Discover the Latest Advancements in Roofing Metal Forming Machines
By:Admin
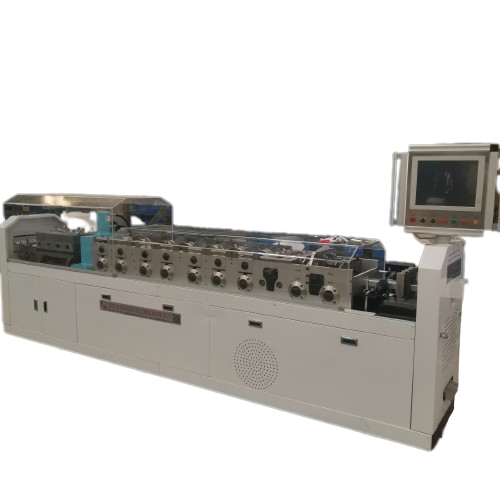
Roofing Metal Forming Machine (need remove brand name), a leading manufacturer and supplier of metal forming machines, offers an efficient solution for producing metal roofing sheets. The machine is designed to provide a cost-effective and reliable method for manufacturing roofing sheets while meeting the required specifications.
The company has gained a reputation as a trusted supplier of metal forming machines due to its focus on quality, reliability, and innovation. By combining advanced technology with skilled engineering, the company has created a range of metal forming machines that offer superior performance, efficiency, and durability.
The Roofing Metal Forming Machine (need remove brand name) is an excellent example of the company's commitment to innovation and quality. The machine is designed to produce high-quality roofing sheets with consistent thickness, length, and width. It is capable of processing different types of metal, including steel, aluminum, and copper, with varying thicknesses and widths.
One of the main advantages of the Roofing Metal Forming Machine (need remove brand name) is its versatility. The machine can be customized to produce roofing sheets of different profiles, including corrugated, trapezoidal, and standing seam profiles. This flexibility enables manufacturers to cater to different market requirements and produce roofing sheets that meet the specific needs of their customers.
The machine is also easy to operate, thanks to its user-friendly interface and automated features. The operator can easily program the machine to produce roofing sheets with the desired length and width, and the machine will automatically adjust its settings to ensure consistent quality and accuracy.
The Roofing Metal Forming Machine (need remove brand name) is also designed to reduce material waste, which is a major concern for manufacturers in the metal forming industry. The machine is equipped with a precision cutting system that minimizes material waste and ensures optimal usage of raw materials.
In addition to its outstanding performance and efficiency, the Roofing Metal Forming Machine (need remove brand name) is also known for its durability and low maintenance requirements. The machine is built to withstand heavy-duty usage and can operate continuously for extended periods with minimal downtime.
The company offers comprehensive support services to ensure that its customers get the most out of their investment in the Roofing Metal Forming Machine (need remove brand name). The services include installation, training, and ongoing technical support, which enable customers to operate the machine efficiently and maximize their production output.
Overall, the Roofing Metal Forming Machine (need remove brand name) is a reliable and cost-effective solution for manufacturing high-quality metal roofing sheets. Its advanced features, versatility, and user-friendly interface make it an excellent choice for manufacturers looking to optimize their production processes and increase their competitiveness in the market.
About the Company
Roofing Metal Forming Machine (need remove brand name) is a leading manufacturer and supplier of metal forming machines. The company specializes in designing and producing machines for the metal roofing and cladding industry, including roll forming machines, slitting machines, and cut-to-length machines.
The company has been in business for over 20 years and has gained a reputation for its commitment to quality, reliability, and innovation. Its machines are used by manufacturers in various industries across the world, including Europe, North America, South America, Africa, and Asia.
Roofing Metal Forming Machine (need remove brand name) has a team of skilled engineers and technicians who use advanced technology and materials to create machines that meet the highest standards. The company also offers comprehensive support services, including installation, training, and technical support, to ensure that its customers get the most out of their investment.
Company News & Blog
How to Choose the Best Glazed Roof Sheet Making Machine
[Company Name], a leading manufacturing company in the construction industry, has recently introduced its latest innovation - the Glazed Roof Sheet Making Machine. With this advanced machinery, the company aims to revolutionize the way roof sheets are produced, making them more durable, aesthetically pleasing, and efficient.Roof sheets play a crucial role in protecting buildings from various weather conditions such as rain, wind, and snow. However, traditionally produced roof sheets often lack the desired durability and aesthetic appeal. Recognizing this gap in the market, [Company Name] developed the Glazed Roof Sheet Making Machine to address these concerns.One of the key features of this machine is its ability to produce roof sheets with a glazed finish. This glazed coating not only enhances the appearance of the sheets but also provides an additional layer of protection against rust, corrosion, and UV rays. The sheets produced by this machine are designed to withstand extreme weather conditions, ensuring the longevity of the roofs they cover.Moreover, the Glazed Roof Sheet Making Machine incorporates cutting-edge technology to improve the overall efficiency of the production process. Equipped with advanced automation systems, the machine reduces the need for manual labor, thus increasing productivity and minimizing human errors. This ensures that the roof sheets are manufactured at a faster pace and with greater precision.Furthermore, [Company Name] has placed a strong emphasis on sustainability when developing this machine. The Glazed Roof Sheet Making Machine is designed to optimize material usage, minimizing waste and reducing environmental impact. The company has also integrated energy-saving features into the machinery, making it more energy-efficient and less harmful to the planet.In addition to its impressive features, the Glazed Roof Sheet Making Machine is backed by [Company Name]'s years of expertise in the construction industry. With a strong commitment to quality and innovation, the company has established a reputation for delivering superior products and services."We are thrilled to introduce the Glazed Roof Sheet Making Machine to the market," said [Spokesperson Name], the spokesperson for [Company Name]. "We believe this machine will revolutionize the way roof sheets are produced, providing our clients with durable, aesthetically pleasing, and highly efficient solutions."[Company Name] prides itself on its dedication to customer satisfaction. The company not only offers top-of-the-line machinery but also provides comprehensive after-sales support. Their qualified technicians are available to assist clients with installation, training, and maintenance, ensuring a seamless experience throughout the lifespan of the Glazed Roof Sheet Making Machine.With the introduction of the Glazed Roof Sheet Making Machine, [Company Name] aims to establish itself as a leader in the roofing industry. By combining innovation, sustainability, and exceptional customer service, the company continues to push boundaries and set new standards for the construction sector.The Glazed Roof Sheet Making Machine is set to revolutionize the roofing industry, providing superior-quality, visually appealing, and durable roof sheets that meet the demands of modern construction projects. With this groundbreaking innovation, [Company Name] secures its position as an industry leader, committed to delivering excellence in every aspect of its operations.
Roll Forming Machine, Cold Roll Forming Machine, Sandwich Panel Machine, Roof Tile Roll Forming Machine, Wall Panel Roll Forming Machine, Steel Roll Forming Machine, Glazed Tile Roll Forming Machine, Ridge Cap Roll Forming Machine, IBR Roll Forming Machine, Corrugated Roll Forming Machine, Floor Deck Roll Forming Machine, Highway Guardrail Roll Forming Machine, Stud and Track Roll Forming Machine, Furring Channel Roll Forming Machine, Downpipe Roll Forming Machine, Gutter Machine, Roller Shutter Door Forming Machine, K Span Roll Forming Machine, Door Frame Roll Forming Machine, Standing Seam Roof Panel Roll Forming Machine, Bemo Panel Roll Forming Machine, Shelf Roll Forming Machine, Cable Tray Roll Forming Machine, Slitting & Cutting Machine, Roof Curving Machine, Embossing Machine
Title: Innovations in Roll Forming Machines - Revolutionizing Construction IndustryIntroduction:In the rapidly evolving construction industry, the use of advanced machinery and equipment has become crucial to enhance productivity and efficiency. Among the various technological innovations in this field, roll forming machines have emerged as indispensable tools. These machines play a pivotal role in the production of metal sheets and panels used in roofing, wall cladding, and other construction applications.Roll Forming Machine: Transforming Metal Sheets with PrecisionRoll forming machines, also known as roll formers, are highly versatile manufacturing machines used to transform flat metal sheets into complex and customized profiles used in construction. They utilize a continuous bending operation by passing the sheet metal through a series of rolling dies. The process involves shaping the metal into a desired cross-section profile while maintaining uniform thickness throughout the length.Cold Roll Forming Machine: Enhancing Precision and DurabilityCold roll forming machines have gained immense popularity due to their ability to work with a wide range of materials, including steel, aluminum, copper, and more. This type of roll forming machine operates at room temperature, minimizing the risk of thermal damage to the metal. Cold roll forming ensures higher uniformity in the end products, offering superior dimensional accuracy, strength, and durability.Sandwich Panel Machine: Efficient Insulation SolutionsThe use of sandwich panels in construction has gained significant traction, primarily due to their excellent thermal and sound insulation properties. Sandwich panel machines are specifically designed to produce panels with an insulating core material, such as EPS (Expanded Polystyrene), rock wool, or mineral wool, sandwiched between two outer sheets. These panels find applications in roofing, wall cladding, and other structural elements, offering energy efficiency and environmental benefits.Revolutionizing the Manufacturing Process:- EPS/Rock wool/Mineral wool sandwich panel machine: This advanced technology enables the efficient production of insulated panels, offering enhanced temperature regulation and noise reduction in buildings.- Glazed Tile Roll Forming Machine: Utilizing high-quality materials, this machine produces aesthetically appealing glazed tiles for roofing applications. The precise roll forming process ensures dimensional accuracy and long-lasting performance.- Standing Seam Roof Panel Roll Forming Machine: This machine revolutionizes the production of standing seam roof panels, which are popular for their exceptional weather resistance and stylish appearance.- Double Layer Roll Forming Machine: Ideal for large-scale projects, this machine efficiently produces two different profiles simultaneously, reducing production time and costs.- Highway Guardrail Roll Forming Machine: As road safety remains a paramount concern, this machine manufactures sturdy guardrails, protecting motorists and minimizing accidents.Expanding Possibilities with Advanced Features:Modern roll forming machines come equipped with advanced features such as computer numerical control (CNC) systems, automated feeders, and precision cutting mechanisms, ensuring high productivity, reliability, and time efficiency. These features allow for customization and adaptation to different profile designs.Conclusion:The roll forming machine industry has witnessed substantial advancements in recent years, fueling innovative manufacturing processes in the construction sector. The introduction of cold roll forming machines, sandwich panel machines, and other specialized equipment has enabled the production of high-quality, customized metal profiles and panels. As technology continues to evolve, these machines will play a vital role in shaping the infrastructure of our future.For further information or inquiries, interested parties are encouraged to contact Ms. Monica Lee, who will provide detailed information and the best prices for the required profile drawings or specifications.Contact Person: Ms. Monica LeeWebsite: (brand name removed)Disclaimer: This news content is for information purposes only and does not serve as an endorsement for any specific brand or company.
High-Speed Corrugated Roll Forming Machine with Hydraulic Cutting - Ideal for 914mm and 1220mm Coil Width
Corrugated Sheet Forming Machine: A Revolutionary Solution for Modern BuildingBuilding construction is a vital industry that contributes significantly to the economy. Architects, builders, and property owners strive to create structures that are resilient and aesthetically appealing. However, the process requires heavy investment, and it's vital to use the best materials and tools. One crucial material is the corrugated sheet, which has become popular due to its durability, cost-effectiveness, and versatility. This is where the Corrugated Sheet Forming Machine comes in.The Corrugated Sheet Forming Machine is an innovative solution that has revolutionized the modern building industry. It is a machine designed to transform flat metal sheets into corrugated sheets, which are widely used for roofing, siding, and cladding applications. The machine uses a series of roller dies to create the corrugated profile, which can be customized to different shapes and sizes. It is a fast, efficient, and highly accurate way to produce high-quality corrugated sheets.One of the most important features of the Corrugated Sheet Forming Machine is its motorized cutting and fast drive system. This system allows for quick and easy processing of metal sheets, reducing the time and effort required to create corrugated sheets. Additionally, the hydraulic cutting system ensures precise cutting and minimal waste, further enhancing the machine's efficiency. The machine's 836 type, lengthened design, and 1220 mm coil width make it suitable for producing large volumes of sheets, making it ideal for commercial applications.The Corrugated Sheet Forming Machine is also highly customizable, allowing operators to create different corrugated profiles. This flexibility allows architects and builders to create unique designs that match their clients' preferences. The machine's versatility is further improved by its ability to process different metals, including galvanized steel, aluminum, and copper. This means that users can choose the material that best fits their project requirements, depending on factors such as durability, cost, and aesthetics.In conclusion, the Corrugated Sheet Forming Machine is an essential tool for the modern building industry. Its speed, accuracy, and versatility make it ideal for producing high-quality corrugated sheets for various applications. Whether you are constructing a commercial building, a residential house, or a metal structure, this machine can help you achieve your goals. If you are looking for a reliable and cost-effective way to produce corrugated sheets, the Corrugated Sheet Forming Machine is the perfect solution.
High-Quality Metal Slitting Line for Sale – Different Gauges Available at SteelSlitter.com
RISHBIN Emerges as a Leading Slitting Line Machine Manufacturer Offering High-Quality Metal Slitting Line for SaleIn the dynamic world of manufacturing, industries are constantly seeking efficient and reliable solutions to meet their production needs. RISHBIN, a prominent player in the market, has emerged as one of the best slitting line machine manufacturers, offering high-quality metal slitting lines for sale. With a wide range of machines catering to different gauge requirements, RISHBIN continues to revolutionize the industry with its cutting-edge technology and exceptional product offerings.Slitting lines are a vital component of the metal processing industry, enabling precise cutting and resizing of coils into narrower widths. When it comes to manufacturing slitting line machines, RISHBIN stands out for its commitment to delivering superior quality and innovative features. With an experienced team of engineers and technicians, the company is at the forefront of technological advancements, ensuring that their machines meet the highest industry standards.RISHBIN's metal slitting lines are designed to handle various gauge requirements, ensuring flexibility and versatility for a wide range of applications. The availability of machines suitable for light, medium, and heavy gauge materials makes RISHBIN the go-to manufacturer for businesses operating in diverse sectors. Whether it's the automotive, construction, or packaging industry, RISHBIN's slitting lines provide optimal performance and accuracy.What sets RISHBIN apart from its competitors is its continuous focus on research and development. The company invests heavily in innovation, constantly enhancing its product offerings to meet evolving industry demands. By staying up-to-date with the latest technological advancements, RISHBIN ensures that its slitting line machines provide the most efficient and reliable solutions for its customers.In addition to its dedication to quality and innovation, RISHBIN is also renowned for its exceptional customer service. The company believes in establishing long-term relationships with its clients, prioritizing their needs and exceeding their expectations. RISHBIN's team of experts assists customers throughout the entire purchasing process, offering valuable guidance and support to help them make informed decisions.RISHBIN's commitment to quality and customer satisfaction is further reflected in its post-sales services. The company offers comprehensive maintenance and technical support to ensure that its machines continue to perform optimally throughout their lifespan. By providing timely servicing and spare parts availability, RISHBIN helps its customers maximize their productivity and minimize downtime.With its robust manufacturing capabilities, RISHBIN ensures that each slitting line machine is crafted to perfection. The company utilizes high-quality materials and rigorous quality control processes to guarantee the durability and efficiency of its products. RISHBIN's metal slitting lines are built to withstand heavy usage and deliver consistent performance, making them a reliable investment for businesses looking to enhance their manufacturing processes.As a socially responsible organization, RISHBIN is committed to sustainability and environmentally friendly practices. The company implements energy-efficient measures throughout its manufacturing processes, reducing its carbon footprint and promoting a greener future. By choosing RISHBIN's slitting line machines, customers not only benefit from high performance but also contribute to global sustainability efforts.In conclusion, RISHBIN has established itself as a leading slitting line machine manufacturer by delivering high-quality solutions tailored to different gauge requirements. With its focus on innovation, customer service, and sustainability, RISHBIN continues to drive the industry forward. As businesses strive for excellence in their manufacturing processes, RISHBIN's metal slitting lines emerge as the ideal choice, ensuring efficiency, accuracy, and long-term reliability.
Revolutionizing the Metal Roofing Industry: Innovative Roofing Machines For A Faster Installation Process
Metal Roofing Machines Expands to Meet Growing Demands for Quality Roofing SolutionsWith the growing demand for durable and energy-efficient roofing solutions, Metal Roofing Machines has expanded its manufacturing capabilities, offering high-quality and dependable metal roofing machines for contractors and builders across the United States.Metal Roofing Machines is a family-owned and operated business that has been in the roofing industry for over two decades. The company has established a reputation for producing state-of-the-art metal roofing machines that are designed to meet the needs of contractors and builders of all sizes.The company's metal roofing machines are manufactured to the highest standards of quality and durability, using only top-grade materials and cutting-edge technology. Metal Roofing Machines' products are designed to offer maximum longevity and performance, while ensuring that they are easy to operate and maintain."We understand the importance of having access to reliable and efficient metal roofing machines," says the company spokesperson. "Our products are designed to meet the needs of the modern roofing industry, where time and efficiency are critical factors."Metal Roofing Machines' range of products includes portable roll formers, standing seam roll formers, roofing panel roll formers, gutter machines, and other specialty machines for the metal roofing industry. The company's machines are suitable for use in a variety of applications, including residential roofing, commercial roofing, and agricultural roofing.The standing seam roll former is the most popular machine distributed by Metal Roofing Machines. This machine is designed to produce standing seam roofing panels, which are popular for their clean, modern look and superior weather resistance. This machine is capable of producing high-quality panels quickly, ensuring that contractors are able to complete their roofing projects efficiently.In addition to manufacturing and distributing metal roofing machines, Metal Roofing Machines also provides education and training to contractors and builders who want to learn more about the metal roofing industry. The company offers a range of resources, including online tutorials, webinars, and in-person training sessions, designed to help contractors and builders improve their skills and stay up-to-date with the latest trends and technologies."We are committed to providing our customers with the best possible support," says the company spokesperson. "We believe that by educating our customers and providing them with the resources they need to succeed, we can help them grow their businesses and provide top-quality roofing solutions to their clients."Metal Roofing Machines has established itself as a leader in the metal roofing industry, thanks to its commitment to quality, innovation, and customer support. With its expanded manufacturing capabilities and growing range of products, the company is well-positioned to meet the demand for high-quality and reliable metal roofing solutions in the years to come.
Plastic Corrugated Roof Tile Making Machine for Efficient Roofing Tile Production
If you are considering venturing into the roof tile manufacturing business, then it might be a good idea to invest in a plastic corrugated / glazed roof tile making machine. The equipment is versatile and can produce a range of roofing tiles with different styles and designs.At Jiangsu Acemien Machinery Co., Ltd. (ACEMIEN for short), we offer state-of-the-art PVC+ASA co-extrusion roof tile making machines that are designed to meet the demands of modern roofing tile production. Our machines are compact and efficient, and can produce tiles with high quality and accuracy.One of the primary advantages of our corrugated roll making machine is that it uses PVC and ASA materials in the co-extrusion process. PVC (polyvinyl chloride) is a plastic material that has excellent toughness, chemical resistance, and weatherability. ASA (acrylonitrile-styrene-acrylate) is a thermoplastic material that combines the properties of acrylics and styrene plastics.When the two materials are co-extruded, the resultant roofing tiles exhibit superior resistance to weather, UV radiation, and impact. They are also easy to install and maintain, which makes them a popular choice for homeowners and commercial property owners alike.Our PVC+ASA co-extrusion roof tile making machines can produce tiles with various shapes, sizes, colors, and textures. The corrugated roll forming machine can create tiles with a corrugated or waved surface, while the glazed roof tile making machines can generate tiles with a smooth or glossy finish.Our machines are equipped with advanced PLC control systems, which enable the operator to control the various parameters of the production process. The machines also come with automatic cutting and stacking devices, which facilitate a smooth and efficient production workflow.At ACEMIEN, we prioritize the quality and durability of our machines, which is why we use high-grade materials and components in their manufacture. Our machines are designed to operate continuously for long periods, and they have low maintenance requirements, which means that they can help you save time and money in the long run.In conclusion, if you are looking to invest in a high-quality plastic corrugated / glazed roof tile making machine, then ACEMIEN is the right company for you. Our machines are versatile, efficient, and reliable, and can help you meet the demands of the modern roofing tile market. Contact us today to learn more about our PVC+ASA co-extrusion roof tile making machines, and let us help you take your business to the next level!
Versatile 1000 kg Manual Stacker with Interchangeable Attachments
As a business owner, you know that efficiency is everything. When it comes to your production line, you need machinery that is flexible, versatile, and customizable to meet your needs. That's where a manual stacker comes in.A manual stacker is an essential tool in many industries where goods need to be lifted, stacked, and transported from one area to another. The Logitrans LOGIFLEX MS 1000 kg manual stacker with articulated legs is one of the best on the market for its flexibility and versatility.One of the key features of the LOGIFLEX MS manual stacker is its interchangeable attachments. This allows you to customize the machine to meet your specific needs. Whether you need to lift and stack heavy loads, or transport smaller items across your production line, the LOGIFLEX MS can be modified to get the job done.With a 1000 kg load capacity, the LOGIFLEX MS can handle even your heaviest loads. And because it's a manual machine, you don't have to worry about the added expense of electricity or maintenance costs. Simply crank the handle to lift your load and easily and quietly transport it to its destination.The articulated legs on this manual stacker are another great feature that makes it stand out from the competition. The legs provide added stability and maneuverability, allowing you to easily navigate tight spaces and turn corners with ease.So what does all this mean for your business? If you own a C purline machine or any other production machinery, a manual stacker like the LOGIFLEX MS can help improve your productivity and efficiency. With its flexibility and customization options, you can tailor the machine to meet your specific needs and make your production line run more smoothly.In addition, using a manual stacker can also reduce the risk of workplace injuries and accidents. The LOGIFLEX MS is easy to operate and requires minimal training to use safely. And because it's a manual machine, there's no risk of electrical shocks or malfunctions that could lead to serious injuries.In conclusion, if you're looking for a reliable, flexible, and efficient manual stacker for your business, the LOGIFLEX MS 1000 kg manual stacker with articulated legs is an excellent choice. With its interchangeable attachments, high load capacity, and added stability, it can help improve your overall productivity and make your work environment safer for everyone. So why wait? Invest in a manual stacker today and start reaping the benefits of improved efficiency and safety in your workplace.
Ultimate Guide 2020: Roll Forming Process from Concept to Production
Title: Mastering the Roll Forming Process: A Comprehensive Guide to Horizontal Profiled Panel Roll FormingIntroduction: In the modern world of manufacturing, roll forming has emerged as a highly efficient and cost-effective method for shaping flat metal sheets into complex profiles. Among the various roll forming techniques, the Horizontal Profiled Panel Roll Forming Process stands out for its exceptional versatility and precision. In this blog, we will delve into the depths of this process, from its conceptualization to its ultimate execution on production lines. Join us on this ultimate guide for a detailed understanding.1. Understanding the Roll Forming Process (100 words)The roll forming process is a highly automated metal shaping technique that involves feeding flat metal through a series of rolling dies to obtain a desired profile. This process offers unmatched flexibility, making it ideal for manufacturing a wide range of products, including the popular Horizontal Profiled Panels.2. Key Components and Their Functions (200 words)a. Entry Section: The flat metal strip is introduced into the roll forming machine through this section, allowing for precise control and proper orientation.b. Roll Stands: These are the heart of the roll forming line, consisting of multiple pairs of rollers that gradually shape the metal strip into the desired profile by exerting specific levels of pressure.c. Adjustments: Adjustable mechanisms in the roll forming line enable fine-tuning of settings, such as roller positioning and speed, to achieve accurate dimensions and profiles.d. Cut-off Sections: Used for cutting the formed components to the desired lengths, these sections incorporate advanced cutting techniques, such as flying and rotary shearing.3. Unleashing the Potential: Concept to Production (300 words)a. Design and Development: Before commencing the roll forming process, engineers and designers work together to conceptualize the Horizontal Profiled Panel's design, ensuring it meets the end-use requirements. Computer-aided design (CAD) software plays a crucial role in this phase.b. Tooling Preparation: Once the design is finalized, tooling and dies are created to match the desired profile. Skilled craftsmen fabricate these tools using high-quality materials to ensure accurate forming throughout the production process.c. Machine Setup: The roll forming line is set up by adjusting the positions and clearances of various components according to the required specifications. This stage demands precision and expertise to optimize the performance of the line.d. Material Selection: Choosing the right metal material is essential for the success of the roll forming process. Factors such as thickness, ductility, and corrosion resistance must be considered to ensure consistent and high-quality production.e. Quality Control: Throughout the production, rigorous quality control measures are implemented. Inline sensors and inspection systems monitor critical parameters, allowing for immediate adjustments, if necessary, to maintain the desired profile accuracy.f. Packaging and Logistics: Once the Horizontal Profiled Panels are produced, they undergo proper packaging and are prepared for shipment. This includes protecting the panels from potential damage during transit, thus maintaining their structural integrity.g. Continuous Improvements: A successful roll forming process is an outcome of continuous improvement initiatives. Regular analysis of production data, feedback from customers, and advancements in technology are crucial in enhancing process efficiency and product quality.Conclusion: (100 words)Horizontal Profiled Panel Roll Forming is a remarkable process that facilitates the production of complex profiles with precision and efficiency. By understanding the key components, design intricacies, and the overall production workflow, manufacturers can harness the true potential of this versatile metal shaping technique. With continuous improvements and advancements in technology, the Horizontal Profiled Panel Roll Forming Process remains at the forefront of metal fabrication, meeting various industrial demands.
High-Quality Metal Roll Forming Machine Available for Purchase – Roof Panel Roll Forming Machine Supplier
Machine, Roll Forming Machine, Roof Panel Roll Forming Machine, Metal Roll Forming, Forming Machine, Metal Roll, Metal Roll Forming Machine for Sale, Buy Metal Roll Forming Machine, Metal Roll Forming Machine Wholesaler, Metal Roll Forming Machine Seller, Top-quality Metal Roll Forming Machine, Benefits of Using Metal Roll Forming Machine, Roll Forming Process, Metal Roll Forming vs Other Forming Techniques, Applications of Metal Roll Forming Machine, Factors to Consider when Buying Metal Roll Forming Machine.Title: Advancing Manufacturing with Metal Roll Forming MachineIntroduction:In the ever-evolving manufacturing industry, metal roll forming machines have become an essential tool for efficiently producing high-quality metal components. This blog will explore the benefits of using metal roll forming machines, discuss the roll forming process, compare metal roll forming with other forming techniques, highlight the applications of metal roll forming machines, and provide insights on factors to consider when purchasing these machines.Benefit 1: Top-quality Metal ComponentsMetal roll forming machines offer superior precision and accuracy in producing metal components. The continuous bending process ensures consistent dimensions, smooth edges, and precise shapes across multiple pieces, resulting in high-quality finished products. Additionally, the ability to control forming speeds and pressures allows for the production of complex and intricate designs, meeting various industry specifications.Benefit 2: Cost-effective ProductionMetal roll forming machines facilitate cost-effective production due to their ability to handle high volumes of material with minimal wastage. By using coil stock material, roll forming eliminates the need for traditional sheet metal blanks, reducing material costs and minimizing scrap. Furthermore, the continuous operation of roll formers decreases labor requirements and enhances production efficiency, ultimately reducing overall manufacturing costs.Benefit 3: Versatile ApplicationsMetal roll forming machines find applications in various industries, including automotive, construction, aerospace, and furniture. These machines offer versatility in creating a wide range of metal profiles, such as roof panels, wall cladding, gutters, window frames, and door frames. The flexibility in material thickness, width, and length allows manufacturers to cater to diverse customer requirements and adapt to market trends effectively.Roll Forming Process:The roll forming process involves feeding coil stock material into a series of contoured rolls, gradually bending and shaping the metal. As the material moves through multiple stations, the rolls progressively form the desired profile. Each station performs a specific shaping operation, such as punching, notching, embossing, or cutting. By adjusting the roll spacing, manufacturers can achieve precise dimensions and shapes. The formed metal components are then cut to the desired length using a flying shear or cut-off press.Metal Roll Forming vs Other Forming Techniques:Compared to other forming techniques like stamping and press braking, metal roll forming offers several advantages. First, roll forming allows for continuous production with minimal interruptions, reducing operational downtime. Second, roll forming eliminates the need for pre-formed blanks or separate operations for joining multiple pieces, resulting in faster production cycles. Finally, roll-formed components exhibit improved structural integrity due to the continuous grain flow, enhancing their strength and durability.Applications of Metal Roll Forming Machines:1. Automotive Industry: Metal roll forming machines are widely used in manufacturing automotive body components, including chassis, roof rails, door frames, and window frames. The ability to produce complex profiles and maintain tight tolerances makes roll forming an ideal choice for this industry.2. Construction Industry: Roll-formed profiles for roofing panels, wall cladding, and structural components are in high demand in the construction sector. The cost-effectiveness and precision of metal roll forming machines make them indispensable for producing these architectural elements.3. Furniture Industry: Roll forming technology is employed in the production of metal furniture components like frame elements, brackets, and decorative fittings. The versatility and high-quality output of metal roll forming machines contribute to the aesthetic appeal and functionality of modern furniture designs.Factors to Consider when Buying Metal Roll Forming Machines:1. Machine Size and Capacity: Consider the required profile dimensions, thickness, and material type to ensure compatibility with the selected machine's specifications.2. Material Handling and Coil Weight: Evaluate the machine's ability to handle heavy coil stock material and ensure that it suits your production requirements.3. Tooling Flexibility: Check if the machine allows for easy changeovers between different profiles and if additional tooling options are available to expand its capabilities.4. Automation and Integration: Decide if integrating automation features, like computer numerical control (CNC) systems, is necessary to enhance production efficiency and reduce human error.5. After-sales Support: Research the reputation of the manufacturer and evaluate the availability of technical support, spare parts, and maintenance services.Conclusion:Metal roll forming machines offer numerous benefits, including top-quality production, cost-effectiveness, and versatility. The roll forming process, with its continuous bending and shaping, ensures consistent dimensions and smooth edges. Metal roll forming outperforms other forming techniques in terms of efficiency, structural integrity, and faster production cycles. These machines find applications in diverse industries like automotive, construction, and furniture manufacturing. When purchasing a metal roll forming machine, considering factors such as machine size, capacity, tooling flexibility, and after-sales support will help manufacturers make informed decisions and achieve optimal results in their production processes.
Top Roof Panel Curving Machine Manufacturers in China: Find Reliable Suppliers
Roof Panel Curving Machine: A Game-Changer in the Construction IndustryThe construction industry has witnessed significant advancements in recent years, and one such innovation that has gained immense popularity is the Roof Panel Curving Machine. Manufactured by reputable companies in China, this remarkable piece of equipment has revolutionized the way roof panels are manufactured and installed, offering unmatched precision, efficiency, and durability.As a leading manufacturer, supplier, and exporter of Roof Panel Curving Machines, China has taken the construction world by storm. These machines enable architects, engineers, and builders to create roofing solutions that were previously unimaginable. Let's delve deeper into the intricate details and working mechanism of this machine to understand its noteworthy features and the benefits it offers.1. Precision in Panel Curving:One of the key advantages of the Roof Panel Curving Machine is its ability to curve roof panels with utmost precision. This machine uses advanced technology, combined with highly efficient tracking systems and sensors, to accurately curve panels according to the desired specifications. The result is a smoothly curved panel that fits perfectly, ensuring an airtight and watertight roof structure.2. Enhanced Efficiency:Gone are the days when roof panels had to be manually curved, which was a time-consuming and labor-intensive process. With the Roof Panel Curving Machine, the entire process is automated, significantly increasing efficiency while reducing labor costs. This machine can curve multiple panels simultaneously, allowing for faster completion of projects without compromising on quality.3. Adaptability to Different Materials:Roof Panel Curving Machines cater to a wide range of roofing materials, including metal, steel, aluminum, and more. Whether you're aiming for a curved roof made of standing seam metal panels or corrugated steel panels, this machine can handle it all with ease. Its adaptability to various materials makes it a versatile tool, capable of tackling diverse construction projects.4. Durability and Longevity:Constructed from high-quality materials and engineered to withstand rigorous usage, Roof Panel Curving Machines are built to last. These machines are designed to withstand the demanding conditions of the construction site, ensuring longevity and high-performance even after prolonged use. Investing in a Roof Panel Curving Machine guarantees a durable piece of equipment that will serve your construction needs for years to come.5. Cost-Effective Solution:With the Roof Panel Curving Machine, construction companies can enjoy long-term cost savings. The reduction in labor costs, improved efficiency, and decreased material waste make this machine an economically viable solution. Moreover, it eliminates the need for outsourcing panel curving services, allowing you to have complete control over the quality and timeline of your projects.In conclusion, the Roof Panel Curving Machine has transformed the construction industry by delivering exceptional precision, efficiency, and durability. With companies in China manufacturing and supplying these machines, builders and architects worldwide have access to this groundbreaking technology. By investing in this advanced equipment, construction professionals can stay ahead of the curve, streamline their operations, and create extraordinary architectural wonders.