- Home
- Blog
- Efficient and Time-saving Automatic Roll Slitter Revolutionizes Industrial Cutting Process
Efficient and Time-saving Automatic Roll Slitter Revolutionizes Industrial Cutting Process
By:Admin
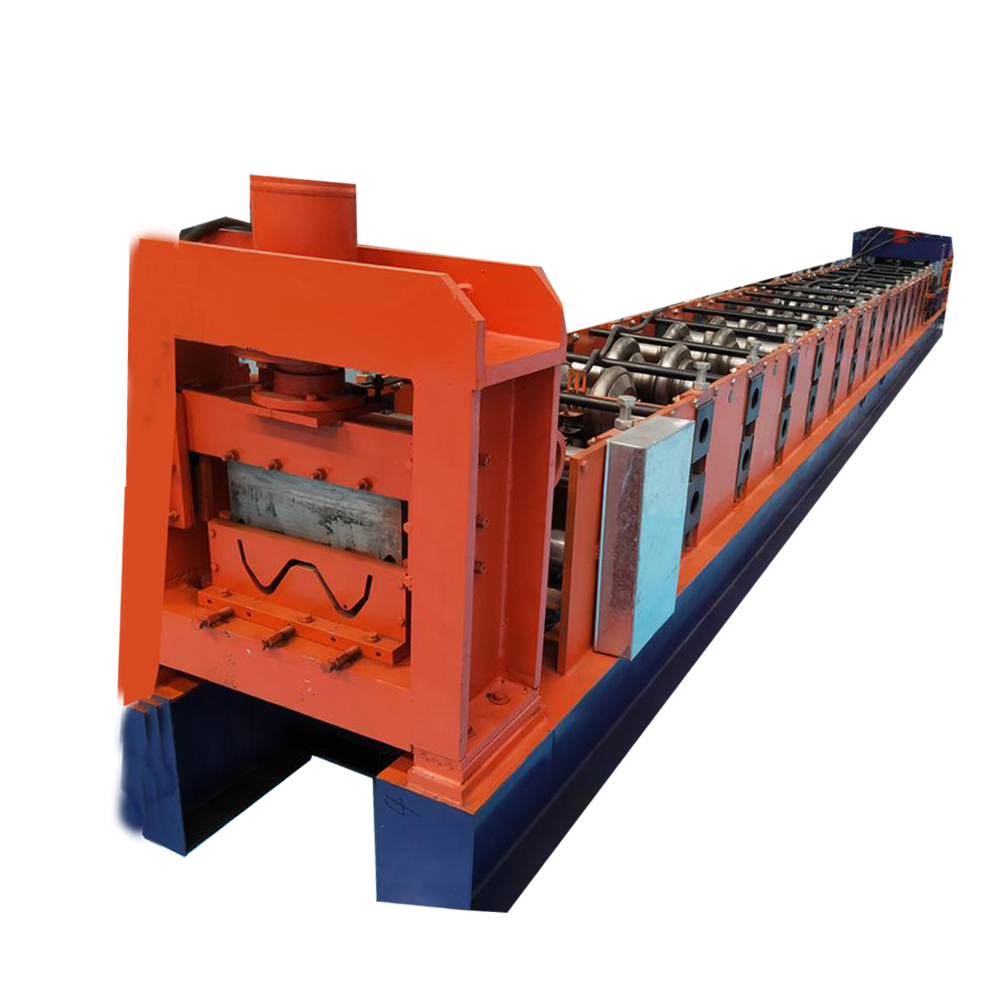
The Automatic Roll Slitter is a state-of-the-art machine that utilizes high-speed rotary knives to slit rolls of materials into precise widths. With its user-friendly interface, users can easily adjust the cutting speed, knife angle, and feed rate to meet their specific needs. The machine is designed for high-volume production, and can handle a variety of roll widths, weights, and types of materials, including non-woven fabrics, foam, and vinyl, among others.
Despite its advanced technology and automated features, the Automatic Roll Slitter is designed to be safe and reliable, with a sturdy frame and safety shields to prevent accidents. It also comes with a range of accessories, such as laser sensors, edge guides, and static eliminators, to further enhance its precision and efficiency.
According to the company's President, the Automatic Roll Slitter has been a game-changer in the industrial equipment market. "We are proud to offer this cutting-edge product that has revolutionized the way companies handle rolls of materials. The Automatic Roll Slitter is not only faster and more accurate than manual methods, but it also saves time, reduces waste, and lowers production costs."
The company's mission is to provide its clients with the highest quality equipment and solutions, backed by excellent customer service and technical support. Its team of experts works closely with clients to understand their unique requirements and help them find the best solutions to optimize their operations.
Recently, the Automatic Roll Slitter was used by a leading producer of medical garments to increase their production capacity and improve product quality. The company had been struggling with the limitations of their manual slitting process, which was prone to errors and inconsistencies. After implementing the Automatic Roll Slitter, they were able to achieve a higher yield of usable materials, reduce scrap and rework, and improve their overall output.
The Automatic Roll Slitter has also been adopted by companies in various industries, such as packaging, automotive, and electronics, among others. Its versatility and adaptability make it an ideal choice for processing a wide range of materials, from foam tapes to flexible circuits.
In addition to its superior performance, the Automatic Roll Slitter is also environmentally friendly, with features such as energy-efficient motors and reduced waste. Its precision cutting also results in less material waste, which contributes to a more sustainable manufacturing process.
As the demand for automation and efficient production methods continues to grow, the Automatic Roll Slitter remains a top choice for companies looking to improve their operations and stay ahead of the competition. With its advanced technology, reliability, and excellent customer support, it is no wonder why it has become a preferred choice for many industries worldwide.
Company News & Blog
Ultimate Guide 2020: Roll Forming Process from Concept to Production
Title: Mastering the Roll Forming Process: A Comprehensive Guide to Horizontal Profiled Panel Roll FormingIntroduction: In the modern world of manufacturing, roll forming has emerged as a highly efficient and cost-effective method for shaping flat metal sheets into complex profiles. Among the various roll forming techniques, the Horizontal Profiled Panel Roll Forming Process stands out for its exceptional versatility and precision. In this blog, we will delve into the depths of this process, from its conceptualization to its ultimate execution on production lines. Join us on this ultimate guide for a detailed understanding.1. Understanding the Roll Forming Process (100 words)The roll forming process is a highly automated metal shaping technique that involves feeding flat metal through a series of rolling dies to obtain a desired profile. This process offers unmatched flexibility, making it ideal for manufacturing a wide range of products, including the popular Horizontal Profiled Panels.2. Key Components and Their Functions (200 words)a. Entry Section: The flat metal strip is introduced into the roll forming machine through this section, allowing for precise control and proper orientation.b. Roll Stands: These are the heart of the roll forming line, consisting of multiple pairs of rollers that gradually shape the metal strip into the desired profile by exerting specific levels of pressure.c. Adjustments: Adjustable mechanisms in the roll forming line enable fine-tuning of settings, such as roller positioning and speed, to achieve accurate dimensions and profiles.d. Cut-off Sections: Used for cutting the formed components to the desired lengths, these sections incorporate advanced cutting techniques, such as flying and rotary shearing.3. Unleashing the Potential: Concept to Production (300 words)a. Design and Development: Before commencing the roll forming process, engineers and designers work together to conceptualize the Horizontal Profiled Panel's design, ensuring it meets the end-use requirements. Computer-aided design (CAD) software plays a crucial role in this phase.b. Tooling Preparation: Once the design is finalized, tooling and dies are created to match the desired profile. Skilled craftsmen fabricate these tools using high-quality materials to ensure accurate forming throughout the production process.c. Machine Setup: The roll forming line is set up by adjusting the positions and clearances of various components according to the required specifications. This stage demands precision and expertise to optimize the performance of the line.d. Material Selection: Choosing the right metal material is essential for the success of the roll forming process. Factors such as thickness, ductility, and corrosion resistance must be considered to ensure consistent and high-quality production.e. Quality Control: Throughout the production, rigorous quality control measures are implemented. Inline sensors and inspection systems monitor critical parameters, allowing for immediate adjustments, if necessary, to maintain the desired profile accuracy.f. Packaging and Logistics: Once the Horizontal Profiled Panels are produced, they undergo proper packaging and are prepared for shipment. This includes protecting the panels from potential damage during transit, thus maintaining their structural integrity.g. Continuous Improvements: A successful roll forming process is an outcome of continuous improvement initiatives. Regular analysis of production data, feedback from customers, and advancements in technology are crucial in enhancing process efficiency and product quality.Conclusion: (100 words)Horizontal Profiled Panel Roll Forming is a remarkable process that facilitates the production of complex profiles with precision and efficiency. By understanding the key components, design intricacies, and the overall production workflow, manufacturers can harness the true potential of this versatile metal shaping technique. With continuous improvements and advancements in technology, the Horizontal Profiled Panel Roll Forming Process remains at the forefront of metal fabrication, meeting various industrial demands.
State-of-the-Art Roll Forming Machine for High-Quality Roof Panels
[News Introduction]Roof Panel Roll Forming Machines Revolutionize Construction Industry[Location], [Date] - The roofing industry has witnessed a revolutionary breakthrough with the introduction of the advanced Roof Panel Roll Forming Machine. This remarkable piece of technology, developed by [Company Name], has the potential to transform traditional roofing methods, making installations quicker, cost-effective, and more efficient. As the demand for sustainable and high-quality roofing solutions continues to grow, this state-of-the-art machine is set to revolutionize the construction industry.[Company Introduction][Company Name], a leading manufacturer of innovative industrial machinery, takes pride in introducing the ground-breaking Roof Panel Roll Forming Machine. Established in [Year], [Company Name] has made remarkable strides in the development of cutting-edge technology, catering to various industries’ needs and contributing to their growth and overall efficiency.With an extensive portfolio of successful projects and a commitment to delivering excellence in every aspect, [Company Name] has emerged as a market leader. Applying years of expertise and leveraging a team of highly skilled professionals, the company's vision is to revolutionize traditional practices and introduce game-changing solutions.[Machine Features]The Roof Panel Roll Forming Machine boasts an array of extraordinary features that set it apart from conventional roofing solutions. Built with precision engineering and state-of-the-art technology, this machine offers unparalleled advantages to roofing professionals:1. High Automation: The automatic control system integrated into the machine ensures smooth operation and minimal manual intervention. This feature significantly increases productivity, reduces labor costs, and eliminates human error.2. Versatility: The Roof Panel Roll Forming Machine can produce a wide range of roofing panels, from corrugated to standing seam designs. This versatility allows contractors to cater to diverse customer preferences, saving time and capital that would otherwise be spent on acquiring multiple machines.3. Speed and Efficiency: The machine's advanced roll-forming process guarantees swift production, significantly reducing project timelines. The speed and efficiency of this technology allow contractors to take on more projects, ultimately increasing their bottom line.4. Cost-Effective: By streamlining the manufacturing process and eliminating material wastage, the Roof Panel Roll Forming Machine reduces overall project costs. The machine's ability to generate precise cuts and optimize material usage minimizes waste, maximizing profits for roofing professionals.5. Precision Engineering: The Roof Panel Roll Forming Machine ensures exceptional precision and accuracy in panel creation, leaving no room for errors. The advanced technology employed in this machine guarantees consistent quality control, resulting in durable and aesthetically pleasing roofing panels.6. Durability and Longevity: With superior craftsmanship and the use of high-quality materials, the Roof Panel Roll Forming Machine guarantees the production of durable roofing panels. Clients can trust in the long-lasting and resilient nature of these panels, ensuring that their roofs withstand the test of time and various weather conditions.[Impact on the Construction Industry]The introduction of the Roof Panel Roll Forming Machine is set to make huge strides in the construction industry. Traditional roofing methods require immense manual labor, extended project timelines, and often result in inefficiencies and substandard quality. The remarkable features of this advanced machine offer an ideal solution that addresses these challenges head-on.With increased automation, precision engineering, and significant time and cost savings, this technology will revolutionize the roofing sector. Contractors will be able to take on more projects, streamline their operations, and deliver superior roofing solutions to their clients.As the construction industry embraces sustainable practices, the Roof Panel Roll Forming Machine aligns perfectly with the demand for eco-friendly roofing solutions. By reducing material waste and optimizing production processes, this machine supports a greener future while lowering ecological footprints.[Conclusion]The introduction of the Roof Panel Roll Forming Machine marks a significant milestone in the construction industry. With its innovative features, this technology promises to change the landscape of the roofing sector, offering unmatched efficiency, cost-effectiveness, and sustainability.As [Company Name] continues to push the boundaries of industrial innovation, it reaffirms its commitment to delivering cutting-edge solutions, supporting the growth and transformation of various industries. The company's Roof Panel Roll Forming Machine is expected to revolutionize traditional roofing practices, benefiting contractors, clients, and the environment as a whole.
Cold Rolling Forming Machines for Automated Production of Various Roofing Sheets
and IBR sheet making machine.Roof Sheet Making Machines - An OverviewRoof sheet making machines are modern-day machines that utilize the cold roll forming principle to produce roofing sheets in bulk. These machines are also known as IBR sheet making machines or color steel roll forming machines. They are fully automatic and designed to produce sheets in a variety of designs and dimensions. They are robust, reliable, and highly efficient, capable of producing high-quality roofing sheets that can be used for AD boards, wall panels, and other applications.The Working Principle of Roof Sheet Making MachinesRoof sheet making machines use a series of rollers to form different shapes and designs on flat metal sheets. The process begins when the metal sheet passes through the first set of rollers, which bend it into a curve. The sheet then moves through several sets of rollers, each producing a different shape and size until the final product is produced. The rollers on these machines are designed to be adjustable, allowing operators to create different designs, dimensions, and shapes.Advantages of Roof Sheet Making MachinesRoof sheet making machines offer several benefits, including:1. High efficiency - Roof sheet making machines are fully automatic and can produce large quantities of roofing sheets in a short period. This makes them ideal for mass production.2. Customization - With the adjustable rollers, roof sheet making machines make it possible to create unique designs and shapes that meet specific customer requirements.3. Low maintenance - These machines are designed to be low maintenance, reducing the overall cost of operation.4. High-quality output - Roof sheet making machines produce high-quality roofing sheets that are durable, robust, and weather-resistant.Applications of Roof Sheet Making MachinesRoof sheet making machines find broad applications in the construction industry, particularly in roofing. The roofing sheets produced by these machines are used for:1. Residential roofing - The roofing sheets are used to create attractive, durable, and weather-resistant roofs for homes.2. Commercial roofing - Roof sheet making machines produce roofing sheets that are ideal for commercial buildings such as warehouses, factories, and workshops.3. Agricultural roofing - The roofing sheets are ideal for agricultural use since they are weather-resistant, durable, and low maintenance.ConclusionRoof sheet making machines are versatile, efficient, and affordable pieces of equipment that make the production of high-quality roofing sheets possible. They offer several benefits over other manufacturing methods, including low maintenance, high output, and customization options. With ongoing technological advancements, the market for roof sheet making machines is expected to grow, driving innovation and leading to even greater efficiency and customization options.
Installing Shallow Pitch Standing Seam Metal Roof on Tar and Gravel Roof
Looking to replace an old tar and gravel roof in your home? Perhaps it's time to consider the benefits of a standing seam metal roof instead! A shallow pitch standing seam metal roof can offer numerous advantages over traditional roofing materials, making it a popular choice for homeowners looking to upgrade their roofs.One of the main benefits of a standing seam metal roof is its durability. Metal roofs are known for their longevity and can last up to 70 years with proper maintenance. This means you won't have to replace your roof as often, saving you money on future repairs and replacements.Additionally, metal roofs are highly resistant to weather-related damage. They can withstand harsh winds, heavy rainfall, and even hail storms. This makes them ideal for homes in areas prone to extreme weather conditions.But that's not all! Metal roofs can also help improve the energy efficiency of your home. They reflect solar radiation, preventing your home from absorbing excess heat and reducing your cooling costs during hot summer months. They can also be designed to optimize natural ventilation, further reducing your energy consumption.If you're worried about the aesthetic appeal of a metal roof, don't be! Standing seam metal roofs come in a variety of colors and finishes, allowing you to choose a design that complements your home's architectural style.Best of all, installing a standing seam metal roof is quick and easy thanks to metal roof panel machines. These machines can fabricate custom panels on-site, ensuring a perfect fit for your roof. They can also help reduce waste and save time during installation.In conclusion, a shallow pitch standing seam metal roof can be a great investment for homeowners looking to replace their old roofs. With its durability, weather resistance, energy efficiency, and aesthetic appeal, a metal roof can offer numerous benefits for years to come. So, consider a metal roof for your home and take advantage of the convenience and durability it offers!
China's Leading Manufacturer Offers Comprehensive Roll Forming Solutions for Various Applications
Roofing Sheet Forming Machine: The Ultimate Solution for Precise and Efficient RoofingWhen it comes to roofing materials, choosing the right one is crucial to ensure the durability and aesthetics of a building. Among the various options available, roofing sheets have become increasingly popular due to their versatility and cost-effectiveness. However, to efficiently produce roofing sheets that meet specific requirements, a reliable and precise manufacturing process is essential. That's where a Roofing Sheet Forming Machine comes into play.A roofing sheet forming machine is an advanced piece of equipment designed specifically for the production of roofing sheets. It is widely used across various industries, including construction, architecture, and manufacturing. The machine utilizes the process of roll forming, which is known for its accuracy and efficiency in creating uniform and high-quality products.The roll forming process involves passing a sheet of metal through a series of rollers, gradually shaping it into the desired profile. With the use of custom-made molds, the machine can produce different types of roofing sheets, such as corrugated, trapezoidal, and standing seam profiles. This flexibility allows manufacturers to cater to a wide range of customer demands and project specifications.One of the significant advantages of using a Roofing Sheet Forming Machine is its ability to ensure precision and consistency throughout the production process. Each roller in the machine is uniquely designed to shape the metal sheet with precise measurements and dimensions. This results in roofing sheets that fit perfectly and are aesthetically pleasing.Additionally, the machine's high-speed operation enables manufacturers to produce a large volume of roofing sheets quickly. This not only saves time but also enhances productivity, making it an ideal choice for mass production. Furthermore, the machine's automated control system eliminates the need for manual labor, reducing the chances of errors and ensuring a safer working environment.Quality is of utmost importance when it comes to roofing materials, and a Roofing Sheet Forming Machine excels in delivering consistent and durable products. By using high-quality materials and advanced manufacturing techniques, these machines guarantee the production of roofing sheets that are resistant to corrosion, weathering, and wear. This durability ensures that the roofs constructed using these sheets can withstand harsh environmental conditions and provide long-lasting protection.In addition to its primary function of manufacturing roofing sheets, a Roofing Sheet Forming Machine offers several other benefits. It provides versatility by offering customizability options, allowing manufacturers to produce roofing profiles of different lengths, widths, and thicknesses. This ensures that they can cater to diverse customer requirements and project specifications.Moreover, the machine's operation is accompanied by minimal noise and vibration, thanks to its advanced engineering and quality construction. This reduces disturbances in the workplace and contributes to a peaceful working environment for employees. Additionally, the machine requires minimal maintenance, leading to lower operational costs and improved overall efficiency.As the demand for roofing sheets continues to rise, it is essential to choose a reliable and experienced manufacturer when investing in a Roofing Sheet Forming Machine. A reputable manufacturer will not only provide top-quality machines but also offer comprehensive support and service throughout the purchase process. They will assist in the selection of the right machine, provide installation and training, and offer after-sales support to ensure smooth and efficient operations.In conclusion, a Roofing Sheet Forming Machine is the ultimate solution for producing precise, durable, and cost-effective roofing sheets. Its ability to deliver consistent quality, high-speed production, and customizability makes it an indispensable piece of equipment in the roofing industry. So, whether you are a contractor, builder, or manufacturer, investing in a Roofing Sheet Forming Machine is a wise choice to elevate your roofing business to new heights.
Aluminium Profile Bending and Window Curving Services: Mumbai's Metfab Machines Delivers Expert Solutions
Title: Unlocking Ultimate Precision: Aluminium Extrusion Bending MachineIntroduction:In the world of manufacturing, precision and efficiency are key factors contributing to a successful production process. When it comes to shaping aluminium profiles and sections for various industries, the importance of a reliable bending machine cannot be overstated. Metfab Machines Mumbai, a leading provider of fabrication machinery, offers an exceptional solution - the Aluminium Extrusion Bending Machine. In this blog, we will explore the incredible capabilities of this machine and how it revolutionizes the bending process in the aluminium industry.Section 1: Understanding Aluminium Extrusion BendingAluminium extrusion bending refers to the process of bending aluminium profiles and sections to achieve specific shapes and curves. This bending technique has gained immense popularity due to its versatility and the advantages it offers in terms of aesthetics and functionality.Section 2: The Powerhouse: The Aluminium Extrusion Bending MachineMetfab Machines Mumbai stands out as a provider of high-quality bending machines, specifically designed to handle aluminium extrusion. Their precision-engineered Aluminium Extrusion Bending Machine offers exceptional capabilities, making it an indispensable tool in the aluminium fabrication industry.The machine boasts state-of-the-art features such as:1. Advanced Bending Technology: Metfab Machines Mumbai incorporates cutting-edge bending technology in their Aluminium Extrusion Bending Machine, ensuring precision, accuracy, and consistency in every bend.2. Versatile Bending Capabilities: This machine is designed to handle a wide range of aluminium profiles and sections, allowing manufacturers to create complex shapes, arcs, and curves with ease.3. Adjustable Bending Speed: The machine offers adjustable bending speed, allowing manufacturers to optimize productivity based on the complexity of the job at hand.4. Easy-to-use Controls: Metfab Machines Mumbai understands the importance of efficiency in manufacturing. Hence, their machine comes equipped with user-friendly controls that streamline the bending process, minimizing errors and maximizing output.Section 3: The Advantages of Aluminium Extrusion BendingThe Aluminium Extrusion Bending Machine offered by Metfab Machines Mumbai provides numerous benefits to manufacturers and fabricators. Let's delve into some of the advantages:1. Enhanced Aesthetics: With the ability to create complex curves and shapes, aluminium extrusion bending adds a touch of elegance to various applications such as architectural designs, furniture, and signage.2. Increased Functionality: By bending aluminium profiles and sections, manufacturers can create components that fit unique specifications, optimizing functionality and performance.3. Cost-Effective Solution: Aluminium extrusion bending eliminates the need for joining multiple pieces, resulting in reduced fabrication costs, improved structural integrity, and minimized maintenance.4. Superior Strength and Durability: The bending process does not compromise the strength and durability of aluminium. Metfab Machines Mumbai's Aluminium Extrusion Bending Machine ensures that the original structural integrity of the material remains intact.Section 4: Revolutionizing Aluminium Fabrication IndustryMetfab Machines Mumbai's Aluminium Extrusion Bending Machine is a game-changer for the aluminium fabrication industry. Its exceptional capabilities, user-friendly interface, and ability to deliver precision and accuracy make it an unrivaled choice for manufacturers.Conclusion:The Aluminium Extrusion Bending Machine from Metfab Machines Mumbai shines as a cutting-edge tool in the aluminium fabrication industry. With its advanced bending technology, versatility, and ability to enhance aesthetics and functionality, this machine ensures that manufacturers can produce superior quality curved and shaped aluminium profiles and sections. By investing in this innovative solution, manufacturers unlock the power of precision and efficiency in their production processes, setting new standards in the aluminium industry.
China Offers Comprehensive Roll Forming Solution for Diverse Applications
, Roll Forming Machine, Cold Roll Forming, China Roll Forming, One-Stop Solution, Consultation, Training, Applications.Roll forming is a common metal forming process used to shape metal into a specific profile or shape. It is achieved through a series of roll forming machines that progressively shape the metal until it reaches the desired shape. This process is commonly used in the production of metal building components, automotive parts, and consumer products.China is a major player in roll forming technology, with many domestic manufacturers providing roll forming machines and solutions. One of the leading manufacturers in China is MTC, which has built a reputation for providing high-quality roll forming machines and a one-stop solution for a range of applications.The MTC roll forming machine is a cold roll former, which means that it operates at room temperature. This is in contrast to hot roll forming, which requires the metal to be preheated before forming. The advantage of cold roll forming is that it can be used on a wider range of materials, including aluminum, steel, and other metals.MTC provides a comprehensive range of roll forming machines, including panel roll forming machines, roof panel machines, wall panel machines, and more. Each machine is tailored to the specific needs of the application, ensuring optimal performance and quality.One of the unique features of MTC is its one-stop solution for roll forming applications. This includes consultation, design, manufacturing, installation, and training. The MTC team works closely with clients to understand their needs and requirements, and then provides a tailored solution that meets those needs.The consultation phase is critical in determining the most appropriate roll forming machine for the specific application. MTC’s team of experts analyze factors such as the material being used, desired throughput, and other factors to recommend the best machine for the job.Once the design has been completed, MTC manufactures the roll forming machine to the highest standards. The company uses state-of-the-art equipment and processes to ensure maximum performance and reliability.Installation is carried out by MTC’s team of trained technicians, who work closely with the client to ensure that the machine is correctly installed and fully operational.Training is also a critical component of the MTC one-stop solution. The company provides comprehensive training to clients, ensuring that they are fully versed in the operation and maintenance of the roll forming machine. This ensures that clients are able to operate the machine to its full potential, and that any maintenance or repair needs are quickly identified and addressed.MTC’s one-stop solution has been successfully implemented across a range of applications, including building construction, automotive manufacturing, and consumer goods production. The company’s expertise and commitment to quality have made it a trusted partner for businesses around the world.In summary, MTC provides a one-stop solution for roll forming applications, including consultation, design, manufacturing, installation, and training. The company's cold roll forming machines are designed to deliver the highest levels of performance and reliability, and its team of experts works closely with clients to ensure that their specific needs are met. With a focus on quality and customer service, MTC is a trusted partner for businesses seeking roll forming solutions.
V-slot Extrusion Aluminum Router/Spindle Mount for CNC Milling Machine Tool Parts M75455850120 [M75455850120] - Affordable and Versatile
Title: Enhance Your CNC Milling Experience with V-Slot Extrusion Aluminum Router/Spindle MountIntroduction:When it comes to CNC milling machines, having the right tool parts and accessories is crucial for maximizing efficiency and precision. One such essential component is the V-Slot Extrusion aluminum router/spindle mount, designed specifically for Makita/Dewalt 611/DW660/Colt OX CNC milling machines. This versatile mount offers incredible stability and durability for milling aluminum extrusions. In this blog, we will explore the benefits of this tool part and how it can revolutionize your CNC machining process.1. Superior Stability and Rigidity:The V-Slot Extrusion aluminum router/spindle mount excels in providing exceptional stability and rigidity during milling operations. Precision engineered with premium quality aluminum, this mount offers robust support to your router or spindle, reducing vibrations and ensuring accurate cuts. The V-slot design further enhances stability by securely anchoring the mount to the machine frame, minimizing unwanted movement during the milling process.2. Compatibility with Popular CNC Milling Machines:Designed with versatility in mind, this mount is compatible with major CNC milling machines such as Makita, Dewalt, DW660, and Colt OX. This widens the scope of applications, allowing users to choose their preferred milling machine without compromising on performance. Whether you are a professional or a DIY enthusiast, having a mount that fits your chosen milling machine is crucial for achieving the desired results.3. Optimal Heat Dissipation:The V-Slot Extrusion mount incorporates advanced heat dissipation features, ensuring efficient cooling during prolonged milling operations. Milling aluminum extrusions can generate significant heat, which may affect the performance and lifespan of the router or spindle. With its innovative design and aluminum construction, this mount effectively dissipates heat, promoting longevity for your machine and maintaining consistent milling accuracy.4. Easy Installation and Adjustment:Installing and adjusting the V-Slot Extrusion mount is a hassle-free process. Thanks to its intuitive design, attaching it to your CNC milling machine requires minimal effort. The mount's versatility allows for quick and precise adjustments, ensuring optimal alignment of the router or spindle. This user-friendly feature is particularly beneficial for users who frequently change router bits or require precise depth adjustments during milling operations.5. Longevity and Durability:The V-Slot Extrusion aluminum router/spindle mount is engineered to withstand the demands of CNC milling operations. Crafted from high-quality aluminum, it offers exceptional durability, withstanding the rigors of daily use in both professional and personal CNC machining settings. Its longevity ensures that you can rely on this tool part for years to come, providing you with consistent performance and precision.Conclusion:Investing in a high-quality V-Slot Extrusion aluminum router/spindle mount for your CNC milling machine is a game-changer that can transform your aluminum extrusion milling experience. The stability, compatibility, heat dissipation, easy installation, and durability offered by this mount make it an excellent addition to any CNC machining setup.So, if you are looking to optimize your CNC machining capabilities, consider upgrading to the V-Slot Extrusion aluminum router/spindle mount. Experience the enhanced stability, precision, and longevity it offers, enabling you to achieve remarkable results in your CNC milling endeavors.Keywords: CNC machine, aluminum extrusions, V-Slot Extrusion mount, router/spindle mount, Makita, Dewalt, DW660, Colt OX, stability, heat dissipation, durability, CNC milling operations.
How Forming Machines Revolutionize Production Processes
article:As automation and technology continue to revolutionize the manufacturing industry, the demand for advanced forming machines has never been greater. A leading company in the industry has recently introduced a state-of-the-art forming machine, which promises to greatly increase efficiency and accuracy in the production of metal parts and components. Let's take a closer look at this exciting development.The new forming machine, which has been designed and engineered to the highest standards, offers a number of advanced features and capabilities that set it apart from other machines on the market. Its advanced servo technology ensures consistent and precise forming, while its flexible and user-friendly controls allow for easy programming and customization. The machine can handle a wide variety of materials, including steel, aluminum, titanium, and even composites, making it a versatile and essential tool for any metalworking operation.The company behind the new forming machine is a well-established and highly respected name in the manufacturing industry. With a long history of innovation and expertise in precision engineering, the company is perfectly positioned to deliver high-quality and reliable forming solutions to its clients worldwide. Its commitment to excellence is reflected in every aspect of the new machine, from its design and construction to its operation and maintenance.But what truly sets this forming machine apart is its ability to integrate seamlessly with other systems and technologies. The machine is equipped with advanced sensors and communication protocols that allow it to exchange data and coordinate with other machines, robots, and software programs. This means that it can be easily integrated into an existing production line or used as part of a larger automation system, increasing efficiency and productivity across the entire manufacturing process.The benefits of this new forming machine are numerous, and will be felt by manufacturers across a wide range of industries. Its advanced technology and customization options will enable companies to produce parts and components that are more precise, consistent, and reliable than ever before. This will lead to higher quality products and increased customer satisfaction, which will ultimately drive growth and profitability. Additionally, the machine's integration capabilities will enable companies to streamline their operations and reduce costs, by eliminating the need for manual labor and reducing the risk of errors and defects.In conclusion, the introduction of this new forming machine is a major development in the manufacturing industry, and one that is sure to have a lasting impact on businesses around the world. The combination of advanced technology, expert engineering, and seamless integration capabilities make this machine a must-have for any company that values efficiency, quality, and innovation. As automation continues to shape and transform the manufacturing industry, it is exciting to see what new innovations and solutions will emerge, and how they will help to shape the future of manufacturing.
High-Quality Roof Sheet Forming Machines and Roll Forming Machines for Sale in China
Roof Sheet Forming Machine Manufacturer in China: Leading the Industry with Quality ProductsAs the construction industry continues to grow at an unprecedented pace, the demand for high-quality building materials and machinery continues to increase. One of these essential machines is the roof sheet forming machine, which plays a vital role in the production of roofing sheets for various commercial and industrial buildings.Enterprises in China are known for producing top-notch roofing sheet forming machines that ensure quality roofing sheets that meet customer specifications. Among these manufacturers is (remove brand name), which has been at the forefront of producing cutting-edge machinery for sheet metal fabrication, roofing, and cladding.With years of experience in the industry, (remove brand name) has developed into a reliable and trustworthy partner for clients from all over the world. Their roof sheet forming machines are world-class, featuring advanced technology that ensures the production of high-quality roofing sheets and panels that meet or exceed industry standards.The Roof Sheet Forming MachineRoofing sheet forming machines, also known as roof panel roll forming machines, are specialized machines designed for the production of roofing sheets and panels. These machines work by passing strips of metal through a series of rollers, which gradually form the sheet or panel into the desired shape.Roofing sheets produced from these machines are used for a variety of building applications. They are an ideal choice for commercial, industrial, and residential buildings that require lightweight, durable, and flexible roofing materials.Roof sheet forming machines vary in size, capacity, and level of automation. At (remove brand name), the company offers a range of roofing sheet forming machines, including the Step Tile Roof Forming Machine, Corrugated Sheet Forming Machine, and Trapezoidal Sheet Forming Machine.Each of these machines has been designed to provide customers with a unique solution tailored to their needs and preferences. They are constructed using the latest technology, ensuring consistent quality and performance.Company Introduction: (remove brand name)Founded in 2009, (remove brand name) has grown to become one of the leading manufacturers of roofing sheet forming machines in China. Over the past decade, the company has continued to innovate its products, incorporating the latest technology and design features to ensure that their customers receive nothing but the best.At (remove brand name), the focus has always been on providing customers with products that meet and exceed their expectations. The company is committed to delivering quality machinery that is both reliable and cost-effective.The company's production facilities are equipped with state-of-the-art machinery that enables it to produce high-quality roofing sheet forming machines at competitive prices. The team of engineers and technicians at (remove brand name) are highly skilled and knowledgeable, and they work tirelessly to ensure that every machine is manufactured to the highest standards.Quality Assurance and Certifications(Insert company name) is committed to providing its customers with quality products that meet industry standards. The company has implemented a comprehensive quality assurance system that covers every stage of the production process.To ensure that its machines are of the highest quality, (remove brand name) works with accredited and reputable testing and certification agencies. All their machines are rigorously tested to ensure compliance with relevant regulations and certification standards, such as CE, ISO, and SGS.In conclusion, (remove brand name) has established itself as a leading manufacturer of roofing sheet forming machines in China. With a focus on quality, innovation, and customer satisfaction, the company continues to set the standards for the industry. By choosing them as a partner, customers can rest assured that they will receive nothing but the best roofing sheet forming machines.