, reducing production time and costs.- Highway Guardrail Roll Forming Machine: As road safety remains a paramount concern, this machine manufactures sturdy guardrails, protecting motorists and minimizing accidents.Expanding Possibilities with Advanced Features:Modern roll forming machines come equipped with advanced features such as computer numerical control (CNC) systems, automated feeders, and precision cutting mechanisms, ensuring high productivity, reliability, and time efficiency. These features allow for customization and adaptation to different profile designs.Conclusion:The roll forming machine industry has witnessed substantial advancements in recent years, fueling innovative manufacturing processes in the construction sector. The introduction of cold roll forming machines, sandwich panel machines, and other specialized equipment has enabled the production of high-quality, customized metal profiles and panels. As technology continues to evolve, these machines will play a vital role in shaping the infrastructure of our future.For further information or inquiries, interested parties are encouraged to contact Ms. Monica Lee, who will provide detailed information and the best prices for the required profile drawings or specifications.Contact Person: Ms. Monica LeeWebsite: (brand name removed)Disclaimer: This news content is for information purposes only and does not serve as an endorsement for any specific brand or company.
High-Quality Glazed Tile Roll Forming Machine Supplier in China - Extensive Product Range
Title: Enhancing Roof Aesthetics with Color Steel Glazed Tile Roof Panel Roll FormerIntroductionWith the growing popularity of glazed tile roofing panels, both in residential and commercial buildings, the demand for efficient and reliable machinery that can manufacture them is on the rise. In this blog post, we will explore the benefits and features of a Color Steel Glazed Tile Roof Panel Roll Former, which is a leading product in the market. This advanced roll forming machine allows manufacturers to produce high-quality glazed tile roof panels with ease. Section 1: Understanding Glazed Tile Roll Forming MachineA Glazed Tile Roll Forming Machine is a specialized equipment designed to transform raw materials, typically color steel, into glazed tile roof panels. This roll forming process involves feeding the steel sheet through a series of rollers that gradually shape and form the desired profile. The result is a strong, aesthetically pleasing, and weather-resistant tile, perfect for enhancing the overall appearance of any building.Section 2: Key Features and Advantages2.1. Precision Manufacturing: The Color Steel Glazed Tile Roof Panel Roll Former ensures precise molding and sizing of glazed tile panels, thanks to its innovative design and cutting-edge technology. The machine guarantees consistent panel quality, reducing the chances of any defects or inconsistencies.2.2. Versatility: This roll forming machine can manufacture various styles and profiles of glazed tiles, catering to the diverse needs of customers. From traditional curved designs to modern flat styles, the machine offers exceptional flexibility and customization options.2.3. Efficiency and Speed: With the ability to operate at high speeds, the roll former significantly increases productivity, allowing manufacturers to meet tight production deadlines. The fast and efficient production process helps minimize labor costs and maximize overall output.2.4. Durability: The construction of the Color Steel Glazed Tile Roof Panel Roll Former is robust and durable, ensuring a longer lifespan. Its strong framework and high-quality components enable continuous and reliable operation, reducing downtimes and maintenance requirements.Section 3: Benefits for Manufacturers3.1. Cost-Effective Solution: Investing in a Glazed Tile Roll Forming Machine eliminates the need for outsourcing tile manufacturing, resulting in substantial cost savings for manufacturers in the long run. The machine's high efficiency and minimal material wastage contribute to further economic advantages.3.2. High-Quality Output: The precision and consistency offered by the roll former ensure that every glazed tile produced is of superior quality. Manufacturers can deliver a premium product that meets the market's high standards, enhancing their reputation and customer satisfaction.3.3. Customization Possibilities: The versatility of the machine enables manufacturers to cater to specific customer requirements. From different colors to various tile sizes and profiles, customization options are limitless, allowing for greater market competitiveness.3.4. Reduced Carbon Footprint: As the Color Steel Glazed Tile Roof Panel Roll Former operates based on energy-efficient principles, it helps reduce the overall carbon footprint of manufacturers. This commitment to sustainability aligns with the growing demand for eco-friendly construction materials and practices.ConclusionInvesting in a Color Steel Glazed Tile Roof Panel Roll Former is a wise choice for manufacturers aiming to expand their product offerings, increase productivity, and enhance the overall quality of their glazed tile roof panels. With its precision manufacturing, versatility, efficiency, and durability, this robust machinery can take roofing aesthetics and functionality to new heights. By embracing modern roll forming technology, manufacturers can stay ahead of the competition and meet the ever-growing demand for glazed tile roofing products.
High-quality Cold Roller Former for Efficient Metal Processing
Cold Roller Former, a cutting-edge technology developed by a leading manufacturing company, is making waves in the industry with its innovative and efficient cold rolling process. This revolutionary machine is designed to shape metallic materials into various components, providing a cost-effective and high-quality solution for a wide range of applications.The cold rolling process is a critical step in metal forming, as it helps to improve the surface finish and mechanical properties of the material. Unlike traditional hot rolling, cold rolling occurs at room temperature, which results in a smoother and more precise finish. This method is particularly important for industries such as automotive, aerospace, and construction, where the quality and integrity of the metal components are paramount.With the introduction of Cold Roller Former, manufacturers can now benefit from a streamlined and advanced cold rolling process. This machine is equipped with state-of-the-art technology, including precision control systems and high-speed capabilities, allowing for the efficient production of complex and high-quality components. Additionally, its modular design and customizable features make it adaptable to various production needs, providing flexibility and versatility to manufacturers.One of the key advantages of Cold Roller Former is its ability to produce parts with tighter tolerances and improved surface finish, resulting in higher precision and quality. This is particularly beneficial for industries that require components with intricate geometries and superior mechanical properties. With Cold Roller Former, manufacturers can achieve a level of consistency and accuracy that is not possible with traditional cold rolling methods, leading to enhanced product performance and reliability.Furthermore, Cold Roller Former is designed with efficiency in mind, offering a significant increase in productivity and cost savings for manufacturers. Its high-speed capabilities and advanced control systems enable faster production cycles and reduced material waste, resulting in a more streamlined and economical manufacturing process. This not only helps to improve the overall competitiveness of manufacturers but also contributes to a more sustainable and environmentally friendly production environment.In addition to its technological advancements, Cold Roller Former is backed by a dedicated team of experts who provide comprehensive support and expertise to ensure the successful implementation and operation of the machine. From initial consultation to ongoing maintenance and training, the company's commitment to customer satisfaction and knowledge sharing sets a new standard for excellence in the industry.As a testament to its success, Cold Roller Former has already made significant strides in the market, garnering attention and accolades from industry experts and customers alike. Its proven track record of delivering superior performance, cost-effectiveness, and reliability has positioned it as the go-to solution for manufacturers seeking to elevate their cold rolling capabilities.Looking ahead, the company is committed to further advancing and enhancing Cold Roller Former to meet the evolving needs of the industry. With ongoing research and development efforts, the company is dedicated to pushing the boundaries of cold rolling technology, ultimately redefining the standards of excellence and innovation in metal forming.In conclusion, Cold Roller Former represents a significant breakthrough in cold rolling technology, offering a game-changing solution for the manufacturing industry. With its advanced capabilities, efficiency, and reliability, this revolutionary machine is poised to shape the future of cold rolling and set a new benchmark for excellence in metal forming.
Cutting-Edge Metal Roof Tile Making Machinery: Simplifying Roofing Solutions
[CompanyName], a leading manufacturer of metal roof tile making machines, has recently launched their latest innovation in the field of roofing technology. The new machine, which combines cutting-edge features with utmost reliability, is set to revolutionize the roof tile manufacturing industry.With an increasing demand for durable and energy-efficient roofing solutions, Metal Roof Tile Making Machine is designed to meet the evolving needs of builders and homeowners alike. This innovative machine utilizes state-of-the-art technology to produce high-quality metal roof tiles that are both visually appealing and highly functional.One of the key features of this advanced machine is its ability to produce roof tiles with precision and consistency. Equipped with cutting-edge automation technology, every tile produced by the machine is perfectly shaped and sized, ensuring seamless installation and a uniform appearance on the roof. This precision is highly valued by customers, as it eliminates the need for manual adjustments and guarantees a hassle-free roofing experience.Moreover, Metal Roof Tile Making Machine emphasizes the importance of durability in their product. The machine is engineered to withstand the rigors of continuous operation and is built to last. Every component of the machine is robustly constructed, ensuring that it can handle heavy workloads without compromising its performance or reliability. This feature is particularly essential for manufacturers who aim to maximize productivity and reduce downtime.In addition to its durability, this cutting-edge machine incorporates various energy-saving features that align with global efforts to promote sustainability. Metal Roof Tile Making Machine emphasizes the use of eco-friendly materials and processes, ensuring that the production of roof tiles has a minimal impact on the environment. By implementing energy-efficient practices, manufacturers can reduce their carbon footprint and contribute to a greener future.Furthermore, Metal Roof Tile Making Machine ensures customer satisfaction by offering technologically advanced controls that enable easy operation and optimization of the machine's performance. The intuitive user interface allows operators to monitor and adjust various parameters, ensuring that the machine operates at its optimal efficiency. This feature enables manufacturers to maximize their output while maintaining the highest quality standards.Metal Roof Tile Making Machine has established itself as a trusted brand in the industry. With years of experience and a commitment to excellence, the company has garnered a loyal customer base that spans across the globe. By consistently delivering superior products and exceptional customer service, Metal Roof Tile Making Machine has become a go-to choice for manufacturers and contractors seeking reliable and efficient roof tile manufacturing solutions.As the demand for metal roof tiles continues to rise, Metal Roof Tile Making Machine remains at the forefront of innovation in the industry. The company's unwavering dedication to research and development ensures that their machines embody the latest advancements in technology and meet the evolving needs of customers. With their latest offering, Metal Roof Tile Making Machine has once again set a new standard for excellence in the roofing industry.In conclusion, Metal Roof Tile Making Machine has launched a state-of-the-art machine that combines advanced features, durability, and energy efficiency. This innovation is set to revolutionize the roof tile manufacturing industry by providing manufacturers with a reliable and efficient solution to meet the growing demand for metal roof tiles. With its commitment to quality, sustainability, and customer satisfaction, Metal Roof Tile Making Machine continues to cement its place as an industry leader in roofing technology.
High-Quality Automatic Cut-To-Length Machine for Precision Cutting
Automatic Cut-To-Length Machine Revolutionizing Production ProcessThe manufacturing industry is continuously evolving with the advancement of technology, and one company at the forefront of this evolution is {}. With a commitment to innovation and efficiency, they have recently introduced their latest addition to their production line – the Automatic Cut-To-Length Machine. This state-of-the-art machine is set to revolutionize the production process, offering precision, speed, and enhanced productivity.The Automatic Cut-To-Length Machine is designed to streamline the process of cutting materials to specific lengths, catering to the diverse needs of various industries such as automotive, construction, and appliances. This machine is equipped with advanced features that enable it to effortlessly cut different materials including metals, plastics, and composites with utmost accuracy and consistency.One of the key highlights of the Automatic Cut-To-Length Machine is its cutting-edge technology that allows for automated operation. This not only reduces the need for manual labor but also minimizes the margin of error, resulting in higher quality output. Additionally, with its rapid cutting speed, the machine significantly increases production efficiency, ultimately leading to cost savings for the company.Furthermore, the Automatic Cut-To-Length Machine is integrated with intelligent software that enables precise customization and optimization of cutting processes. This ensures that the machine can meet the specific requirements of each customer, catering to a wide range of dimensions and tolerances. With such versatility, the machine offers a competitive edge in the market, allowing {} to provide tailored solutions to meet the unique demands of their clients.In addition to its technical capabilities, the Automatic Cut-To-Length Machine is designed with the operator in mind. Its user-friendly interface and intuitive controls make it easy to operate, minimizing the need for extensive training and ensuring seamless integration into the production line. This not only enhances the overall efficiency of the manufacturing process but also creates a safer working environment for the operators.{} has a long-standing reputation for delivering high-quality, reliable machinery, and the introduction of the Automatic Cut-To-Length Machine is a testament to their commitment to continuous improvement and innovation. With a strong focus on research and development, the company has invested heavily in advancing their technological capabilities, ensuring that they remain at the forefront of the industry.The launch of the Automatic Cut-To-Length Machine underscores {}'s dedication to meeting the evolving needs of their customers. By incorporating cutting-edge technology and automation into their production line, they are not only enhancing their own operational efficiency but also empowering their clients to achieve greater success in their respective industries.Moreover, the introduction of the Automatic Cut-To-Length Machine aligns with {}'s long-term sustainability goals. By optimizing the cutting process and reducing material waste, the machine contributes to a more environmentally friendly manufacturing approach. This reflects {}'s commitment to conducting business in a responsible and ethical manner, prioritizing sustainability and resource efficiency.With the introduction of the Automatic Cut-To-Length Machine, {} is poised to set new standards within the manufacturing industry. By leveraging cutting-edge technology and innovation, they are not just meeting the current demands of the market but also shaping the future of production processes. As the industry continues to evolve, {} remains dedicated to pushing boundaries and redefining what is possible in manufacturing.
How to Build a Sheet Metal Barn in 6 Simple Steps
Title: How to Build a Sheet Metal Barn in 6 Easy StepsIntroduction:Sheet metal barns provide an excellent solution for storage and shelter needs. Not only are they durable and cost-effective, but they can also be constructed relatively easily. In this article, we will outline a step-by-step guide on how to build a sheet metal barn in six simple steps. Whether you have experience in construction or are a DIY enthusiast, this guide will help you create your very own sheet metal barn.Step 1: Planning and PreparationBefore starting any project, careful planning is essential. Determine the size and design of your barn based on your requirements. Take measurements of the desired area and sketch out the barn's layout. Consult local building codes and acquire any necessary permits. Once you have a clear plan, gather the required materials.Step 2: Foundation and Frame ConstructionCreate a solid foundation for your sheet metal barn. Excavate the area, level the ground, and lay a sturdy foundation using concrete or treated wood. Next, construct the frame using the plywood pallets. Cut them to the desired size and connect them securely using screws and nuts, ensuring stability and durability.Step 3: Installing RoofingSelect the appropriate sheet metal for the roofing of your barn. Galvanized sheet metal provides excellent protection against rust and corrosion. Measure and cut the sheet metal to fit the roof frame, leaving a slight overhang for drainage. Secure the roofing sheets to the frame using screws or nails, ensuring proper alignment and sealing.Step 4: Wall ConstructionMeasure and cut additional plywood panels to serve as walls for your sheet metal barn. Attach them securely to the frame, leaving space for doors and windows as needed. Ensure tight joints and smooth surfaces for a professional finish.Step 5: Doors and WindowsInstall suitable doors and windows into the wall structure. Depending on your requirements, you can choose ready-made options or customize your own. Ensure proper insulation and weatherproofing to protect your belongings from the elements.Step 6: Finishing TouchesTake time to inspect your sheet metal barn for any loose screws or nails. Replace or tighten them as necessary. Consider adding ventilation systems, gutters, or additional storage options such as shelves or hooks. Apply a protective finish, such as paint or weather-resistant coatings, to increase the longevity and aesthetics of your barn.Conclusion:Building a sheet metal barn is a satisfying project that offers both functionality and durability. By following these six easy steps, you can construct your own barn and enjoy the benefits of efficient storage and shelter. Whether you are a DIY enthusiast or a seasoned builder, creating a sheet metal barn can be achieved with the right materials, tools, and patience. Embrace your creativity and get started on your own sheet metal barn project today!
Highly Efficient Rolling Forming Machine for Profile Manufacturing
Profile Rolling Forming Machine Revolutionizes the Manufacturing IndustryIn today's fast-paced industrial landscape, the need for efficient and reliable machinery has never been more critical. Companies across various sectors are constantly seeking innovative solutions that not only enhance productivity but also ensure top-notch quality. One such groundbreaking development comes in the form of the Profile Rolling Forming Machine, a technology that has taken the manufacturing industry by storm.Profile Rolling Forming Machine utilizes state-of-the-art techniques to produce high-precision profiles in a cost-effective manner. By employing a unique rolling process, this cutting-edge machine enables the creation of complex profiles from a wide range of materials, including metal, plastic, and composite materials. This revolutionary technology has garnered significant attention and is set to have a major impact on multiple industries.One key advantage of the Profile Rolling Forming Machine lies in its ability to produce profiles with exceptional accuracy and uniformity. Traditionally, manufacturing complex profiles involves various time-consuming and labor-intensive processes, such as casting, cutting, and shaping. However, with the advent of this new technology, these conventional methods are being replaced by a streamlined process that guarantees superior precision.The Profile Rolling Forming Machine's rolling process starts with a specially designed set of rolls that gradually shape the material into the desired profile. This continuous bending and rolling operation not only ensures an impeccable finish but also eliminates the need for excessive material wastage. The precision and efficiency of this process significantly reduce production costs and enhance overall productivity.Additionally, the Profile Rolling Forming Machine offers immense flexibility in terms of profile customization. With its advanced computer-controlled system, users can easily program the machine to produce profiles of various shapes and dimensions, catering to unique design requirements. This versatility has opened up several opportunities for manufacturers, enabling them to manufacture highly intricate profiles that were previously deemed unachievable.Furthermore, this groundbreaking technology excels in both small-scale and large-scale production. The Profile Rolling Forming Machine can efficiently handle both small batches and high-volume production, making it suitable for a wide range of applications. From automotive components to architectural elements, this innovation has the potential to revolutionize numerous industries that rely heavily on complex profile production.Moreover, the Profile Rolling Forming Machine offers enhanced productivity by minimizing downtime and maintenance requirements. The robust design of this machine ensures prolonged usage without compromising on performance. Advanced sensors integrated into the machinery provide real-time data about the process, enabling operators to detect any issues promptly and take corrective measures, thereby reducing production delays.In conclusion, the Profile Rolling Forming Machine represents an exciting breakthrough in the manufacturing industry. With its unmatched precision, flexibility, and scalability, this innovative technology has the power to revolutionize the way complex profiles are produced. As industries strive for greater efficiency and productivity, the Profile Rolling Forming Machine emerges as a game-changer, providing manufacturers with the means to achieve exceptional quality while optimizing costs. Embracing this technology will undoubtedly propel businesses to the forefront of their respective industries, opening new avenues for growth and advancement.
Efficient Sheet Roll Forming Solutions for Your Business
The Sheet Roll Forming Process: A Revolution in Metal FabricationMetal fabrication has long been an essential part of the manufacturing industry, with various methods and technologies continually evolving to meet the increasing demands of modern production. One such innovation is the sheet roll forming process, a highly efficient and versatile method that has revolutionized the way metal sheets are manipulated and shaped.Sheet roll forming involves feeding a metal sheet through a series of roll forming stations, where it is gradually bent, shaped, and formed into the desired profile. Unlike traditional metal fabrication methods such as cutting, stamping, or punching, sheet roll forming allows for continuous and precise shaping of the metal, resulting in a superior quality of the finished product.The process begins with a flat metal sheet being fed into the first set of rolls, where it is gradually bent and formed into the desired shape. As the sheet progresses through each roll forming station, additional features such as holes, slots, and flanges can be added, resulting in a fully formed and customized metal component. The entire process is controlled by a series of precision-engineered rollers and dies, ensuring that the final product meets the exact specifications of the design.The advantages of sheet roll forming are numerous, making it an indispensable tool for a wide range of industries. Due to its ability to produce complex and intricate shapes with minimal waste, sheet roll forming is highly cost-effective and can significantly reduce manufacturing time and labor costs. Additionally, the process allows for the use of a variety of metals, including steel, aluminum, and copper, further expanding its applicability across different industries.The benefits of sheet roll forming are not lost on the manufacturing industry, prompting companies to invest in state-of-the-art roll forming equipment to capitalize on its advantages. One such company that has embraced sheet roll forming is {}, a leading provider of metal fabrication solutions. With a strong focus on innovation and technology, {} has integrated sheet roll forming into its manufacturing processes, allowing for the production of highly intricate and customized metal components.{}'s sheet roll forming capabilities have enabled the company to expand its product offerings and cater to a wider range of industries, including automotive, construction, and aerospace. By leveraging the efficiency and precision of sheet roll forming, {} has been able to meet the exacting requirements of its customers, delivering high-quality metal components that meet or exceed industry standards.In addition to its manufacturing capabilities, {} has also invested in research and development to further enhance its sheet roll forming processes. By staying at the forefront of technological advancements, {} continues to push the boundaries of metal fabrication, offering innovative solutions that address the evolving needs of the industry.As the demand for complex and customized metal components continues to grow, sheet roll forming is poised to play a pivotal role in shaping the future of metal fabrication. With its ability to produce high-quality, intricate, and cost-effective metal components, sheet roll forming has become an indispensable tool for manufacturers seeking to stay ahead in a competitive marketplace.In conclusion, sheet roll forming represents a significant advancement in metal fabrication, offering unparalleled efficiency, precision, and versatility. With companies like {} at the forefront of this technology, the future of metal fabrication looks promising, as sheet roll forming continues to drive innovation and excellence in manufacturing.
Flat Roof Rubber Sheet: Unparalleled Corrugated Metal Roof for Pergolas Unmatched Corrugated Metal Roofing Sheets in Scotland Tile Effect Metal Roofing Sheets, Radiant Barrier Material, Galvanized Steel Sheet Metal, Wood Support Brackets, Eagle Carports, Target Stand, Colored Metal Panels, Mono Pitch Roof Calculator, Tom Roof, Charcoal Roof Tiles, Corrugated Colorbond Sheets: The Ultimate Solution Premium Quality Flat Roof Rubber Sheet for Your Roofing Needs
Title: A New Approach to Roofing Solutions: Horizontal Corrugated Roof PanelIntroduction:In a world where sustainability and durability are becoming paramount, the roofing industry has witnessed tremendous advancements. This article focuses on an innovative product, the Horizontal Corrugated Roof Panel, offered by (need to remove brand name), which aims to revolutionize traditional roofing solutions. With its exceptional features and benefits, this unique product has garnered significant attention in the market.A Versatile Solution for All: The Horizontal Corrugated Roof Panel offers versatility in terms of its applications. The product is designed to cater to various roofing needs, including pergolas, carports, and commercial and residential buildings. Whether it's a traditional or contemporary architectural design, this panel effortlessly complements any structure, showcasing its adaptability.Unmatched Durability and Longevity:One significant advantage of the Horizontal Corrugated Roof Panel is its exceptional durability. Made of high-quality galvanized steel sheet metal, this product offers unparalleled strength and resistance against harsh weather conditions, including heavy rains, intense UV exposure, and strong winds. Additionally, the panel's unique design ensures its longevity, offering a sustainable roofing solution that requires minimal maintenance.Enhancing Energy Efficiency:The Horizontal Corrugated Roof Panel is a high-performance roofing material that integrates a radiant barrier material within its structure. This innovative feature reflects heat away from the structure, reducing the amount of heat transferred inside. As a result, buildings experience improved energy efficiency, reducing the reliance on HVAC systems and resulting in substantial energy cost savings.Aesthetically Pleasing and Customizable:Gone are the days when roofing sheets were merely utilitarian. The Horizontal Corrugated Roof Panel embraces contemporary design trends, presenting itself as a visually appealing option. With its tile effect metal roofing sheets, buildings can achieve a desirable aesthetic appeal that replicates the beauty of traditional tile roofs. Additionally, the product comes in a variety of colors, allowing for customization and personalization to suit individual preferences.Easy Installation and Cost-Effective Solution:Not only does the Horizontal Corrugated Roof Panel offer exceptional durability and aesthetics, but it also provides an easy and hassle-free installation process. With its wood support brackets, the panels can be quickly assembled, reducing labor costs and project timelines. This efficiency makes it an ideal option for both small-scale residential projects and large-scale commercial installations.Environmental Sustainability:In a time when sustainability is of paramount importance, the Horizontal Corrugated Roof Panel stands out for its environmentally conscious approach. Made with recyclable materials such as galvanized steel, this product is an eco-friendly alternative to traditional roofing options. Additionally, its ability to enhance energy efficiency contributes to reducing carbon emissions and overall environmental impact.Conclusion:The Horizontal Corrugated Roof Panel offered by (need to remove brand name) is revolutionizing roofing solutions with its durability, energy efficiency, aesthetic appeal, and sustainability. As the need for reliable and cost-effective roofing materials grows, this innovative product emerges as a game-changer in the industry. Whether for residential or commercial applications, this versatile and long-lasting roofing solution provides a viable alternative for those seeking excellence in both functionality and design.