High-Quality Metal Roof Making Machine for Sale: Find Out More
By:Admin
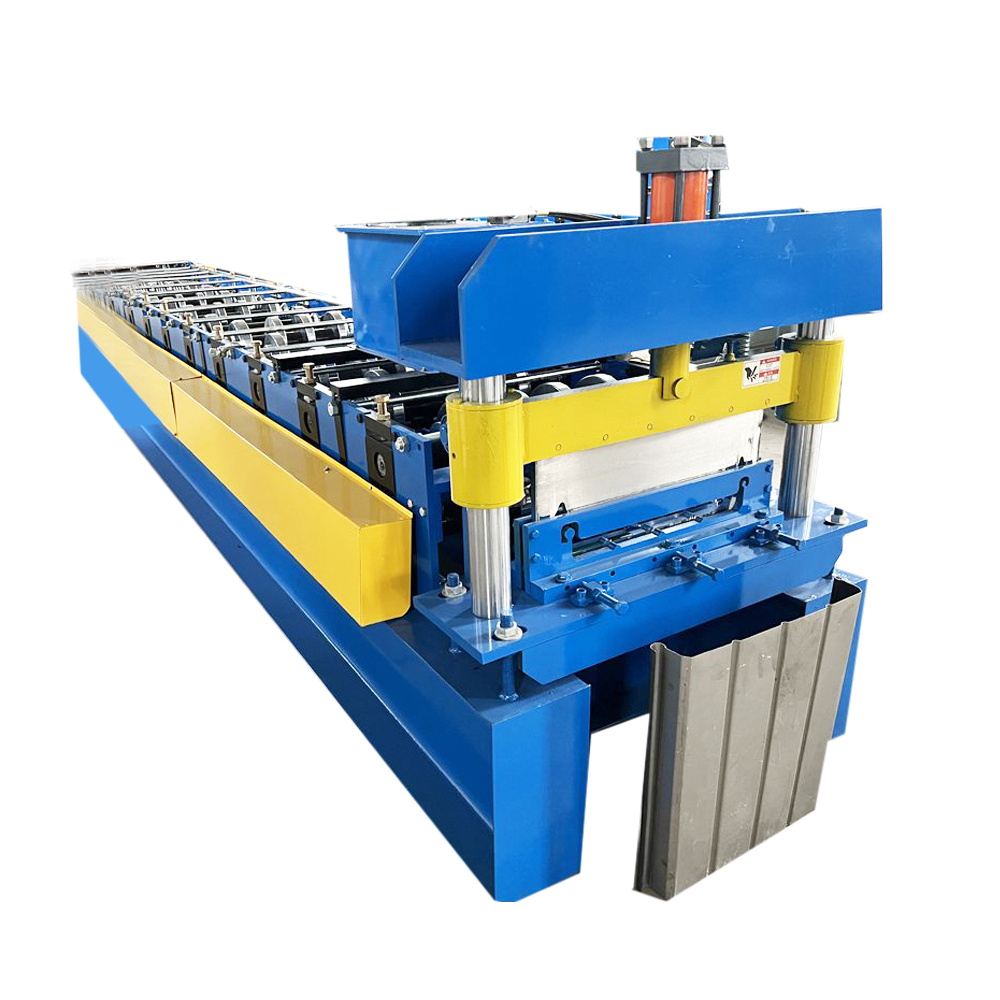
The roofing industry is constantly evolving and innovating, and one of the latest advancements that is revolutionizing the way roofs are made is the Metal Roof Making Machine. This state-of-the-art machine, manufactured by a leading company in the industry, is changing the game for roofing contractors and manufacturers.
With the ability to produce high-quality metal roofing panels at a fraction of the time and cost of traditional methods, this machine is a game-changer for the industry. The Metal Roof Making Machine is designed to streamline the production process, allowing for faster and more efficient manufacturing of metal roofing panels. This means that roofing contractors can now meet tight deadlines and take on more projects, ultimately increasing their bottom line.
The Metal Roof Making Machine is equipped with cutting-edge technology that allows for precision and accuracy in panel production. This means that each panel is of the highest quality, ensuring that the end result is a durable and long-lasting roof. Additionally, the machine is versatile and can produce a wide variety of panel designs and sizes, giving contractors and manufacturers the flexibility to meet the unique needs of each project.
In addition to its production capabilities, the Metal Roof Making Machine is also designed with ease of use in mind. Its user-friendly interface and intuitive controls make it easy for operators to quickly learn and master the machine, minimizing the need for extensive training and reducing the chances of errors in production. This allows for a seamless and efficient manufacturing process, further reducing costs and increasing productivity.
The company behind the Metal Roof Making Machine has a long-standing reputation for excellence in the industry. With a commitment to quality and innovation, they have been at the forefront of developing cutting-edge solutions for the roofing industry. Their team of experts and engineers have worked tirelessly to design and manufacture a machine that not only meets the needs of the industry but exceeds expectations.
With a focus on customer satisfaction, the company provides comprehensive support and training for their machines, ensuring that their clients are equipped with the knowledge and resources they need to succeed. This dedication to service and support has earned them the trust and loyalty of countless roofing contractors and manufacturers around the world.
The Metal Roof Making Machine is already making waves in the industry, with many contractors and manufacturers adopting this new technology to improve their production processes. The machine has been praised for its speed, efficiency, and quality, and is quickly becoming a staple in the toolset of roofing professionals.
As the roofing industry continues to evolve, the Metal Roof Making Machine is leading the way in transforming the way roofs are made. With its advanced technology, ease of use, and commitment to quality, this machine is sure to have a lasting impact on the industry for years to come. Its ability to streamline production, improve quality, and reduce costs is a testament to the innovation and dedication of the company behind it.
In conclusion, the Metal Roof Making Machine is a game-changer for the roofing industry. Its advanced technology, ease of use, and commitment to quality are setting a new standard for metal roofing production. With the support and expertise of the company behind it, contractors and manufacturers can now take their production processes to new heights. This revolutionary machine is paving the way for the future of roofing, and it's clear that the industry will never be the same.
Company News & Blog
Roll Former for Drip Edge Production: A Complete Guide
In the competitive world of construction and roofing, precision and efficiency are paramount. That's why the introduction of the Drip Edge Roll Former by [Company Name] has been creating a significant buzz in the industry. With its advanced technology and innovative design, this roll former is set to revolutionize the way drip edges are produced for roofing projects.Firstly, let's take a closer look at [Company Name]. With over 20 years of experience in the field of roll forming machinery, [Company Name] has established itself as a trusted and reliable provider of high-quality equipment for the construction and roofing industry. The company's commitment to innovation and customer satisfaction has driven it to develop cutting-edge solutions for various challenges faced by contractors and builders.The Drip Edge Roll Former is a prime example of [Company Name]'s dedication to delivering top-of-the-line equipment that meets the evolving needs of the industry. This roll former is designed to streamline the production process of drip edges, which are an essential component of roofing systems as they effectively direct water away from the structure, preventing potential water damage.So, what sets the Drip Edge Roll Former apart from traditional methods of producing drip edges? The answer lies in its state-of-the-art features and capabilities. This roll former is equipped with precision-driven rollers that can efficiently shape metal strips into uniform and high-quality drip edges. By utilizing this advanced machinery, contractors and manufacturers can produce drip edges with consistent dimensions and flawless finishes, ensuring the utmost reliability and durability for roofing projects.Furthermore, the Drip Edge Roll Former boasts an intuitive control system that allows for easy customization of drip edge specifications, such as width, length, and thickness. This level of flexibility enables users to cater to the specific requirements of their projects, whether it's a small-scale residential roofing job or a large commercial construction endeavor. The ability to tailor drip edges to exact specifications is a game-changer for the industry, as it enhances productivity and reduces material waste.In addition to its precision and customization capabilities, the Drip Edge Roll Former is engineered for speed and efficiency. It can produce a high volume of drip edges in a relatively short amount of time, making it ideal for meeting tight project deadlines and demand. The seamless operation of this roll former allows for continuous production without compromising on quality, ultimately optimizing production processes and boosting overall project efficiency.The impact of the Drip Edge Roll Former extends beyond its technical prowess – it also signifies [Company Name]'s commitment to sustainability and cost-effectiveness. By streamlining the production of drip edges, this roll former minimizes material waste and energy consumption, aligning with the industry's push for eco-friendly practices. Moreover, the efficiency and consistency of drip edge production contribute to cost savings for contractors and manufacturers, making it a financially sound investment for businesses of all sizes.As the construction and roofing industry continues to evolve, the introduction of the Drip Edge Roll Former by [Company Name] marks a significant milestone in advancing the production of essential roofing components. Its cutting-edge technology, precision engineering, and cost-effective benefits position it as a valuable asset for those seeking to elevate their operations and deliver superior results.In conclusion, the Drip Edge Roll Former stands as a testament to [Company Name]'s unwavering dedication to innovation and excellence. With its game-changing capabilities, this roll former is set to redefine the standards of drip edge production and set a new benchmark for efficiency and quality in the roofing industry.With the Drip Edge Roll Former, [Company Name] continues to solidify its position as a leader in providing advanced solutions that empower businesses to thrive in the competitive construction and roofing landscape. As the industry embraces the next generation of technology, the Drip Edge Roll Former is poised to make a lasting impact on how drip edges are manufactured and utilized, driving progress and success for those who harness its potential.
Professional Guide to Using a Roller for Painting Corrugated Roofing
Roller For Painting Corrugated Roof, a leading supplier of industrial painting equipment, has recently introduced a new and improved roller for painting corrugated roofs. This innovative product is designed to make the process of painting corrugated roofs faster, more efficient, and more cost-effective.Corrugated metal roofs are commonly used in industrial and commercial buildings, as well as in agricultural and residential applications. These roofs are durable and long-lasting, but they do require regular maintenance, including periodic painting to protect them from corrosion and weather damage.Traditional methods of painting corrugated roofs can be time-consuming and labor-intensive, often requiring the use of brushes or sprayers. Roller For Painting Corrugated Roof's new product aims to simplify the process by providing a specialized roller that is designed to fit the unique shape and profile of corrugated metal roofing.The new roller features a durable and lightweight design, making it easy to handle and maneuver on the uneven surface of a corrugated roof. The roller also has a specially designed nap that is ideal for applying paint evenly and smoothly to the ridges and grooves of the metal panels.In addition to its practical design, the roller is also compatible with a wide range of paints and coatings, including acrylics, enamels, and elastomerics, making it a versatile tool for a variety of painting projects."We are excited to introduce this new roller for painting corrugated roofs," said a spokesperson for Roller For Painting Corrugated Roof. "We believe that this product will make a significant impact on the industry by providing a more efficient and cost-effective solution for maintaining and preserving corrugated metal roofs."In addition to the new roller, Roller For Painting Corrugated Roof offers a comprehensive range of industrial painting equipment, including airless sprayers, pressure washers, and surface preparation tools. The company also provides expert technical support and training for customers looking to improve their painting processes and techniques.With a focus on innovation and customer satisfaction, Roller For Painting Corrugated Roof is committed to providing high-quality products and services to its clients. The company prides itself on its dedication to research and development, continuously striving to develop new and improved solutions for the painting industry.Roller For Painting Corrugated Roof has a strong reputation for reliability and expertise, with a team of experienced professionals who are passionate about delivering exceptional results for their customers. The company works closely with clients to understand their specific needs and requirements, offering tailored solutions to help them achieve their painting goals efficiently and effectively.As the demand for high-quality painting equipment continues to grow, Roller For Painting Corrugated Roof remains at the forefront of the industry, constantly seeking new opportunities to innovate and improve. The introduction of the new roller for painting corrugated roofs is just one example of the company's ongoing commitment to excellence and customer satisfaction.In conclusion, Roller For Painting Corrugated Roof's new roller for painting corrugated roofs is set to revolutionize the process of maintaining and preserving corrugated metal roofs. With its practical design, versatility, and compatibility with a wide range of paints and coatings, this innovative product is poised to make a significant impact on the industry, providing a more efficient and cost-effective solution for painting corrugated roofs.ROLLER FOR PAINTING CORRUGATED ROOFOverall, Roller For Painting Corrugated Roof's dedication to innovation and customer satisfaction makes it a trusted and reliable partner for companies and individuals looking to achieve exceptional results in their painting projects. With a strong focus on research and development, the company is well-positioned to continue leading the way in the industrial painting equipment industry for years to come.
High-Quality Metal Stud Roll Formers: Enhance Efficiency in Stud Construction
Title: Revolutionary Metal Stud Roll Former Offers Unmatched Efficiency and VersatilityIntroduction:In the ever-evolving construction industry, the demand for innovative machinery and solutions has reached new heights. One such ground-breaking addition is the Metal Stud Roll Former, a cutting-edge machine that promises a paradigm shift in efficiency and versatility. Developed by a leading manufacturer in the industry, this industry-transforming solution aims to streamline the process of metal stud production, ensuring faster turnaround times and higher quality output.Unmatched Efficiency:Traditionally, the production of metal studs has relied heavily on manual labor and outdated machinery, resulting in a slow and labor-intensive process. With the introduction of the Metal Stud Roll Former, manufacturers can now experience unparalleled efficiency. This revolutionary machine automates the stud production process, reducing human error, and significantly increasing the speed of manufacturing.Equipped with advanced technology, the Metal Stud Roll Former boasts an impressive production rate of [insert production per hour], enabling manufacturers to meet tight project deadlines without compromising quality. By eliminating the need for manual labor, this machinery also minimizes the risk of workplace injuries and fatigue, promoting a safer working environment.Versatility Redefined:The Metal Stud Roll Former stands out from its predecessors due to its exceptional versatility. Unlike traditional roll formers, which limit manufacturers to specific stud dimensions, this technologically advanced machine accommodates an extensive range of stud sizes, shapes, and profiles. From standard C and U profiles to custom designs, the Metal Stud Roll Former offers limitless possibilities, making it an ideal choice for diverse construction projects.The machine's adjustable settings empower manufacturers to effortlessly switch between different stud dimensions, eliminating the need for multiple production lines and reducing production costs significantly. Moreover, the Metal Stud Roll Former adapts to various metal gauges, accommodating the ever-expanding range of material preferences in the industry.Precision and Quality Control:The Metal Stud Roll Former incorporates state-of-the-art sensors and precision mechanisms that ensure impeccable accuracy and consistent quality. These sensors detect and correct any irregularities throughout the production process, resulting in studs that meet the highest industry standards. Manufacturers can rely on this machinery to deliver flawless, dimensionally accurate studs that are ready for assembly, minimizing delays and rework.Ease of Operation and Maintenance:To enhance user experience, the Metal Stud Roll Former is designed with user-friendly controls and intuitive interfaces. Operators can quickly learn to operate the machine, reducing training time and improving overall productivity. Additionally, the machine's low maintenance requirements result in reduced downtime and increased profitability for manufacturers.Contribution to Sustainability:In an era where environmental sustainability is a significant concern, the Metal Stud Roll Former stands out as an environmentally responsible solution. By minimizing material waste through precise measurements and efficient manufacturing processes, this machinery significantly reduces the carbon footprint associated with stud production. Manufacturers can take pride in utilizing this innovative technology, playing their part in the sustainable growth of the construction industry.Conclusion:The Metal Stud Roll Former introduces a new era of efficiency, versatility, and precision to the construction industry. Its ability to enhance production rates, facilitate custom designs, and ensure consistent quality makes it an indispensable asset for metal stud manufacturers. By adopting this revolutionary machine, manufacturers can unlock new levels of productivity while keeping pace with the ever-changing demands of the construction market. As the industry continues to evolve, the Metal Stud Roll Former sets the benchmark for cutting-edge technology and marks a significant milestone in improving construction productivity.
Revolutionizing Roofing: The Benefits of a Horizontal Roof Panel Forming Machine
Horizontal Roof Panel Forming Machine Revolutionizes Construction IndustryIn recent years, the construction industry has experienced a significant shift towards innovative technologies that increase efficiency and reduce labor costs. One technology that has been gaining popularity amongst builders is the Horizontal Roof Panel Forming Machine. This state-of-the-art machine has revolutionized the way we build roofs, making the process faster, easier, and more cost-effective.The Horizontal Roof Panel Forming Machine is a machine that is designed to create roof panels. It is based on a roll-forming principle, which involves a continuous bending process of a long strip of metal. The machine works by feeding a metal strip through a series of rollers that form the metal into the desired shape. The result is a panel that fits seamlessly into the roof structure, creating a strong and durable roof that is built to last.One of the key benefits of the Horizontal Roof Panel Forming Machine is its speed and accuracy. Traditional roof panel manufacturing methods involve a lot of manual labor and are often time-consuming. With this machine, roof panels can be produced quickly and efficiently. This means that builders can complete projects faster, which is a significant advantage in the competitive construction industry.Another important benefit of the machine is that it produces high-quality panels. This is due to the precision and consistency of the roll-forming process. Unlike traditional manufacturing methods, the Horizontal Roof Panel Forming Machine can produce panels with a high level of accuracy and consistency. This means that each panel fits perfectly into the roof structure, reducing the risk of leaks and other structural issues.Moreover, the machine has an ergonomic design that makes it operator-friendly. Its compact and lightweight frame means that it can be easily moved around the worksite, making it versatile and perfect for use in remote construction sites. The machine also comes with easy-to-use controls, making it easy for operators of all skill levels to use.The Horizontal Roof Panel Forming Machine is the brainchild of a leading construction technology company, which remains at the forefront of innovation in the industry. The company, whose name has been removed for privacy purposes, has a proven track record of developing cutting-edge technologies that have been highly successful in the market.The company prides itself on creating solutions that meet the specific needs of contractors and builders. They have a team of engineers who work tirelessly to design and develop new technologies that can revolutionize the construction industry. Their products are known for their durability, efficiency, and ease of use.With the Horizontal Roof Panel Forming Machine, the company has once again demonstrated its commitment to innovation and excellence. The machine has already been adopted by numerous contractors and builders, who have reported significant improvements in their workflow and overall project efficiency.The machine's success is a testament to the benefits of using technology to improve the construction industry. As more builders and contractors discover the advantages of using the Horizontal Roof Panel Forming Machine, it is clear that the machine is set to become an indispensable tool in the industry.In conclusion, the Horizontal Roof Panel Forming Machine is a game-changer for the construction industry. Its capabilities in producing high-quality panels quickly have made it very popular among builders and contractors. With its compact design and ease of use, the machine is perfect for use in remote construction sites and is set to become an indispensable tool in the industry. The company behind it deserves credit for developing such an innovative and useful technology.
China Offers Comprehensive Roll Forming Solution for Diverse Applications
, Roll Forming Machine, Cold Roll Forming, China Roll Forming, One-Stop Solution, Consultation, Training, Applications.Roll forming is a common metal forming process used to shape metal into a specific profile or shape. It is achieved through a series of roll forming machines that progressively shape the metal until it reaches the desired shape. This process is commonly used in the production of metal building components, automotive parts, and consumer products.China is a major player in roll forming technology, with many domestic manufacturers providing roll forming machines and solutions. One of the leading manufacturers in China is MTC, which has built a reputation for providing high-quality roll forming machines and a one-stop solution for a range of applications.The MTC roll forming machine is a cold roll former, which means that it operates at room temperature. This is in contrast to hot roll forming, which requires the metal to be preheated before forming. The advantage of cold roll forming is that it can be used on a wider range of materials, including aluminum, steel, and other metals.MTC provides a comprehensive range of roll forming machines, including panel roll forming machines, roof panel machines, wall panel machines, and more. Each machine is tailored to the specific needs of the application, ensuring optimal performance and quality.One of the unique features of MTC is its one-stop solution for roll forming applications. This includes consultation, design, manufacturing, installation, and training. The MTC team works closely with clients to understand their needs and requirements, and then provides a tailored solution that meets those needs.The consultation phase is critical in determining the most appropriate roll forming machine for the specific application. MTC’s team of experts analyze factors such as the material being used, desired throughput, and other factors to recommend the best machine for the job.Once the design has been completed, MTC manufactures the roll forming machine to the highest standards. The company uses state-of-the-art equipment and processes to ensure maximum performance and reliability.Installation is carried out by MTC’s team of trained technicians, who work closely with the client to ensure that the machine is correctly installed and fully operational.Training is also a critical component of the MTC one-stop solution. The company provides comprehensive training to clients, ensuring that they are fully versed in the operation and maintenance of the roll forming machine. This ensures that clients are able to operate the machine to its full potential, and that any maintenance or repair needs are quickly identified and addressed.MTC’s one-stop solution has been successfully implemented across a range of applications, including building construction, automotive manufacturing, and consumer goods production. The company’s expertise and commitment to quality have made it a trusted partner for businesses around the world.In summary, MTC provides a one-stop solution for roll forming applications, including consultation, design, manufacturing, installation, and training. The company's cold roll forming machines are designed to deliver the highest levels of performance and reliability, and its team of experts works closely with clients to ensure that their specific needs are met. With a focus on quality and customer service, MTC is a trusted partner for businesses seeking roll forming solutions.
High-Quality Metal Roll Forming Machine Available for Purchase – Roof Panel Roll Forming Machine Supplier
Machine, Roll Forming Machine, Roof Panel Roll Forming Machine, Metal Roll Forming, Forming Machine, Metal Roll, Metal Roll Forming Machine for Sale, Buy Metal Roll Forming Machine, Metal Roll Forming Machine Wholesaler, Metal Roll Forming Machine Seller, Top-quality Metal Roll Forming Machine, Benefits of Using Metal Roll Forming Machine, Roll Forming Process, Metal Roll Forming vs Other Forming Techniques, Applications of Metal Roll Forming Machine, Factors to Consider when Buying Metal Roll Forming Machine.Title: Advancing Manufacturing with Metal Roll Forming MachineIntroduction:In the ever-evolving manufacturing industry, metal roll forming machines have become an essential tool for efficiently producing high-quality metal components. This blog will explore the benefits of using metal roll forming machines, discuss the roll forming process, compare metal roll forming with other forming techniques, highlight the applications of metal roll forming machines, and provide insights on factors to consider when purchasing these machines.Benefit 1: Top-quality Metal ComponentsMetal roll forming machines offer superior precision and accuracy in producing metal components. The continuous bending process ensures consistent dimensions, smooth edges, and precise shapes across multiple pieces, resulting in high-quality finished products. Additionally, the ability to control forming speeds and pressures allows for the production of complex and intricate designs, meeting various industry specifications.Benefit 2: Cost-effective ProductionMetal roll forming machines facilitate cost-effective production due to their ability to handle high volumes of material with minimal wastage. By using coil stock material, roll forming eliminates the need for traditional sheet metal blanks, reducing material costs and minimizing scrap. Furthermore, the continuous operation of roll formers decreases labor requirements and enhances production efficiency, ultimately reducing overall manufacturing costs.Benefit 3: Versatile ApplicationsMetal roll forming machines find applications in various industries, including automotive, construction, aerospace, and furniture. These machines offer versatility in creating a wide range of metal profiles, such as roof panels, wall cladding, gutters, window frames, and door frames. The flexibility in material thickness, width, and length allows manufacturers to cater to diverse customer requirements and adapt to market trends effectively.Roll Forming Process:The roll forming process involves feeding coil stock material into a series of contoured rolls, gradually bending and shaping the metal. As the material moves through multiple stations, the rolls progressively form the desired profile. Each station performs a specific shaping operation, such as punching, notching, embossing, or cutting. By adjusting the roll spacing, manufacturers can achieve precise dimensions and shapes. The formed metal components are then cut to the desired length using a flying shear or cut-off press.Metal Roll Forming vs Other Forming Techniques:Compared to other forming techniques like stamping and press braking, metal roll forming offers several advantages. First, roll forming allows for continuous production with minimal interruptions, reducing operational downtime. Second, roll forming eliminates the need for pre-formed blanks or separate operations for joining multiple pieces, resulting in faster production cycles. Finally, roll-formed components exhibit improved structural integrity due to the continuous grain flow, enhancing their strength and durability.Applications of Metal Roll Forming Machines:1. Automotive Industry: Metal roll forming machines are widely used in manufacturing automotive body components, including chassis, roof rails, door frames, and window frames. The ability to produce complex profiles and maintain tight tolerances makes roll forming an ideal choice for this industry.2. Construction Industry: Roll-formed profiles for roofing panels, wall cladding, and structural components are in high demand in the construction sector. The cost-effectiveness and precision of metal roll forming machines make them indispensable for producing these architectural elements.3. Furniture Industry: Roll forming technology is employed in the production of metal furniture components like frame elements, brackets, and decorative fittings. The versatility and high-quality output of metal roll forming machines contribute to the aesthetic appeal and functionality of modern furniture designs.Factors to Consider when Buying Metal Roll Forming Machines:1. Machine Size and Capacity: Consider the required profile dimensions, thickness, and material type to ensure compatibility with the selected machine's specifications.2. Material Handling and Coil Weight: Evaluate the machine's ability to handle heavy coil stock material and ensure that it suits your production requirements.3. Tooling Flexibility: Check if the machine allows for easy changeovers between different profiles and if additional tooling options are available to expand its capabilities.4. Automation and Integration: Decide if integrating automation features, like computer numerical control (CNC) systems, is necessary to enhance production efficiency and reduce human error.5. After-sales Support: Research the reputation of the manufacturer and evaluate the availability of technical support, spare parts, and maintenance services.Conclusion:Metal roll forming machines offer numerous benefits, including top-quality production, cost-effectiveness, and versatility. The roll forming process, with its continuous bending and shaping, ensures consistent dimensions and smooth edges. Metal roll forming outperforms other forming techniques in terms of efficiency, structural integrity, and faster production cycles. These machines find applications in diverse industries like automotive, construction, and furniture manufacturing. When purchasing a metal roll forming machine, considering factors such as machine size, capacity, tooling flexibility, and after-sales support will help manufacturers make informed decisions and achieve optimal results in their production processes.
Automatic Reinforcement Iron Bar Making Machine: Everything You Need to Know
Ibr Making Machine: Revolutionizing the Roofing IndustryIn the world of construction and roofing, innovation and technology play a vital role in improving efficiency and quality of work. One such innovation that has recently been making waves in the industry is the Ibr Making Machine. This state-of-the-art machine is changing the way roofing materials are manufactured and is set to revolutionize the roofing industry as we know it.The Ibr Making Machine, produced by a leading manufacturing company in the field of construction machinery, is a fully automated, high-speed machine that is capable of producing a wide range of roofing materials with precision and efficiency. From galvanized steel to aluminum, the machine can effortlessly handle various materials, ensuring versatility and high quality in the final products.One of the key features of this machine is its ability to produce IBR (Inverted Box Rib) profiles, a popular choice for roofing material due to its strength and durability. The machine's precision rollers and cutting mechanisms ensure that each sheet produced is of consistent quality and precise dimensions, meeting the highest standards in the industry. This consistency is crucial for roofing projects, as it ensures a seamless and watertight installation, ultimately leading to greater customer satisfaction and long-lasting roofs.Furthermore, the Ibr Making Machine is equipped with advanced technology that allows for seamless customization of roofing materials. This means that contractors and builders can easily adjust the dimensions, thickness, and even colors of the roofing sheets to suit the specific requirements of each project. This level of customization not only provides flexibility but also reduces material waste, ultimately leading to cost savings for the roofing companies and their clients.The company behind the Ibr Making Machine prides itself on its commitment to innovation and quality. With a team of experienced engineers and technicians, the company has dedicated extensive resources to research and development, ensuring that their machines are at the forefront of technological advancements in the industry. In addition, the company places great emphasis on customer service and support, ensuring that their clients are well-trained and supported in the operation and maintenance of the machines.The impact of the Ibr Making Machine on the roofing industry has been profound. Many roofing companies that have adopted this technology have reported significant improvements in their production processes, from faster turnaround times to higher quality products. The machine's efficiency has also allowed these companies to take on larger and more complex projects, expanding their business and ultimately improving their bottom line.Moreover, the Ibr Making Machine has had a positive environmental impact as well. By reducing material waste and energy consumption, the machine contributes to sustainable and eco-friendly manufacturing practices, aligning with the global push for greener and more sustainable construction methods.As the demand for high-quality roofing materials continues to grow, the Ibr Making Machine is poised to become an indispensable asset for roofing companies around the world. Its ability to produce top-notch roofing materials with speed, efficiency, and customization capabilities make it a game-changer in the industry. With the backing of a reputable and innovative manufacturing company, the Ibr Making Machine is set to shape the future of roofing, providing solutions that meet the evolving needs of the construction industry.
High-Quality Glazed Tile Roll Forming Machine for Metal Roofing Production
Are you in need of a high-quality glazed tile roll forming machine for your metal roofing production? Look no further than the Color Steel Glazed Metal Tile Roll Forming Machine from Dahezb.Designed for producing metal roof tiles in thicknesses ranging from 0.3-0.6mm, this machine specializes in creating aluminum roofing step tile and glazed tiles for roofing sheets. Using advanced automatic technology, it ensures fast and efficient production with consistent results, making it the perfect choice for industrial settings.One of the key advantages of the Color Steel Glazed Metal Tile Roll Forming Machine is its versatility. It can be used with a wide range of raw materials, including color steel, galvanized steel, and aluminum, giving you greater flexibility in your production processes. Additionally, it boasts a high level of precision, thanks to its advanced integrated control system that ensures every tile is made to exacting standards.Another benefit of this glazed tile roll forming machine is its ease of use. With a simple and easy-to-follow interface, it can be operated by personnel with minimal training, reducing the learning curve and saving you time and money. Its compact design also makes it ideal for smaller facilities, and it can be easily transported between locations.Finally, the Color Steel Glazed Metal Tile Roll Forming Machine is built to last. It is constructed from durable materials that can withstand heavy use, and its high-quality components ensure that it requires minimal maintenance over its lifetime. This translates to a lower total cost of ownership and a higher return on investment for your business.In conclusion, if you're looking for a reliable, efficient, and user-friendly glazed tile roll forming machine for your metal roofing production, the Color Steel Glazed Metal Tile Roll Forming Machine from Dahezb is an excellent choice. With its advanced technology, precision, versatility, and durability, it will help you take your business to the next level and meet even the most demanding production requirements.
Efficient Automatic Roll Slitter: A Game-Changer in Manufacturing
Automatic roll slitter has become a significant part of the manufacturing process for many industries. It offers precision cutting and slitting of various materials, making it an essential tool for businesses looking to improve their production efficiency. [Company] is one of the leading providers of automatic roll slitter solutions, catering to the diverse needs of its clients in different industries.The automatic roll slitter offered by [Company] is designed to meet the high standards of precision and reliability required in modern manufacturing environments. With advanced technology and innovative features, the automatic roll slitter ensures accurate and consistent cutting of materials, including paper, film, fabric, and other flexible substrates. This level of precision is essential for achieving the desired quality and performance in the final products.One of the key benefits of the automatic roll slitter from [Company] is its versatility. It can handle a wide range of roll widths and thicknesses, making it suitable for various applications. Whether it's converting large rolls into smaller ones or creating custom-sized rolls for specific production requirements, the automatic roll slitter offers the flexibility needed to accommodate different manufacturing needs.In addition to its cutting capabilities, the automatic roll slitter also includes features for automated roll handling and positioning. This streamlines the process of loading and unloading rolls, minimizing downtime and maximizing productivity. Furthermore, the intuitive control system allows operators to set precise cutting parameters and monitor the slitting process, ensuring consistent results with minimal intervention.Another standout feature of the automatic roll slitter from [Company] is its user-friendly design. The machine is engineered for easy operation and maintenance, reducing the learning curve for operators and the overall cost of ownership for businesses. This simplicity, coupled with its robust construction, ensures long-term reliability and performance, delivering a high return on investment for customers.With a commitment to quality and customer satisfaction, [Company] provides comprehensive support for its automatic roll slitter solutions. From installation and training to ongoing technical assistance, the company's team of experts is dedicated to helping clients optimize the performance of their equipment and achieve their production goals. This level of support underscores [Company]'s reputation as a trusted partner for manufacturers seeking reliable and efficient roll slitting solutions.The automatic roll slitter from [Company] has garnered positive feedback from clients across various industries. The machine's combination of precision, versatility, and user-friendly operation has significantly improved their manufacturing processes, leading to increased efficiency and quality in their end products. For businesses looking to stay competitive in today's fast-paced market, the automatic roll slitter has proven to be a valuable asset for driving success and growth.[Company] continues to innovate and enhance its automatic roll slitter solutions, leveraging the latest technologies and industry best practices. As the manufacturing landscape evolves, the company remains at the forefront, delivering cutting-edge solutions that empower its clients to achieve their production objectives with confidence and ease.In conclusion, the automatic roll slitter from [Company] is a game-changer for manufacturers seeking to elevate their production capabilities. With its precision cutting, versatility, and user-friendly design, the machine offers a competitive edge in today's dynamic market. As [Company] continues to set the standard for roll slitting solutions, businesses can rely on its expertise and commitment to driving their success.
Enhance Efficiency with Cutting-Edge Floor Deck Roll Forming Machines
Title: Streamlining Construction with the Double Deck Roll Forming MachineIntroduction (100 words):In today's rapidly evolving construction industry, it is crucial to stay updated with the latest technology and equipment that can enhance project efficiency and productivity. One such impressive innovation is the Double Deck Roll Forming Machine. This cutting-edge machinery has revolutionized the way steel floor decks are produced, providing a cost-effective and seamless solution for construction projects. In this blog post, we will explore the key features and benefits of the Double Deck Roll Forming Machine, while also highlighting its role in enabling swift and precise construction processes. 1. Advantages of the Double Deck Roll Forming Machine (200 words):The Double Deck Roll Forming Machine offers numerous advantages that make it a highly sought-after tool in the construction industry. With its advanced capabilities, this machinery streamlines the production of steel floor decks, reducing manual labor and minimizing human error. Some key advantages of the Double Deck Roll Forming Machine include:a) Enhanced Efficiency: By automating the roll forming process, the Double Deck Roll Forming Machine significantly speeds up production, resulting in shorter lead times and improved project timelines.b) Precision and Consistency: This machine ensures precise and uniform shaping of steel floor decks, eliminating variations in dimensions commonly found in manual production methods. The outcome is a consistent and high-quality end product that meets industry standards.c) Cost-effective Solution: The automated nature of the Double Deck Roll Forming Machine reduces the need for additional workers, thereby lowering labor costs. Furthermore, by minimizing production errors, wastage is reduced, leading to cost savings.2. Key Features of the Double Deck Roll Forming Machine (300 words):The Double Deck Roll Forming Machine boasts several key features that have attributed to its rise in popularity among construction professionals worldwide. Here are some notable features:a) Dual-Level Decking: As its name suggests, this machine has the ability to create two different levels of deck sheets simultaneously, maximizing productivity and reducing production time. This efficient process eliminates the need for separate runs for different profiles or heights.b) Customizable Profiles: The Double Deck Roll Forming Machine allows for the creation of various profiles and sizes of steel floor decks. With adjustable settings and versatile tooling options, it caters to the specific requirements of each construction project.c) High-speed Production: Equipped with an advanced control system, the machine ensures that the roll forming process is efficient and swift, delivering high-speed production capabilities without compromising on quality.d) User-friendly Design: The Double Deck Roll Forming Machine is designed for ease of use, with intuitive controls and a straightforward setup process. Its user-friendly interface reduces the learning curve for workers, allowing for seamless integration into construction sites.3. Integration of the Double Deck Roll Forming Machine in Construction (300 words):The integration of the Double Deck Roll Forming Machine brings about several positive developments in the construction process, positively impacting both small-scale and large-scale projects. a) Project Acceleration: By automating the production of steel floor decks, project timelines are significantly reduced. The efficient production process enabled by the Double Deck Roll Forming Machine ensures that construction projects progress swiftly, allowing for earlier completion and increased overall efficiency.b) Enhanced Structural Integrity: The consistent and precise shaping of steel floor decks produced by the machine ensures the structural integrity of the building. The high-quality end product meets industry standards, thus contributing to the safety and durability of the construction.c) Cost Savings: The Double Deck Roll Forming Machine considerably reduces labor costs by eliminating the need for excessive manual labor. Additionally, the minimized errors and wastage result in cost savings, making the machine a highly cost-effective solution for construction projects.Conclusion (100 words):In conclusion, the Double Deck Roll Forming Machine is an innovative asset that has transformed the production of steel floor decks in the construction industry. Its ability to seamlessly manufacture precise and high-quality components, along with its cost-effectiveness and efficient automation, make this machinery a game-changer in optimizing construction processes. As the industry evolves and demands quicker turnaround times, the Double Deck Roll Forming Machine offers the perfect solution, providing construction professionals with a competitive edge and enhancing the overall efficiency and quality of their projects.