Installing Shallow Pitch Standing Seam Metal Roof on Tar and Gravel Roof
By:Admin
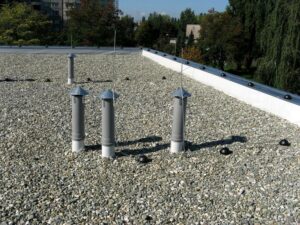
One of the main benefits of a standing seam metal roof is its durability. Metal roofs are known for their longevity and can last up to 70 years with proper maintenance. This means you won't have to replace your roof as often, saving you money on future repairs and replacements.
Additionally, metal roofs are highly resistant to weather-related damage. They can withstand harsh winds, heavy rainfall, and even hail storms. This makes them ideal for homes in areas prone to extreme weather conditions.
But that's not all! Metal roofs can also help improve the energy efficiency of your home. They reflect solar radiation, preventing your home from absorbing excess heat and reducing your cooling costs during hot summer months. They can also be designed to optimize natural ventilation, further reducing your energy consumption.
If you're worried about the aesthetic appeal of a metal roof, don't be! Standing seam metal roofs come in a variety of colors and finishes, allowing you to choose a design that complements your home's architectural style.
Best of all, installing a standing seam metal roof is quick and easy thanks to metal roof panel machines. These machines can fabricate custom panels on-site, ensuring a perfect fit for your roof. They can also help reduce waste and save time during installation.
In conclusion, a shallow pitch standing seam metal roof can be a great investment for homeowners looking to replace their old roofs. With its durability, weather resistance, energy efficiency, and aesthetic appeal, a metal roof can offer numerous benefits for years to come. So, consider a metal roof for your home and take advantage of the convenience and durability it offers!
Company News & Blog
Elegant Black and White Script Fabric - Cut Length of 60cm Panels Available for Purchase
Title: Revolutionary Fabric Cut-to-Length Machine Enhances Efficiency and Precision in Textile IndustryIntroduction:The textile industry has always been at the forefront of innovation and technological advancements. One recent breakthrough that promises to revolutionize fabric cutting processes is the introduction of the Fabric Cut-to-Length Machine by an industry-leading company. This machine is designed to streamline the production process, improve accuracy, and enhance efficiency, ultimately benefiting both manufacturers and customers alike.Enhancing Efficiency and Precision:Gone are the days when fabric cutting was a laborious and time-consuming task. The Fabric Cut-to-Length Machine offers a solution that significantly reduces production time, allowing textile manufacturers to meet increasing demands promptly. By automating the cutting process, this machine minimizes human error and ensures precise measurements and accurate fabric cuts, resulting in a higher quality end product.The introduction of the Fabric Cut-to-Length Machine has streamlined the production process by eliminating the need for manual measuring, marking, and cutting, which were traditionally prone to inaccuracies and inconsistencies. With this automated technology, manufacturers can now achieve a consistent level of precision throughout the fabric cutting process, leading to improved overall product quality.Improved Efficiency Drives Profits:Efficiency is a crucial factor in any industry, and the textile industry is no exception. One of the key features of the Fabric Cut-to-Length Machine is its ability to optimize production speed without compromising accuracy. The machine's advanced technology allows manufacturers to handle large volumes of fabric in a short time span, giving them a competitive advantage in meeting tight deadlines and reducing lead times.With decreased labor and material costs, manufacturers can allocate their resources more effectively, leading to substantial cost savings. The efficient fabric cutting process ensures that valuable textile materials are optimally utilized, minimizing waste and maximizing profits. Consequently, businesses can offer their products at competitive prices without compromising on quality, further benefiting both their bottom line and the end consumer.Eco-Friendly Practices:In addition to improving efficiency and accuracy, the adoption of the Fabric Cut-to-Length Machine promotes sustainable and eco-friendly practices within the textile industry. By minimizing fabric waste, manufacturers can reduce their environmental impact. This waste reduction not only benefits the planet, but also helps companies meet increasing consumer demand for sustainable and ethical production practices.Furthermore, the precise fabric cuts produced by the machine mean that manufacturers can have better control over the yield and usage of materials. This efficiency directly contributes to reducing the need for excessive production, thus conserving resources and minimizing carbon footprint.Conclusion:The introduction of the Fabric Cut-to-Length Machine marks a significant breakthrough in the textile industry. As demand for textiles continues to rise, manufacturers are searching for innovative solutions to meet production demands without compromising on quality or efficiency. This machine not only streamlines the fabric cutting process, but also enhances precision, reduces waste, and promotes sustainable practices.In a highly competitive market, textile manufacturers utilizing this cutting-edge technology will gain a significant advantage by producing high-quality fabrics at a faster rate. The Fabric Cut-to-Length Machine revolutionizes the industry by embracing automation, efficiency, and sustainability, ultimately benefitting businesses, consumers, and the environment.
How to Build a Sheet Metal Barn in 6 Simple Steps
Title: How to Build a Sheet Metal Barn in 6 Easy StepsIntroduction:Sheet metal barns provide an excellent solution for storage and shelter needs. Not only are they durable and cost-effective, but they can also be constructed relatively easily. In this article, we will outline a step-by-step guide on how to build a sheet metal barn in six simple steps. Whether you have experience in construction or are a DIY enthusiast, this guide will help you create your very own sheet metal barn.Step 1: Planning and PreparationBefore starting any project, careful planning is essential. Determine the size and design of your barn based on your requirements. Take measurements of the desired area and sketch out the barn's layout. Consult local building codes and acquire any necessary permits. Once you have a clear plan, gather the required materials.Step 2: Foundation and Frame ConstructionCreate a solid foundation for your sheet metal barn. Excavate the area, level the ground, and lay a sturdy foundation using concrete or treated wood. Next, construct the frame using the plywood pallets. Cut them to the desired size and connect them securely using screws and nuts, ensuring stability and durability.Step 3: Installing RoofingSelect the appropriate sheet metal for the roofing of your barn. Galvanized sheet metal provides excellent protection against rust and corrosion. Measure and cut the sheet metal to fit the roof frame, leaving a slight overhang for drainage. Secure the roofing sheets to the frame using screws or nails, ensuring proper alignment and sealing.Step 4: Wall ConstructionMeasure and cut additional plywood panels to serve as walls for your sheet metal barn. Attach them securely to the frame, leaving space for doors and windows as needed. Ensure tight joints and smooth surfaces for a professional finish.Step 5: Doors and WindowsInstall suitable doors and windows into the wall structure. Depending on your requirements, you can choose ready-made options or customize your own. Ensure proper insulation and weatherproofing to protect your belongings from the elements.Step 6: Finishing TouchesTake time to inspect your sheet metal barn for any loose screws or nails. Replace or tighten them as necessary. Consider adding ventilation systems, gutters, or additional storage options such as shelves or hooks. Apply a protective finish, such as paint or weather-resistant coatings, to increase the longevity and aesthetics of your barn.Conclusion:Building a sheet metal barn is a satisfying project that offers both functionality and durability. By following these six easy steps, you can construct your own barn and enjoy the benefits of efficient storage and shelter. Whether you are a DIY enthusiast or a seasoned builder, creating a sheet metal barn can be achieved with the right materials, tools, and patience. Embrace your creativity and get started on your own sheet metal barn project today!
Top Color Steel Glazed Tile Corrugation Equipment for Efficient Production
Color Steel Glazed Tile Corrugation Equipment Meeting Increasing Demand for Premium Building MaterialsAs the global construction industry grows in size and complexity, the demand for high-quality building materials continues to increase. In an effort to meet this demand and drive industrial innovation, Color Steel Glazed Tile Corrugation Equipment (Name of brand removed) has designed and produced a cutting-edge system that delivers premium roofing sheets and wall panels with remarkable precision and efficiency.With over 20 years of experience in manufacturing and engineering, Color Steel Glazed Tile Corrugation Equipment is a trusted leader in the industry that helps companies around the world transform their construction operations. From metal sheets and glazed tiles to corrugated panels and roof ridges, their equipment excels in delivering high-performance building materials that are essential to the construction of modern-day structures.The new Color Steel Glazed Tile Corrugation Equipment is no exception. This innovative production line takes advantage of advanced technologies to create materials that are not only visually appealing but also highly durable and weather-resistant. With a wide range of customization options, clients can easily adapt the equipment to meet their specific requirements to create roofing and wall panel products that stand out in the market.One of the key features of the Color Steel Glazed Tile Corrugation Equipment is its high level of flexibility. The production line can be used to create a wide variety of roofing and wall panel products in various shapes and sizes, including classic corrugated panels, glazed tiles, and classical tiles, both with and without an insulated core. This flexibility enables clients to offer a diverse range of products to their customers while maintaining exceptional quality and speed of production.Another major benefit of the equipment is its high level of accuracy. The production line is computer-controlled, ensuring that products are manufactured to precise standards every time. This accuracy results in dimensional stability, consistency, and perfect curvature of the final products, each of which is important to the successful completion of any construction project.At the heart of the design is the automatic color steel coil feeding and cut-to-length system, which guarantees that materials are processed quickly and efficiently with minimal waste. Additionally, the equipment features an automatic roll forming system and a pressing system for easy panel finishing and shaping.Color Steel Glazed Tile Corrugation Equipment takes pride in its machines' quality and longevity. Each production line component is made from high-quality materials and is designed by a team of experienced engineers to ensure consistent performance and long service life. Regular maintenance and customer service are also available to ensure that the equipment is operational and exceptionally dependable throughout its lifespan.Commenting on this new equipment, a spokesperson for Color Steel Glazed Tile Corrugation Equipment said, "Our innovative production line is designed to offer exceptional performance and versatility across various applications in the construction industry. Through the delivery of high-quality materials and products, we aim to provide cutting-edge solutions to our clients that enable them to stay ahead of the competition and meet the ever-increasing demands of their customers."In conclusion, the Color Steel Glazed Tile Corrugation Equipment is a versatile production line designed for the creation of high-quality building materials. With its cutting-edge technology, precision engineering, and flexibility, it is an essential tool for construction companies looking to innovate and deliver premium products to their customers. As demand for exceptional building materials continues to grow, Color Steel Glazed Tile Corrugation Equipment's new production line will provide construction companies with the competitive edge they need to succeed.
China Offers Comprehensive Roll Forming Solution for Diverse Applications
, Roll Forming Machine, Cold Roll Forming, China Roll Forming, One-Stop Solution, Consultation, Training, Applications.Roll forming is a common metal forming process used to shape metal into a specific profile or shape. It is achieved through a series of roll forming machines that progressively shape the metal until it reaches the desired shape. This process is commonly used in the production of metal building components, automotive parts, and consumer products.China is a major player in roll forming technology, with many domestic manufacturers providing roll forming machines and solutions. One of the leading manufacturers in China is MTC, which has built a reputation for providing high-quality roll forming machines and a one-stop solution for a range of applications.The MTC roll forming machine is a cold roll former, which means that it operates at room temperature. This is in contrast to hot roll forming, which requires the metal to be preheated before forming. The advantage of cold roll forming is that it can be used on a wider range of materials, including aluminum, steel, and other metals.MTC provides a comprehensive range of roll forming machines, including panel roll forming machines, roof panel machines, wall panel machines, and more. Each machine is tailored to the specific needs of the application, ensuring optimal performance and quality.One of the unique features of MTC is its one-stop solution for roll forming applications. This includes consultation, design, manufacturing, installation, and training. The MTC team works closely with clients to understand their needs and requirements, and then provides a tailored solution that meets those needs.The consultation phase is critical in determining the most appropriate roll forming machine for the specific application. MTC’s team of experts analyze factors such as the material being used, desired throughput, and other factors to recommend the best machine for the job.Once the design has been completed, MTC manufactures the roll forming machine to the highest standards. The company uses state-of-the-art equipment and processes to ensure maximum performance and reliability.Installation is carried out by MTC’s team of trained technicians, who work closely with the client to ensure that the machine is correctly installed and fully operational.Training is also a critical component of the MTC one-stop solution. The company provides comprehensive training to clients, ensuring that they are fully versed in the operation and maintenance of the roll forming machine. This ensures that clients are able to operate the machine to its full potential, and that any maintenance or repair needs are quickly identified and addressed.MTC’s one-stop solution has been successfully implemented across a range of applications, including building construction, automotive manufacturing, and consumer goods production. The company’s expertise and commitment to quality have made it a trusted partner for businesses around the world.In summary, MTC provides a one-stop solution for roll forming applications, including consultation, design, manufacturing, installation, and training. The company's cold roll forming machines are designed to deliver the highest levels of performance and reliability, and its team of experts works closely with clients to ensure that their specific needs are met. With a focus on quality and customer service, MTC is a trusted partner for businesses seeking roll forming solutions.
Short Lead Time for Plastic PVC Profile Making Machine - PE Hollow Grid Sheet Production Line by JEEBO Machinery: China Qingdao JBD Machinery Introduction
PE Hollow profile sheet is becoming an increasingly popular material in various industries due to its unique properties. With its high light transmittance, weather resistance, fire resistance, impact resistance, lightweight nature, heat insulation, and UV resistance, it has a wide range of applications.One of the main applications of PE Hollow profile sheet is in light covers. Due to its high light transmittance, it allows light to pass through easily, providing ample illumination while still offering protection. This makes it ideal for use in lighting fixtures, such as lamps, ceiling lights, and outdoor lighting. The transparent nature of the sheet ensures that the full brightness of the light source is maintained, without any loss in intensity.Another common application of PE Hollow profile sheet is in greenhouses. Its weather resistance and light transmittance properties make it an ideal material for creating a controlled environment for plants to grow. The sheet allows sunlight to enter the greenhouse, providing the necessary light for photosynthesis, while protecting the plants from harsh weather conditions. Its UV resistance ensures that the plants are not exposed to harmful rays, preventing damage and ensuring healthy growth.PE Hollow profile sheet is also widely used in interior decor. Its lightweight nature makes it easy to handle and install, allowing for creative design possibilities. It can be used to create partitions, room dividers, ceiling panels, and decorative screens. The sheet's high light transmittance can be utilized to create a bright and open space, while its impact resistance ensures durability and longevity.Soundproofing is another application where PE Hollow profile sheet excels. Its unique structure and material composition make it an effective barrier against sound waves. The sheet can be used to create soundproof partitions, walls, and enclosures, reducing noise levels and providing a peaceful environment. Whether it is for residential, commercial, or industrial applications, the sheet's soundproofing properties make it a valuable asset.When it comes to manufacturing PE Hollow profile sheet, a Profile Sheet Making Machine is essential. This machine is specifically designed to produce high-quality profile sheets with precision and efficiency. The Short Lead Time for Plastic PVC Profile Making Machine offered by JEEBO Machinery in China is an excellent choice for this purpose.By investing in this state-of-the-art machine, manufacturers can ensure a smooth and seamless production process. The machine's advanced features and technology enable it to produce profile sheets with consistent quality, meeting the required specifications. Its short lead time ensures a quick turnaround, allowing manufacturers to fulfill customer orders promptly.With the increasing demand for PE Hollow profile sheet, it is crucial to have a reliable and efficient Profile Sheet Making Machine. JEEBO Machinery, with its years of experience and expertise in the industry, provides top-quality machines that are designed to meet the diverse needs of manufacturers. Their commitment to delivering exceptional products and services has made them a trusted name in the market.In conclusion, PE Hollow profile sheet has revolutionized many industries due to its exceptional properties. Whether it is for light covers, greenhouses, interior decor, soundproofing, or any other application, this versatile material offers numerous advantages. To ensure a smooth production process and high-quality output, investing in a reliable Profile Sheet Making Machine is crucial. JEEBO Machinery stands out as a leading manufacturer in China, providing top-notch machines with a short lead time. With their expertise and commitment to customer satisfaction, they are the ideal choice for all profile sheet manufacturing needs.
Cold Roll Forming Machine for Steel Processing Equipment
If you are in the market for a purlin roll forming machine, then look no further than our CZ interchange purlin roll forming machine. As a professional manufacturer, we have exported our machines to various countries, including India and Dubai. With our machine, you can expect excellent quality at a low price.One of the advantages of our CZ interchange purlin roll forming machine is its versatility. It can handle different thickness materials, ranging from 1.5mm to 3.0mm. Additionally, it can produce both C and Z shape purlins, with the size ranging from 80mm to 300mm. This flexibility allows you to meet the requirements of various projects.Another key feature of our CZ interchange purlin roll forming machine is its ability to easily switch between C and Z types. This means that you can efficiently produce different types of purlins without the need for significant adjustments or additional equipment. This feature adds convenience and saves you time and effort.To ensure the stability and durability of our machine, we have opted for an iron cast structure. This robust design guarantees the machine's longevity and provides a stable platform for producing high-quality purlins. You can rely on our machine to consistently deliver excellent results.When it comes to applications, our CZ interchange purlin roll forming machine is ideal for steel processing. Whether you are involved in construction, manufacturing, or any other industry that requires purlins, our machine can meet your needs. It is capable of efficiently producing purlins of various shapes and sizes, making it a versatile tool for your business.In conclusion, our CZ interchange purlin roll forming machine offers numerous advantages that make it a top choice for individuals and businesses in need of a reliable and versatile purlin forming machine. With its ability to handle different thickness materials, produce various shapes and sizes, and easily switch between C and Z types, our machine provides the flexibility and convenience you require. Additionally, its iron cast structure ensures stability and durability. Invest in our CZ interchange purlin roll forming machine and take your production capabilities to the next level.
Coil-Fed Cutting Machine for Metal and Sheet Metal Applications - Laser and Fiber Laser Technology Available
Sheet Metal Coil Cutting Machine - DANOBAT LB - The Ultimate Solution for Your Cutting NeedsAre you in search of a reliable and efficient cutting solution for your sheet metal needs? Look no further than the DANOBAT LB coil-fed cutting machine. This state-of-the-art machine is designed for the metalworking industry to provide precise and efficient cutting of sheet metal.The DANOBAT LB coil-fed cutting machine is perfect for cutting sheet metal because it feeds the material directly from a coil, allowing for continuous and uninterrupted cutting. This means that there is no need to stop and reload sheets, which saves time and increases productivity.The cutting machine is equipped with fiber laser technology, which provides superior cutting quality and enhances precision. It can cut through a wide range of materials, including stainless steel, aluminum, and brass, making it a versatile choice for a variety of applications.The DANOBAT LB coil-fed cutting machine is easy to operate, with a user-friendly interface that allows operators to quickly and easily make adjustments to the cutting process. With its high-speed processing and high-precision cutting, it can easily handle complex shapes and intricate patterns.This cutting machine also boasts an advanced software system that allows for easy programming and automation of the cutting process. This means that it can run continuously with minimal operator intervention, saving time and reducing labor costs.In addition to its many features and benefits, the DANOBAT LB coil-fed cutting machine is built to last. It is constructed with high-quality materials and components, ensuring that it will provide reliable and consistent performance for years to come.If you're looking for a cutting solution that will increase your productivity and provide high-quality, precise cuts, consider the DANOBAT LB coil-fed cutting machine. With its advanced technology, user-friendly interface, and durable construction, it's the ultimate solution for all your cutting needs.
V-slot Extrusion Aluminum Router/Spindle Mount for CNC Milling Machine Tool Parts M75455850120 [M75455850120] - Affordable and Versatile
Title: Enhance Your CNC Milling Experience with V-Slot Extrusion Aluminum Router/Spindle MountIntroduction:When it comes to CNC milling machines, having the right tool parts and accessories is crucial for maximizing efficiency and precision. One such essential component is the V-Slot Extrusion aluminum router/spindle mount, designed specifically for Makita/Dewalt 611/DW660/Colt OX CNC milling machines. This versatile mount offers incredible stability and durability for milling aluminum extrusions. In this blog, we will explore the benefits of this tool part and how it can revolutionize your CNC machining process.1. Superior Stability and Rigidity:The V-Slot Extrusion aluminum router/spindle mount excels in providing exceptional stability and rigidity during milling operations. Precision engineered with premium quality aluminum, this mount offers robust support to your router or spindle, reducing vibrations and ensuring accurate cuts. The V-slot design further enhances stability by securely anchoring the mount to the machine frame, minimizing unwanted movement during the milling process.2. Compatibility with Popular CNC Milling Machines:Designed with versatility in mind, this mount is compatible with major CNC milling machines such as Makita, Dewalt, DW660, and Colt OX. This widens the scope of applications, allowing users to choose their preferred milling machine without compromising on performance. Whether you are a professional or a DIY enthusiast, having a mount that fits your chosen milling machine is crucial for achieving the desired results.3. Optimal Heat Dissipation:The V-Slot Extrusion mount incorporates advanced heat dissipation features, ensuring efficient cooling during prolonged milling operations. Milling aluminum extrusions can generate significant heat, which may affect the performance and lifespan of the router or spindle. With its innovative design and aluminum construction, this mount effectively dissipates heat, promoting longevity for your machine and maintaining consistent milling accuracy.4. Easy Installation and Adjustment:Installing and adjusting the V-Slot Extrusion mount is a hassle-free process. Thanks to its intuitive design, attaching it to your CNC milling machine requires minimal effort. The mount's versatility allows for quick and precise adjustments, ensuring optimal alignment of the router or spindle. This user-friendly feature is particularly beneficial for users who frequently change router bits or require precise depth adjustments during milling operations.5. Longevity and Durability:The V-Slot Extrusion aluminum router/spindle mount is engineered to withstand the demands of CNC milling operations. Crafted from high-quality aluminum, it offers exceptional durability, withstanding the rigors of daily use in both professional and personal CNC machining settings. Its longevity ensures that you can rely on this tool part for years to come, providing you with consistent performance and precision.Conclusion:Investing in a high-quality V-Slot Extrusion aluminum router/spindle mount for your CNC milling machine is a game-changer that can transform your aluminum extrusion milling experience. The stability, compatibility, heat dissipation, easy installation, and durability offered by this mount make it an excellent addition to any CNC machining setup.So, if you are looking to optimize your CNC machining capabilities, consider upgrading to the V-Slot Extrusion aluminum router/spindle mount. Experience the enhanced stability, precision, and longevity it offers, enabling you to achieve remarkable results in your CNC milling endeavors.Keywords: CNC machine, aluminum extrusions, V-Slot Extrusion mount, router/spindle mount, Makita, Dewalt, DW660, Colt OX, stability, heat dissipation, durability, CNC milling operations.
Ultimate Guide 2020: Roll Forming Process from Concept to Production
Title: Mastering the Roll Forming Process: A Comprehensive Guide to Horizontal Profiled Panel Roll FormingIntroduction: In the modern world of manufacturing, roll forming has emerged as a highly efficient and cost-effective method for shaping flat metal sheets into complex profiles. Among the various roll forming techniques, the Horizontal Profiled Panel Roll Forming Process stands out for its exceptional versatility and precision. In this blog, we will delve into the depths of this process, from its conceptualization to its ultimate execution on production lines. Join us on this ultimate guide for a detailed understanding.1. Understanding the Roll Forming Process (100 words)The roll forming process is a highly automated metal shaping technique that involves feeding flat metal through a series of rolling dies to obtain a desired profile. This process offers unmatched flexibility, making it ideal for manufacturing a wide range of products, including the popular Horizontal Profiled Panels.2. Key Components and Their Functions (200 words)a. Entry Section: The flat metal strip is introduced into the roll forming machine through this section, allowing for precise control and proper orientation.b. Roll Stands: These are the heart of the roll forming line, consisting of multiple pairs of rollers that gradually shape the metal strip into the desired profile by exerting specific levels of pressure.c. Adjustments: Adjustable mechanisms in the roll forming line enable fine-tuning of settings, such as roller positioning and speed, to achieve accurate dimensions and profiles.d. Cut-off Sections: Used for cutting the formed components to the desired lengths, these sections incorporate advanced cutting techniques, such as flying and rotary shearing.3. Unleashing the Potential: Concept to Production (300 words)a. Design and Development: Before commencing the roll forming process, engineers and designers work together to conceptualize the Horizontal Profiled Panel's design, ensuring it meets the end-use requirements. Computer-aided design (CAD) software plays a crucial role in this phase.b. Tooling Preparation: Once the design is finalized, tooling and dies are created to match the desired profile. Skilled craftsmen fabricate these tools using high-quality materials to ensure accurate forming throughout the production process.c. Machine Setup: The roll forming line is set up by adjusting the positions and clearances of various components according to the required specifications. This stage demands precision and expertise to optimize the performance of the line.d. Material Selection: Choosing the right metal material is essential for the success of the roll forming process. Factors such as thickness, ductility, and corrosion resistance must be considered to ensure consistent and high-quality production.e. Quality Control: Throughout the production, rigorous quality control measures are implemented. Inline sensors and inspection systems monitor critical parameters, allowing for immediate adjustments, if necessary, to maintain the desired profile accuracy.f. Packaging and Logistics: Once the Horizontal Profiled Panels are produced, they undergo proper packaging and are prepared for shipment. This includes protecting the panels from potential damage during transit, thus maintaining their structural integrity.g. Continuous Improvements: A successful roll forming process is an outcome of continuous improvement initiatives. Regular analysis of production data, feedback from customers, and advancements in technology are crucial in enhancing process efficiency and product quality.Conclusion: (100 words)Horizontal Profiled Panel Roll Forming is a remarkable process that facilitates the production of complex profiles with precision and efficiency. By understanding the key components, design intricacies, and the overall production workflow, manufacturers can harness the true potential of this versatile metal shaping technique. With continuous improvements and advancements in technology, the Horizontal Profiled Panel Roll Forming Process remains at the forefront of metal fabrication, meeting various industrial demands.
Revolutionizing the Metal Roofing Industry: Innovative Roofing Machines For A Faster Installation Process
Metal Roofing Machines Expands to Meet Growing Demands for Quality Roofing SolutionsWith the growing demand for durable and energy-efficient roofing solutions, Metal Roofing Machines has expanded its manufacturing capabilities, offering high-quality and dependable metal roofing machines for contractors and builders across the United States.Metal Roofing Machines is a family-owned and operated business that has been in the roofing industry for over two decades. The company has established a reputation for producing state-of-the-art metal roofing machines that are designed to meet the needs of contractors and builders of all sizes.The company's metal roofing machines are manufactured to the highest standards of quality and durability, using only top-grade materials and cutting-edge technology. Metal Roofing Machines' products are designed to offer maximum longevity and performance, while ensuring that they are easy to operate and maintain."We understand the importance of having access to reliable and efficient metal roofing machines," says the company spokesperson. "Our products are designed to meet the needs of the modern roofing industry, where time and efficiency are critical factors."Metal Roofing Machines' range of products includes portable roll formers, standing seam roll formers, roofing panel roll formers, gutter machines, and other specialty machines for the metal roofing industry. The company's machines are suitable for use in a variety of applications, including residential roofing, commercial roofing, and agricultural roofing.The standing seam roll former is the most popular machine distributed by Metal Roofing Machines. This machine is designed to produce standing seam roofing panels, which are popular for their clean, modern look and superior weather resistance. This machine is capable of producing high-quality panels quickly, ensuring that contractors are able to complete their roofing projects efficiently.In addition to manufacturing and distributing metal roofing machines, Metal Roofing Machines also provides education and training to contractors and builders who want to learn more about the metal roofing industry. The company offers a range of resources, including online tutorials, webinars, and in-person training sessions, designed to help contractors and builders improve their skills and stay up-to-date with the latest trends and technologies."We are committed to providing our customers with the best possible support," says the company spokesperson. "We believe that by educating our customers and providing them with the resources they need to succeed, we can help them grow their businesses and provide top-quality roofing solutions to their clients."Metal Roofing Machines has established itself as a leader in the metal roofing industry, thanks to its commitment to quality, innovation, and customer support. With its expanded manufacturing capabilities and growing range of products, the company is well-positioned to meet the demand for high-quality and reliable metal roofing solutions in the years to come.