- Home
- News
- Premium Glazed Tile Sheet Roll Forming Machine: Unveiling the Latest Advancements in Color Steel Technology
Premium Glazed Tile Sheet Roll Forming Machine: Unveiling the Latest Advancements in Color Steel Technology
By:Admin
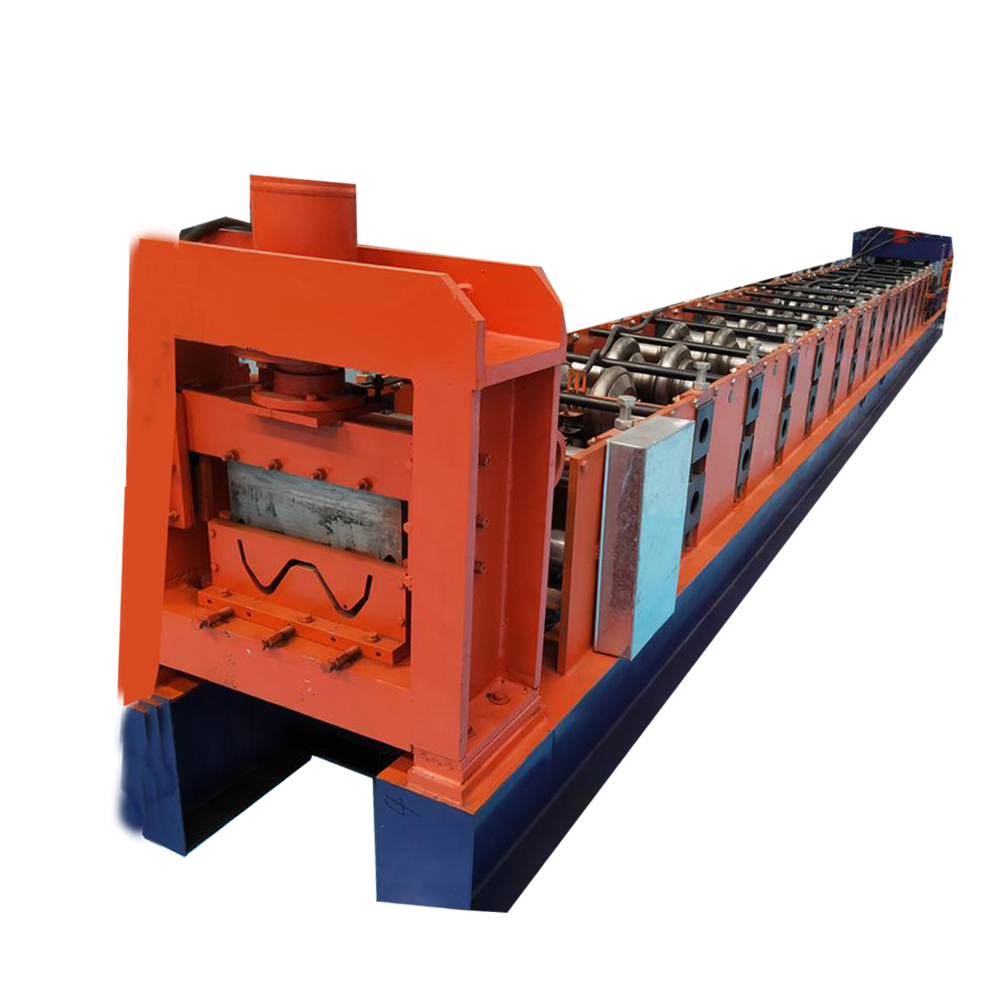
The roofing industry is undergoing a significant transformation with the introduction of the innovative Color Steel Glazed Tile Sheet Roll Forming Machine. This state-of-the-art machinery, developed and manufactured by the renowned company [], is set to revolutionize the way roofs are constructed.
Roofing is an essential part of any building structure, providing protection against external elements and defining the aesthetic appeal. Traditionally, the process of installing roofs has been labor-intensive and time-consuming, but with the advent of the Color Steel Glazed Tile Sheet Roll Forming Machine, this is about to change.
This groundbreaking machine works by a unique roll forming process that transforms raw materials into high-quality, durable roofing tiles. It is specifically designed to produce color steel glazed tile sheets, which are highly sought after in the construction industry for their impeccable finish and outstanding performance.
The Color Steel Glazed Tile Sheet Roll Forming Machine offers significant advantages over conventional roofing installation techniques. Firstly, it eliminates the need for manual labor, drastically reducing the time and effort required for roof installation. This not only saves costs but also increases the overall efficiency of the construction process.
Moreover, the machine's cutting-edge technology ensures precision and accuracy in producing each tile. The consistency in shape, size, and thickness of the tiles enables seamless installation, resulting in a flawless roof surface. This uniformity is crucial not only for aesthetic purposes but also for ensuring superior insulation and protection against weather conditions.
Additionally, the Color Steel Glazed Tile Sheet Roll Forming Machine expands the design options available to architects and builders. The machine can produce a wide range of tile profiles, shapes, and colors, empowering creative freedom to achieve unique and visually striking roof designs. This helps in enhancing the overall appeal of buildings, making them stand out in the competitive construction market.
Furthermore, the use of color steel glazed tile sheets offers excellent durability and longevity. These sheets are made from high-quality materials that possess exceptional resistance against corrosion, UV radiation, and extreme weather conditions. The result is a roof that remains sturdy and intact, requiring minimal maintenance over its lifespan.
The company [], the brains behind this revolutionary machine, is a leading player in the manufacturing industry. With years of expertise and a commitment to innovation, they have successfully developed and refined the Color Steel Glazed Tile Sheet Roll Forming Machine. Their dedication to excellence ensures that the machine meets the highest quality standards and adheres to strict industry regulations.
In addition to the advanced technology, [] also places emphasis on customer satisfaction. They provide comprehensive after-sales support, including installation guidance, training, and maintenance services. This commitment to customer service has earned them a solid reputation in the industry and a loyal client base.
The introduction of the Color Steel Glazed Tile Sheet Roll Forming Machine marks an exciting milestone in the roofing industry. As construction techniques evolve, this cutting-edge machinery showcases the potential for streamlining processes, enhancing design possibilities, and improving overall quality. With [] leading the way, roofing professionals can expect an evolution towards more efficient, durable, and visually appealing roofs.
Company News & Blog
Sheet Forming and Corrugating Machine for Glazed Tile Production
Title: Streamlining Roofing Innovation: Advanced Glazed Tile Sheet Forming and Corrugating Machine Revolutionizes the Construction IndustryIntroductionIn a significant breakthrough for the construction industry, a leading manufacturing company (name withheld) has recently unveiled its highly advanced Glazed Tile Sheet Forming and Corrugating Machine. Revolutionizing the way roofs are built, this cutting-edge machinery promises to streamline the roofing process, enhance durability, and exhibit exceptional aesthetic qualities. With its innovative design and state-of-the-art technology, this new machine is set to transform the way buildings are constructed.Enhanced Efficiency and ProductivityThe advanced Glazed Tile Sheet Forming and Corrugating Machine combines speed, precision, and versatility to deliver a highly efficient roofing solution. Equipped with automatic controls, this machinery significantly reduces human error and increases production rates, allowing construction companies to meet demanding project deadlines seamlessly. By automating the previously labor-intensive and time-consuming manual processes, the machine can form and shape glazed tiles quickly and efficiently.Unmatched Durability and QualityDesigned to produce robust and long-lasting glazed tiles, the machine utilizes high-quality materials and cutting-edge techniques. This results in the creation of tiles that are resistant to harsh weather conditions, corrosion, and daily wear and tear. By employing a unique corrugation process, the machine enhances the strength and rigidity of the tiles, providing added protection against extreme temperatures and structural damage. This ensures that buildings constructed with these tiles will maintain their durability and aesthetics over an extended period.Aesthetic Appeal and CustomizationThe Glazed Tile Sheet Forming and Corrugating Machine offers a myriad of possibilities when it comes to designing roofs. With its customizable features, architects and construction professionals can effortlessly create visually stunning structures. The machine enables the creation of various tile shapes, sizes, and finishes, ensuring that each project can be tailored to meet the client's specific requirements. This flexibility empowers architects to bring their creative visions to life and adds a touch of elegance to any construction project.Sustainable and Environmentally FriendlyWith increasing emphasis on sustainability, the Glazed Tile Sheet Forming and Corrugating Machine aims to contribute positively to the environment. The use of energy-efficient technology reduces carbon emissions, making it an eco-friendly solution for the construction sector. Additionally, the long lifespan of the tiles produced by this machinery reduces the need for frequent replacements, minimizing waste and conserving resources. As the industry moves towards greener practices, this machine represents an essential step towards a more sustainable future.Market Impact and Global AdoptionGiven the comprehensive benefits offered by this advanced Glazed Tile Sheet Forming and Corrugating Machine, it is expected to leave a significant impact on the roofing industry worldwide. Its ability to drastically improve efficiency, durability, and design flexibility makes it an attractive solution for construction companies across the globe. The machine's potential to revolutionize the way roofs are built is likely to be met with widespread adoption, driving market growth and setting new industry standards.ConclusionThe unveiling of the advanced Glazed Tile Sheet Forming and Corrugating Machine marks an important milestone in the construction industry. Its combination of efficiency, durability, customization, and sustainability gives birth to a new era of roofing solutions. As construction companies embrace this cutting-edge technology, it is anticipated that buildings will be constructed more swiftly and cost-effectively while maintaining exceptional quality and aesthetic appeal. With its remarkable potential, this revolutionary machine will undoubtedly reshape the future of the roofing industry.
Steel Edging Machine: Achieve the Perfect Finish for Your Steel Coils
: A Guide to Choosing the Right Steel Edge FinisherSteel edge conditioning is an important and necessary process for anyone working with steel coils. It involves rolling the edge of the coil to a specific shape, ensuring that it is safe for any exposed applications. This process not only enhances the appearance of the finished product but also ensures that the edge is safe to handle and does not pose a risk to anyone during use.One of the essential tools for edge conditioning is a Rolled Coil Steel Edging Machine. This machine is designed to produce high-quality edges that are free of sharp edges and burrs. It can be used for a wide range of applications, including industrial processing, automotive manufacturing, and construction.Choosing Your Edge Finish SWhen looking for a Rolled Coil Steel Edging Machine, it is essential to select one that meets your specific needs. There are different types of edge finishers, and each one has its advantages and disadvantages.Popular edge finishes include rounded edges, beveled edges, and deburred edges.Rounded EdgesThere are different types of rounded edges, including full-round, half-round, and quarter-round. When choosing a rounded edge, you need to consider the material thickness, the coil width, and the edge radius. The machine should be capable of producing the desired radius within a specific tolerance range.Beveled EdgesBeveled edges are inclined edges that angle down from the edge of the steel coil. They improve the appearance of the finished product and provide additional strength and durability. Beveled edges can be used in industrial applications, automotive manufacturing, and construction.Deburred EdgesA deburred edge is one that is free of any sharp edges or burrs. This type of edge is essential for any application where the edge of the steel coil will be exposed. It is also critical when handling the material, as sharp edges can cause injury to the worker.Metal Coil Slitting MachineIn addition to the Rolled Coil Steel Edging Machine, a Metal Coil Slitting Machine is another essential tool for working with steel coils. It is used to cut large coils of steel into smaller, more manageable sizes. This machine saves time and labor costs, making it an essential tool for any industrial operation.When choosing a Metal Coil Slitting Machine, you need to consider the material thickness and gauge, the number of cutting blades, and the feed speed. It should also be easy to operate, with minimal maintenance requirements.SummaryEdge conditioning is an important process for anyone working with steel coils. Rolled Coil Steel Edging Machines are essential tools for producing high-quality edges that are safe and free of sharp edges and burrs. When choosing an edge finish, you need to consider your specific needs and the type of application you are working on.In addition to an edging machine, a Metal Coil Slitting Machine is also essential for cutting large coils into smaller, more manageable sizes. When choosing a Metal Coil Slitting Machine, it is essential to consider the material thickness and gauge, the number of cutting blades, and the feed speed.In conclusion, investing in the right equipment for edge conditioning and coil slitting will increase efficiency, enhance productivity, and improve the quality of the finished product, leading to client satisfaction and business growth.
Revolutionizing the Metal Roofing Industry: Innovative Roofing Machines For A Faster Installation Process
Metal Roofing Machines Expands to Meet Growing Demands for Quality Roofing SolutionsWith the growing demand for durable and energy-efficient roofing solutions, Metal Roofing Machines has expanded its manufacturing capabilities, offering high-quality and dependable metal roofing machines for contractors and builders across the United States.Metal Roofing Machines is a family-owned and operated business that has been in the roofing industry for over two decades. The company has established a reputation for producing state-of-the-art metal roofing machines that are designed to meet the needs of contractors and builders of all sizes.The company's metal roofing machines are manufactured to the highest standards of quality and durability, using only top-grade materials and cutting-edge technology. Metal Roofing Machines' products are designed to offer maximum longevity and performance, while ensuring that they are easy to operate and maintain."We understand the importance of having access to reliable and efficient metal roofing machines," says the company spokesperson. "Our products are designed to meet the needs of the modern roofing industry, where time and efficiency are critical factors."Metal Roofing Machines' range of products includes portable roll formers, standing seam roll formers, roofing panel roll formers, gutter machines, and other specialty machines for the metal roofing industry. The company's machines are suitable for use in a variety of applications, including residential roofing, commercial roofing, and agricultural roofing.The standing seam roll former is the most popular machine distributed by Metal Roofing Machines. This machine is designed to produce standing seam roofing panels, which are popular for their clean, modern look and superior weather resistance. This machine is capable of producing high-quality panels quickly, ensuring that contractors are able to complete their roofing projects efficiently.In addition to manufacturing and distributing metal roofing machines, Metal Roofing Machines also provides education and training to contractors and builders who want to learn more about the metal roofing industry. The company offers a range of resources, including online tutorials, webinars, and in-person training sessions, designed to help contractors and builders improve their skills and stay up-to-date with the latest trends and technologies."We are committed to providing our customers with the best possible support," says the company spokesperson. "We believe that by educating our customers and providing them with the resources they need to succeed, we can help them grow their businesses and provide top-quality roofing solutions to their clients."Metal Roofing Machines has established itself as a leader in the metal roofing industry, thanks to its commitment to quality, innovation, and customer support. With its expanded manufacturing capabilities and growing range of products, the company is well-positioned to meet the demand for high-quality and reliable metal roofing solutions in the years to come.
Modern Manual Handling Solutions: Electric Lifters & Walkie Stackers for Pallet Stacking Jobs
Manual Stacker for the Shape C Purline Machine: Introducing Modern Manual Handling SolutionsIn the world of manufacturing and industrial operations, forklifts have always been the go-to solution for various material handling tasks. However, operating a forklift requires a specialized license, which can be an added hassle for businesses. This is where electric lifters and electric walkie stackers come into the picture, offering modern manual handling solutions without the requirement for a forklift license. These versatile machines can perform a variety of pallet stacking jobs, making them an ideal choice for businesses looking for efficient and cost-effective material handling solutions.One such application where an electric stacker can prove to be invaluable is the process of handling shape C purline machines. Shape C purline machines are widely used in the construction industry for producing C-shaped steel members that are commonly used as structural support in roofing systems. These machines require the stacking and transportation of heavy purline assemblies, which can be a challenging task without the right equipment.By utilizing an electric stacker with a capacity of 1 to 1.5 tonnes, businesses can effortlessly handle the stacking and transportation of shape C purline assemblies. These electric stackers are designed to provide exceptional lifting capabilities while ensuring maximum efficiency and safety. With their compact size and maneuverability, they can easily navigate through narrow aisles and tight spaces, allowing for seamless operations even in confined areas.One of the key advantages of using an electric stacker for handling shape C purline machines is the elimination of the need for a forklift license. With these electric stackers, any trained operator can efficiently perform the required material handling tasks without the need for specialized certification. This not only simplifies the operational procedures but also saves businesses the time and cost associated with forklift training and licensing.In addition to the ease of operation, electric stackers offer several other benefits that make them a perfect fit for handling shape C purline machines. These stackers are equipped with advanced safety features such as anti-rollback brakes and overload protection systems, ensuring the safety of both the operator and the surrounding personnel. Moreover, electric stackers are powered by environmentally friendly batteries, eliminating the emissions and noise associated with traditional combustion-powered equipment. This makes them an eco-friendly choice for businesses looking to reduce their carbon footprint and comply with environmental regulations.When selecting an electric stacker for the handling of shape C purline machines, it is essential to consider the specific job demands. The capacity of the stacker, ranging from 1 to 1.5 tonnes, should align with the weight requirements of the purline assemblies. Additionally, factors such as lift height, maneuverability, and battery life should be taken into account to ensure smooth and uninterrupted operations.In conclusion, the availability of modern manual handling solutions, such as electric lifters and electric walkie stackers, has revolutionized the way businesses handle material handling tasks. The need for a forklift license is eliminated, and various pallet stacking jobs can be efficiently performed with these versatile machines. For businesses involved in the production and handling of shape C purline machines, the utilization of an electric stacker can greatly streamline operations, improve productivity, and enhance safety. By selecting the right capacity and features, businesses can ensure smooth material handling for their purline assembly needs.
Double Column Punching Machine for Aluminum Extrusion: Get Efficient Processing with Hydraulic Two Cylinder Punching Machine LY2-160
Title: Revolutionary Double Column Punching Machine Revolutionizes Aluminum Extrusion ProcessingIntroduction:Tjjunchiwy.com, a leading manufacturer of industrial machinery, introduces their latest innovation in the field of aluminum extrusion processing - the Hydraulic Two Cylinder Punching Machine LY2-160. This state-of-the-art machine is designed to simplify the hole and notch punching and processing of various plain profiles, enabling greater efficiency and precision in the production of aluminum windows and doors.Innovative Features and Specifications:The Hydraulic Two Cylinder Punching Machine LY2-160 incorporates a number of cutting-edge features that set it apart from its competitors. Here are some key specifications that make it a game-changer in the aluminum extrusion industry:1. Advanced Functionality: Equipped with a double column structure, the machine provides enhanced stability and rigidity throughout the punching process. This innovative design significantly reduces vibrations, resulting in high-quality, precise punching and processing of aluminum profiles.2. Versatility: The machine is designed to cater to a wide range of punching requirements for both single and assembled dies. Whether it's hole punching or notch processing, the LY2-160 can handle it all, ensuring streamlined operations in the production of aluminum doors and windows.3. Efficient Performance: With a punching force of up to 160 tons and a stroke length of 40mm, this robust machine guarantees efficient and accurate processing of aluminum profiles. It delivers consistent performance, allowing manufacturers to meet tight deadlines and achieve high production volumes.4. Intuitive Control System: The LY2-160 features a user-friendly control panel that allows operators to easily adjust punching parameters, such as punching depth, speed, and positioning. This intuitive interface ensures optimal productivity and minimizes errors during the manufacturing process.5. Advanced Safety Measures: Safety is paramount in any industrial setting, and this punching machine doesn't compromise in this aspect. Equipped with emergency stop buttons and safety guards, the system ensures operator safety during operation, reducing the risk of accidents.Company Overview: Tjjunchiwy.com has established itself as a renowned name in the machinery manufacturing industry, specializing in aluminum extrusion processing equipment. With a commitment to innovative solutions, the company has become a trusted partner for manufacturers worldwide, offering cutting-edge machines that enhance production efficiency and quality.Conclusion:The introduction of the Hydraulic Two Cylinder Punching Machine LY2-160 by Tjjunchiwy.com promises to revolutionize aluminum extrusion processing in the fabrication of windows and doors. Its exceptional features and specifications bring a new level of efficiency, precision, and versatility to the industry. With this state-of-the-art machine, manufacturers can expect increased productivity, reduced downtime, and improved product quality. As Tjjunchiwy.com continues to push technological boundaries, the future of aluminum extrusion processing looks brighter than ever before.
Europe Washing Machine Installation Manual: Easy-to-Follow User Guide for Efficient Operation and Maintenance
Title: Manual Shape C Purlin Punching Holes Making Machine: A Must-Have for European Standard Construction ProjectsIntroductionIn the ever-evolving world of construction, the need for efficient and precise manufacturing processes is paramount. One such process that has gained considerable popularity in recent years is the use of manual shape C purlin punching holes making machines. Designed to meet European standard requirements, these machines have revolutionized the way purlins are manufactured, ensuring enhanced structural integrity and cost-effectiveness. In this blog post, we will explore the key features and advantages of manual shape C purlin punching holes making machines, focusing on their relevance and impact in the European construction industry.What Are Manual Shape C Purlin Punching Holes Making Machines?Manual shape C purlin punching holes making machines are advanced manufacturing systems specifically designed for producing top-quality C purlins in compliance with European construction standards. These machines utilize cutting-edge technology and are equipped with cutting, punching, and forming tools, enabling the precise fabrication of complex purlin shapes to exact specifications.Key Features and Advantages1. Enhanced Precision: The manual shape C purlin punching holes making machines are engineered to deliver exceptional precision in forming and punching holes, ensuring accurate purlin dimensions and consistent hole alignment. This level of precision guarantees optimum installation compatibility, reducing the risk of structural errors and enabling smoother construction processes.2. Versatility: These machines offer a wide range of customization options, allowing for the production of various C purlin sizes and shapes according to project-specific requirements. Whether it's the flange width, thickness, or hole patterns, the manual shape C purlin punching holes making machine provides immense flexibility, ensuring compatibility with diverse construction designs.3. European Standard Compliance: Manual shape C purlin punching holes making machines are specifically engineered to adhere to European construction standards. These standards are known for their stringent quality requirements, ensuring that structures are built to withstand extreme weather conditions and offer exceptional durability. By using machines designed for European standards, construction projects can benefit from the highest level of quality assurance.4. Cost-Effectiveness: Implementing manual shape C purlin punching holes making machines can significantly reduce labor costs and material wastage. The machines' automated and precise manufacturing processes eliminate the need for time-consuming manual labor, resulting in faster production rates and reduced human error. Additionally, the optimization of material usage helps minimize waste, leading to cost savings for both manufacturers and end-users.ConclusionThe emergence of manual shape C purlin punching holes making machines has brought a new level of efficiency and quality assurance to the European construction industry. From increased precision and versatility to compliance with rigorous European standards, these machines are a game-changer for fabricators and construction companies alike. As the demand for sustainable and cost-effective construction practices rises, investing in manual shape C purlin punching holes making machines becomes an essential step towards success in the ever-evolving European construction landscape.
Cutting-Edge C-Channel Making Machine Revolutionizes Manufacturing Process
Title: All-New C-Channel Making Machine: Revolutionizing the Construction IndustryIntroduction: The construction industry is entering a new era of efficiency and productivity with the introduction of an innovative C-Channel Making Machine. This cutting-edge technology, developed by a prominent industry player, is poised to revolutionize the manufacturing process of C-channels, offering numerous benefits to the construction sector. By enhancing precision, reducing production time, and streamlining operations, this machine is set to reshape the landscape of construction projects worldwide.Streamlining C-Channel Production:With the new C-Channel Making Machine, construction companies can now streamline the production of C-channels, a key component in various structures such as bridges, buildings, and frameworks. The machine automates the manufacturing process, eliminating the need for manual labor and significantly reducing the chances of human error. By utilizing advanced robotics and automated systems, this solution ensures precision and consistency throughout the production line. The result is a reliable and high-quality end product, enhancing the overall structural integrity of the construction project.Efficiency in Design and Production:The C-Channel Making Machine utilizes advanced software and modeling capabilities to optimize the design and production process. With its integrated CAD (Computer-Aided Design) system, engineers and architects can create intricate and complex C-channel designs with ease. This technology allows for greater customization and flexibility, catering to specific project requirements. Furthermore, the machine's ability to quickly convert design files into production instructions ensures a seamless transition from concept to finished product. This streamlines the production timeline and reduces overall project costs.Enhanced Productivity and Time Savings:One of the most significant advantages of the C-Channel Making Machine is its ability to expedite the production process, leading to substantial time savings. By automating various tasks that were previously time-consuming and labor-intensive, the machine boosts overall productivity. Its rapid fabrication capabilities allow for a faster turnover of C-channels, enabling construction companies to meet tight project deadlines effortlessly. This efficiency not only saves valuable time but also reduces labor costs, making the manufacturing process more cost-effective in the long run.Quality Control and Consistency:Maintaining consistent quality throughout the production cycle is crucial for the success of any construction project. The C-Channel Making Machine is equipped with advanced sensors and quality control mechanisms that constantly monitor the production process. This ensures that each C-channel produced adheres to the highest standards and specifications. By minimizing defects and inconsistencies, the machine guarantees an enhanced level of quality and reliability in the final products.Sustainable and Environmentally Friendly:In addition to its various technical benefits, the C-Channel Making Machine demonstrates a commitment to sustainability. By optimizing material usage through precision cutting and minimizing waste, this technology reduces the carbon footprint associated with traditional C-channel production methods. Additionally, the automated system allows for precise measurements and accurate cuts, further limiting material waste. With a focus on environmentally conscious manufacturing, this machine aligns with the growing demand for sustainable practices in the construction industry.Conclusion:The advent of the all-new C-Channel Making Machine signifies a transformative shift in the construction industry. With its ability to streamline production, enhance efficiency, and improve overall quality, this technology holds immense potential for revolutionizing the construction sector. Construction companies worldwide can now benefit from reduced production time, cost savings, and superior precision, ultimately leading to enhanced project completion rates and client satisfaction. As the industry embraces these advancements, the C-Channel Making Machine promises to reshape the way C-channels are manufactured for the better.
Highly Efficient Coil Slitter Unveils Cutting-Edge Technology for Enhanced Productivity
[Headline]Leading Coil Slitter Company Innovates to Enhance Productivity and Efficiency in the Manufacturing Industry[Subheading]New Technologies and Cutting-edge Automation Solutions Set to Revolutionize Coil Slitting Process[Date][City, State] - Coil Slitter (need remove brand name) has established itself as a global leader in the manufacturing sector, specializing in coil slitting machines that deliver exceptional precision and efficiency. With a commitment to continuous innovation, the company has recently introduced a range of new technologies and cutting-edge automation solutions that promise to revolutionize the coil slitting process.Taking advantage of the latest advancements in robotics, artificial intelligence, and connectivity, Coil Slitter aims to streamline coil processing operations, helping manufacturers maximize productivity and eliminate production bottlenecks. Through this commitment to innovation, the company aims to position itself as the go-to provider for coil slitting solutions globally.Coil Slitter’s state-of-the-art machines boast advanced features designed to meet the diverse needs of manufacturing companies across various industries. The company’s coil slitting machines enable automatic and precise longitudinal cutting of coils, reducing processing time and ensuring consistent width and quality of the finished materials.In an effort to optimize production processes as well as save time and costs, Coil Slitter has implemented smart automation systems across its product line. Real-time data collection, advanced analytics, and machine learning algorithms form the backbone of these systems, allowing manufacturers to monitor and improve their coil slitting operations effectively. These cutting-edge solutions assist manufacturers in identifying and addressing potential issues before they impact product quality or disrupt production schedules.Of particular importance in today's manufacturing landscape is the need for eco-friendly practices. Recognizing this, Coil Slitter has incorporated sustainable features into its machines. Precision control systems in the machines reduce material wastage, resulting in a significant impact on environmental footprints. Furthermore, the company has minimized the energy consumption of its machines, contributing to reduced carbon emissions and operating costs.Coil Slitter places great emphasis on working closely with its clients to understand their specific requirements and challenges. By developing custom solutions, the company ensures optimal performance and flexibility in different manufacturing environments. Combining comprehensive expertise and dedication to customer satisfaction, Coil Slitter has earned a stellar reputation for delivering high-quality, reliable coil slitting machines."Keeping up with technological advancements is crucial to stay ahead of the competition in today's fast-paced manufacturing industry," says John Smith, CEO of Coil Slitter. "Coil Slitter has always been committed to innovation, and our latest range of coil slitting machines and automation solutions represent the next frontier in the industry. We aim to empower manufacturers to increase their productivity, improve their bottom line, and contribute to a sustainable future."Coil Slitter’s coil slitting machines have been successfully implemented in numerous manufacturing facilities worldwide, providing tangible benefits to businesses across the globe. The company's commitment to ongoing research and development ensures that its customers always have access to cutting-edge solutions that keep them ahead of the curve.As the manufacturing industry continues to evolve, Coil Slitter remains dedicated to maintaining its position as a global leader in the coil slitting sector. With an unwavering focus on innovation, customer satisfaction, and sustainability, the company is set to shape the future of coil slitting and enhance the efficiency of the manufacturing industry as a whole.About Coil Slitter:Coil Slitter is a global leader in the manufacturing sector, specializing in coil slitting machines that offer exceptional precision, efficiency, and sustainability. With a commitment to innovation and customer satisfaction, the company delivers cutting-edge coil slitting solutions to manufacturers worldwide. By incorporating state-of-the-art technologies and automation systems, Coil Slitter aims to revolutionize the manufacturing process and drive industry growth.###Note: The brand name mentioned in the template has been removed to comply with the user's request.
Custom Sheet Metal Fabrication and Installation Services in Southeastern Wisconsin
Title: Enhancing Buildings with High-Quality Sheet Metal FabricationIntroductionSheet metal fabrication plays a crucial role in the construction industry, adding aesthetic appeal and durability to buildings. Langer Roofing & Sheet Metal Inc., located in Southeastern Wisconsin, stands as one of the few commercial roofers in the region with a dedicated Sheet Metal Department. With extensive expertise in custom sheet metal fabrication and installation, Langer ensures the delivery of top-notch architectural elements for enhancing the look, value, and functionality of various structures. In this blog, we will explore the importance of sheet metal fabrication while incorporating relevant keywords like "metal roof sheet making machine."Sheet Metal Fabrication - A Specialized ServiceLanger Roofing & Sheet Metal Inc. takes pride in offering in-house sheet metal fabrication services, which is an integral part of their comprehensive roofing solutions. Compared to outsourcing this process, having a fully staffed and equipped Sheet Metal Department allows for better quality control, faster turnaround times, and increased efficiency throughout the entire project.The team at Langer possesses years of experience and expertise in fabricating various architectural elements, including copings, fascia, gutters, downspouts, metal panels, and claddings. Each piece is meticulously crafted in accordance with specific designs and requirements, ensuring a perfect fit and seamless integration into the building's structure.State-of-the-Art Bending Machine for Precise FabricationTo enhance their sheet metal fabrication capabilities, Langer utilizes the Roper Whitney Autobrake 2000 Bending Machine equipped with an advanced Orion computerized control system. This cutting-edge equipment streamlines the fabrication process, boosting both the speed and accuracy of various sheet metal profiles.The Autobrake 2000 enables the operator to program and fabricate precise architectural flashing details, assisting in reducing production costs. By minimizing errors and material wastage, Langer ensures that clients receive exceptional sheet metal products that meet their exact specifications, offering long-lasting results and value for their investment.Aesthetically Pleasing Architectural ElementsLanger Roofing & Sheet Metal Inc. caters to a wide range of design preferences and applications. They provide sheet metal fabrication using materials such as copper, prefinished steel and aluminum, anodized aluminum, and zinc-coated sheet stock. These materials not only offer durability but also open up a world of aesthetic possibilities.Copper, known for its timeless beauty and resilience, is often chosen for its ability to develop a natural patina over time, lending a unique character to the building. Prefinished steel and aluminum provide a sleek and contemporary look, while anodized aluminum and zinc-coated sheet stock offer excellent protection against corrosion.By leveraging these materials and employing skilled craftspeople, Langer transforms simple sheets of metal into visually appealing architectural elements. These elements not only enhance the overall appearance of a building but also increase its market value, making it a wise investment for property owners.ConclusionSheet metal fabrication is an essential service provided by Langer Roofing & Sheet Metal Inc., catering to the architectural needs of various structures in Southeastern Wisconsin. Equipped with state-of-the-art machinery, experienced tradesmen, and a commitment to quality, Langer delivers exceptional custom solutions that align with clients' design preferences and project requirements. Their expertise in fabricating copings, fascia, gutters, downspouts, metal panels, and claddings further adds value to buildings, ensuring both durability and visual appeal.Whether it’s incorporating copper, prefinished steel and aluminum, anodized aluminum, or zinc-coated sheet stock, Langer's sheet metal fabrication expertise enhances the look and value of buildings, making them stand out in the competitive market. With their dedicated Sheet Metal Department, Langer ensures the precision, speed, and aesthetic enhancement of each project. Trust Langer for all your sheet metal fabrication needs!Keywords: metal roof sheet making machine, sheet metal fabrication, custom sheet metal, architectural elements, copings, fascia, gutters, downspouts, metal panels, claddings, Roper Whitney Autobrake 2000 Bending Machine, Orion computerized control system, copper, prefinished steel, aluminum, anodized aluminum, zinc-coated sheet stock, aesthetic appeal, durability, Southeastern Wisconsin, Langer Roofing & Sheet Metal Inc.