How to Build a Sheet Metal Barn in 6 Simple Steps
By:Admin
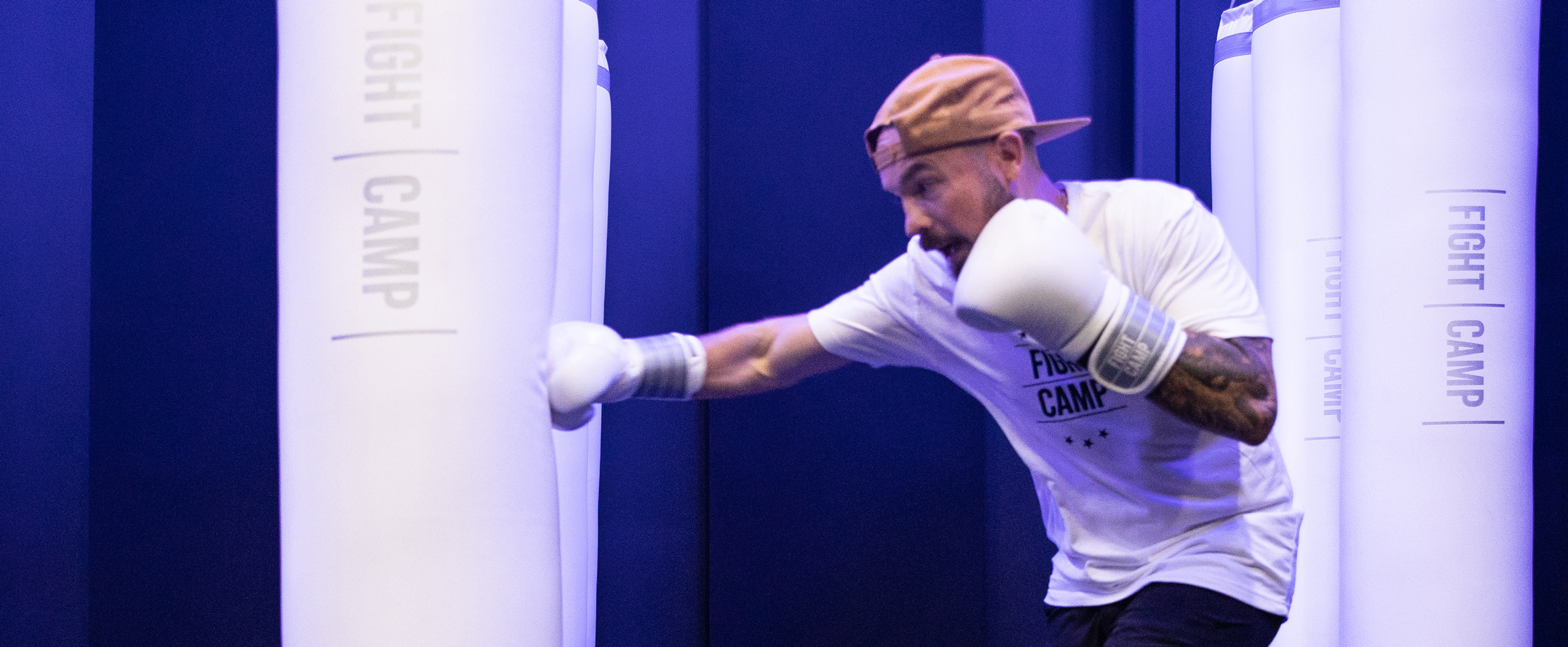
Introduction:
Sheet metal barns provide an excellent solution for storage and shelter needs. Not only are they durable and cost-effective, but they can also be constructed relatively easily. In this article, we will outline a step-by-step guide on how to build a sheet metal barn in six simple steps. Whether you have experience in construction or are a DIY enthusiast, this guide will help you create your very own sheet metal barn.
Step 1: Planning and Preparation
Before starting any project, careful planning is essential. Determine the size and design of your barn based on your requirements. Take measurements of the desired area and sketch out the barn's layout. Consult local building codes and acquire any necessary permits. Once you have a clear plan, gather the required materials.
Step 2: Foundation and Frame Construction
Create a solid foundation for your sheet metal barn. Excavate the area, level the ground, and lay a sturdy foundation using concrete or treated wood. Next, construct the frame using the plywood pallets. Cut them to the desired size and connect them securely using screws and nuts, ensuring stability and durability.
Step 3: Installing Roofing
Select the appropriate sheet metal for the roofing of your barn. Galvanized sheet metal provides excellent protection against rust and corrosion. Measure and cut the sheet metal to fit the roof frame, leaving a slight overhang for drainage. Secure the roofing sheets to the frame using screws or nails, ensuring proper alignment and sealing.
Step 4: Wall Construction
Measure and cut additional plywood panels to serve as walls for your sheet metal barn. Attach them securely to the frame, leaving space for doors and windows as needed. Ensure tight joints and smooth surfaces for a professional finish.
Step 5: Doors and Windows
Install suitable doors and windows into the wall structure. Depending on your requirements, you can choose ready-made options or customize your own. Ensure proper insulation and weatherproofing to protect your belongings from the elements.
Step 6: Finishing Touches
Take time to inspect your sheet metal barn for any loose screws or nails. Replace or tighten them as necessary. Consider adding ventilation systems, gutters, or additional storage options such as shelves or hooks. Apply a protective finish, such as paint or weather-resistant coatings, to increase the longevity and aesthetics of your barn.
Conclusion:
Building a sheet metal barn is a satisfying project that offers both functionality and durability. By following these six easy steps, you can construct your own barn and enjoy the benefits of efficient storage and shelter. Whether you are a DIY enthusiast or a seasoned builder, creating a sheet metal barn can be achieved with the right materials, tools, and patience. Embrace your creativity and get started on your own sheet metal barn project today!
Company News & Blog
High-Strength Multi-Heads Rotary Woodworking CNC Machine for Efficient Wood Processing
Title: Multi-Head Rotary Woodworking CNC Machine: Advancing Efficiency in Residential and Commercial Woodwork ProjectsIntroductionIn the world of woodworking, the demand for precision and efficiency is paramount. With advancements in technology, the introduction of Multi-Head Rotary Woodworking CNC Machines has revolutionized the industry. HBHongchen.com proudly presents a woodworking CNC router that is designed to meet the diverse needs of both residential and commercial projects, offering a range of advantages that make it an essential tool for anyone involved in the woodworking field.High-Strength Design and Enhanced SpeedOne of the key advantages of the woodworking CNC router is its high-strength body design. Equipped with double driving motors on the Y-axis, the machine operates with more remarkable precision and efficiency than ever before. The more reasonable and advanced design ensures fast processing speeds, reducing project completion times significantly. This improved speed is a boon for both large-scale commercial projects and intricate residential woodworking endeavors.Easy Operation and Low MaintenanceThe woodworking CNC router prides itself on its user-friendly interface, making it easily operable even by novices in the woodworking field. The machine's design incorporates simplicity, allowing operators to quickly grasp its functionalities and navigate through its various features effortlessly. Additionally, the easy-operated maintenance feature allows users to perform routine checks and troubleshoot efficiently, minimizing downtime and optimizing productivity.Reduced Fault Rate for Increased ReliabilityWoodworking projects can often be time-consuming, and any unanticipated faults in the machinery can result in costly delays. However, the woodworking CNC router boasts an exceptionally low fault rate, ensuring reliability throughout the production process. This unwavering performance provides peace of mind for both individual craftsmen and commercial manufacturers, allowing them to focus on their core woodworking tasks without unnecessary interruptions.Premium Drivers and MotorsA key component of the woodworking CNC router's efficiency lies in the integration of famous brand drivers and motors. It is important to note that specific brand names have been omitted for this content. However, the woodworking CNC machine incorporates renowned components that meet and exceed industry standards. These premium drivers and motors ensure smooth and precise operations, providing consistent results regardless of the scale or complexity of the project.Synergy with C Z Purlin Multi-Size Purlin Making MachineHBHongchen.com has also established itself as a leading provider of the C Z Purlin Multi-Size Purlin Making Machine. This innovative equipment enables the efficient production of C and Z-shaped steel purlins, commonly used in residential and commercial building construction. By combining the woodworking CNC router with the C Z Purlin Making Machine, manufacturers can seamlessly transition between woodworking and metalworking, streamlining their production processes and maximizing productivity.ConclusionThe Multi-Head Rotary Woodworking CNC Machine provided by HBHongchen.com offers a range of advantages that elevate its performance in residential and commercial woodworking projects. With its high-strength body design, fast processing speeds, easy operation, low maintenance requirements, and premium quality drivers and motors, this woodworking CNC router redefines efficiency and reliability in the woodworking industry.Furthermore, by integrating it with the C Z Purlin Multi-Size Purlin Making Machine, manufacturers can seamlessly achieve a smoother transition between woodworking and metalworking processes. For professionals in the woodworking field, investing in this state-of-the-art machinery ensures optimal performance, increased productivity, and cost-effective woodworking solutions. HBHongchen.com leaves no stone unturned in providing woodworking enthusiasts and professionals with the best tools to realize their creative visions while optimally meeting the demands of the industry.
Modern Manual Handling Solutions: Electric Lifters & Walkie Stackers for Pallet Stacking Jobs
Manual Stacker for the Shape C Purline Machine: Introducing Modern Manual Handling SolutionsIn the world of manufacturing and industrial operations, forklifts have always been the go-to solution for various material handling tasks. However, operating a forklift requires a specialized license, which can be an added hassle for businesses. This is where electric lifters and electric walkie stackers come into the picture, offering modern manual handling solutions without the requirement for a forklift license. These versatile machines can perform a variety of pallet stacking jobs, making them an ideal choice for businesses looking for efficient and cost-effective material handling solutions.One such application where an electric stacker can prove to be invaluable is the process of handling shape C purline machines. Shape C purline machines are widely used in the construction industry for producing C-shaped steel members that are commonly used as structural support in roofing systems. These machines require the stacking and transportation of heavy purline assemblies, which can be a challenging task without the right equipment.By utilizing an electric stacker with a capacity of 1 to 1.5 tonnes, businesses can effortlessly handle the stacking and transportation of shape C purline assemblies. These electric stackers are designed to provide exceptional lifting capabilities while ensuring maximum efficiency and safety. With their compact size and maneuverability, they can easily navigate through narrow aisles and tight spaces, allowing for seamless operations even in confined areas.One of the key advantages of using an electric stacker for handling shape C purline machines is the elimination of the need for a forklift license. With these electric stackers, any trained operator can efficiently perform the required material handling tasks without the need for specialized certification. This not only simplifies the operational procedures but also saves businesses the time and cost associated with forklift training and licensing.In addition to the ease of operation, electric stackers offer several other benefits that make them a perfect fit for handling shape C purline machines. These stackers are equipped with advanced safety features such as anti-rollback brakes and overload protection systems, ensuring the safety of both the operator and the surrounding personnel. Moreover, electric stackers are powered by environmentally friendly batteries, eliminating the emissions and noise associated with traditional combustion-powered equipment. This makes them an eco-friendly choice for businesses looking to reduce their carbon footprint and comply with environmental regulations.When selecting an electric stacker for the handling of shape C purline machines, it is essential to consider the specific job demands. The capacity of the stacker, ranging from 1 to 1.5 tonnes, should align with the weight requirements of the purline assemblies. Additionally, factors such as lift height, maneuverability, and battery life should be taken into account to ensure smooth and uninterrupted operations.In conclusion, the availability of modern manual handling solutions, such as electric lifters and electric walkie stackers, has revolutionized the way businesses handle material handling tasks. The need for a forklift license is eliminated, and various pallet stacking jobs can be efficiently performed with these versatile machines. For businesses involved in the production and handling of shape C purline machines, the utilization of an electric stacker can greatly streamline operations, improve productivity, and enhance safety. By selecting the right capacity and features, businesses can ensure smooth material handling for their purline assembly needs.
How to Build a Sheet Metal Barn in 6 Simple Steps
Title: How to Build a Sheet Metal Barn in 6 Easy StepsIntroduction:Sheet metal barns provide an excellent solution for storage and shelter needs. Not only are they durable and cost-effective, but they can also be constructed relatively easily. In this article, we will outline a step-by-step guide on how to build a sheet metal barn in six simple steps. Whether you have experience in construction or are a DIY enthusiast, this guide will help you create your very own sheet metal barn.Step 1: Planning and PreparationBefore starting any project, careful planning is essential. Determine the size and design of your barn based on your requirements. Take measurements of the desired area and sketch out the barn's layout. Consult local building codes and acquire any necessary permits. Once you have a clear plan, gather the required materials.Step 2: Foundation and Frame ConstructionCreate a solid foundation for your sheet metal barn. Excavate the area, level the ground, and lay a sturdy foundation using concrete or treated wood. Next, construct the frame using the plywood pallets. Cut them to the desired size and connect them securely using screws and nuts, ensuring stability and durability.Step 3: Installing RoofingSelect the appropriate sheet metal for the roofing of your barn. Galvanized sheet metal provides excellent protection against rust and corrosion. Measure and cut the sheet metal to fit the roof frame, leaving a slight overhang for drainage. Secure the roofing sheets to the frame using screws or nails, ensuring proper alignment and sealing.Step 4: Wall ConstructionMeasure and cut additional plywood panels to serve as walls for your sheet metal barn. Attach them securely to the frame, leaving space for doors and windows as needed. Ensure tight joints and smooth surfaces for a professional finish.Step 5: Doors and WindowsInstall suitable doors and windows into the wall structure. Depending on your requirements, you can choose ready-made options or customize your own. Ensure proper insulation and weatherproofing to protect your belongings from the elements.Step 6: Finishing TouchesTake time to inspect your sheet metal barn for any loose screws or nails. Replace or tighten them as necessary. Consider adding ventilation systems, gutters, or additional storage options such as shelves or hooks. Apply a protective finish, such as paint or weather-resistant coatings, to increase the longevity and aesthetics of your barn.Conclusion:Building a sheet metal barn is a satisfying project that offers both functionality and durability. By following these six easy steps, you can construct your own barn and enjoy the benefits of efficient storage and shelter. Whether you are a DIY enthusiast or a seasoned builder, creating a sheet metal barn can be achieved with the right materials, tools, and patience. Embrace your creativity and get started on your own sheet metal barn project today!
High-Quality Steel Coil Slitting Machines for Efficient Metal Sheet Cutting and Stainless Steel Strips
Stainless Steel Strip Slitting Machine: A Revolutionary Solution for Cutting and Slitting Metal SheetsWhen it comes to metalworking, precision and accuracy are critical factors in achieving quality results. One such process is slitting, which involves cutting a wide metal sheet into narrower strips to meet specific requirements. This process is necessary for industries that require smaller widths for their product manufacturing, such as automotive, electronics, and construction.To achieve this, manufacturers use a slitting machine, a unique piece of equipment that cuts and converts metal coils into narrower strips. One type of slitting machine that has gained popularity in recent years is the stainless steel strip slitting machine, which provides greater precision and efficiency in metal sheet cutting.What is a Stainless Steel Strip Slitting Machine?A stainless steel strip slitting machine is a piece of equipment specifically designed for cutting and slitting metal sheets, mainly made of stainless steel. This machine is equipped with a set of blades or knives that sever the material in smaller strips with the desired width. The blades or knives can be adjusted to achieve the desired cut and width of the strips, making it highly customizable.Uses of Stainless Steel Strip Slitting MachineStainless Steel Strip Slitting Machine is widely used in many industries that utilize metal sheets in their manufacturing processes. These include the automotive, aerospace, and construction industries. It is also useful for electronics, textile, and paper industries for creating smaller electronic components and packaging materials.Advantages of Stainless Steel Strip Slitting Machine1.Precision CuttingOne of the primary advantages of using a stainless steel strip slitting machine is its ability to produce precise cuts and meet the required specifications. The machine can cut narrow strips with the desired width and high accuracy, reducing material waste and saving production time.2. High ProductivityStainless Steel Strip Slitting Machine can work continuously, producing strips of varying widths with minimal operator intervention. This leads to increased productivity and output while ensuring consistent quality in products.3. CustomizationThe Stainless Steel Strip Slitting Machine can be customized to meet specific requirements, such as cutting thickness, strip widths, and number of pieces produced per roll.4. DurabilityAs the name suggests, the machine is made of stainless steel, making it resistant to corrosion and ensuring durability. The blades are also made of high-quality materials that can withstand the stress of cutting metal sheets for extended periods.ConclusionIn conclusion, the Stainless Steel Strip Slitting Machine is a revolutionary technology that has changed the game in metal sheet cutting and slitting. It offers high precision, customization, efficiency, and durability in metalworking, making it an excellent investment for industries that rely on metal sheets. With its versatile applications and advantages, it is no wonder why it has become popular among manufacturers. Keywords: Stainless Steel Strip Slitting Machine, Metal Sheet Cutting Machine, Steel Strip Slitting Machine.
China's Leading Manufacturer Offers Comprehensive Roll Forming Solutions for Various Applications
Roofing Sheet Forming Machine: The Ultimate Solution for Precise and Efficient RoofingWhen it comes to roofing materials, choosing the right one is crucial to ensure the durability and aesthetics of a building. Among the various options available, roofing sheets have become increasingly popular due to their versatility and cost-effectiveness. However, to efficiently produce roofing sheets that meet specific requirements, a reliable and precise manufacturing process is essential. That's where a Roofing Sheet Forming Machine comes into play.A roofing sheet forming machine is an advanced piece of equipment designed specifically for the production of roofing sheets. It is widely used across various industries, including construction, architecture, and manufacturing. The machine utilizes the process of roll forming, which is known for its accuracy and efficiency in creating uniform and high-quality products.The roll forming process involves passing a sheet of metal through a series of rollers, gradually shaping it into the desired profile. With the use of custom-made molds, the machine can produce different types of roofing sheets, such as corrugated, trapezoidal, and standing seam profiles. This flexibility allows manufacturers to cater to a wide range of customer demands and project specifications.One of the significant advantages of using a Roofing Sheet Forming Machine is its ability to ensure precision and consistency throughout the production process. Each roller in the machine is uniquely designed to shape the metal sheet with precise measurements and dimensions. This results in roofing sheets that fit perfectly and are aesthetically pleasing.Additionally, the machine's high-speed operation enables manufacturers to produce a large volume of roofing sheets quickly. This not only saves time but also enhances productivity, making it an ideal choice for mass production. Furthermore, the machine's automated control system eliminates the need for manual labor, reducing the chances of errors and ensuring a safer working environment.Quality is of utmost importance when it comes to roofing materials, and a Roofing Sheet Forming Machine excels in delivering consistent and durable products. By using high-quality materials and advanced manufacturing techniques, these machines guarantee the production of roofing sheets that are resistant to corrosion, weathering, and wear. This durability ensures that the roofs constructed using these sheets can withstand harsh environmental conditions and provide long-lasting protection.In addition to its primary function of manufacturing roofing sheets, a Roofing Sheet Forming Machine offers several other benefits. It provides versatility by offering customizability options, allowing manufacturers to produce roofing profiles of different lengths, widths, and thicknesses. This ensures that they can cater to diverse customer requirements and project specifications.Moreover, the machine's operation is accompanied by minimal noise and vibration, thanks to its advanced engineering and quality construction. This reduces disturbances in the workplace and contributes to a peaceful working environment for employees. Additionally, the machine requires minimal maintenance, leading to lower operational costs and improved overall efficiency.As the demand for roofing sheets continues to rise, it is essential to choose a reliable and experienced manufacturer when investing in a Roofing Sheet Forming Machine. A reputable manufacturer will not only provide top-quality machines but also offer comprehensive support and service throughout the purchase process. They will assist in the selection of the right machine, provide installation and training, and offer after-sales support to ensure smooth and efficient operations.In conclusion, a Roofing Sheet Forming Machine is the ultimate solution for producing precise, durable, and cost-effective roofing sheets. Its ability to deliver consistent quality, high-speed production, and customizability makes it an indispensable piece of equipment in the roofing industry. So, whether you are a contractor, builder, or manufacturer, investing in a Roofing Sheet Forming Machine is a wise choice to elevate your roofing business to new heights.
Ultimate Guide 2020: Roll Forming Process from Concept to Production
Title: Mastering the Roll Forming Process: A Comprehensive Guide to Horizontal Profiled Panel Roll FormingIntroduction: In the modern world of manufacturing, roll forming has emerged as a highly efficient and cost-effective method for shaping flat metal sheets into complex profiles. Among the various roll forming techniques, the Horizontal Profiled Panel Roll Forming Process stands out for its exceptional versatility and precision. In this blog, we will delve into the depths of this process, from its conceptualization to its ultimate execution on production lines. Join us on this ultimate guide for a detailed understanding.1. Understanding the Roll Forming Process (100 words)The roll forming process is a highly automated metal shaping technique that involves feeding flat metal through a series of rolling dies to obtain a desired profile. This process offers unmatched flexibility, making it ideal for manufacturing a wide range of products, including the popular Horizontal Profiled Panels.2. Key Components and Their Functions (200 words)a. Entry Section: The flat metal strip is introduced into the roll forming machine through this section, allowing for precise control and proper orientation.b. Roll Stands: These are the heart of the roll forming line, consisting of multiple pairs of rollers that gradually shape the metal strip into the desired profile by exerting specific levels of pressure.c. Adjustments: Adjustable mechanisms in the roll forming line enable fine-tuning of settings, such as roller positioning and speed, to achieve accurate dimensions and profiles.d. Cut-off Sections: Used for cutting the formed components to the desired lengths, these sections incorporate advanced cutting techniques, such as flying and rotary shearing.3. Unleashing the Potential: Concept to Production (300 words)a. Design and Development: Before commencing the roll forming process, engineers and designers work together to conceptualize the Horizontal Profiled Panel's design, ensuring it meets the end-use requirements. Computer-aided design (CAD) software plays a crucial role in this phase.b. Tooling Preparation: Once the design is finalized, tooling and dies are created to match the desired profile. Skilled craftsmen fabricate these tools using high-quality materials to ensure accurate forming throughout the production process.c. Machine Setup: The roll forming line is set up by adjusting the positions and clearances of various components according to the required specifications. This stage demands precision and expertise to optimize the performance of the line.d. Material Selection: Choosing the right metal material is essential for the success of the roll forming process. Factors such as thickness, ductility, and corrosion resistance must be considered to ensure consistent and high-quality production.e. Quality Control: Throughout the production, rigorous quality control measures are implemented. Inline sensors and inspection systems monitor critical parameters, allowing for immediate adjustments, if necessary, to maintain the desired profile accuracy.f. Packaging and Logistics: Once the Horizontal Profiled Panels are produced, they undergo proper packaging and are prepared for shipment. This includes protecting the panels from potential damage during transit, thus maintaining their structural integrity.g. Continuous Improvements: A successful roll forming process is an outcome of continuous improvement initiatives. Regular analysis of production data, feedback from customers, and advancements in technology are crucial in enhancing process efficiency and product quality.Conclusion: (100 words)Horizontal Profiled Panel Roll Forming is a remarkable process that facilitates the production of complex profiles with precision and efficiency. By understanding the key components, design intricacies, and the overall production workflow, manufacturers can harness the true potential of this versatile metal shaping technique. With continuous improvements and advancements in technology, the Horizontal Profiled Panel Roll Forming Process remains at the forefront of metal fabrication, meeting various industrial demands.
Glazed Tile Roll Forming Machine: A Reliable Solution for Roofing Sheet Production
Title: Introducing Dahezb's Cutting-Edge Glazed Tile Roll Forming Machine for Metal RoofingIntroduction:In the fast-paced world of construction and manufacturing, technological advancements are constantly emerging to improve efficiency and quality. Dahezb Metal presents its latest innovation, the Glazed Tile Roll Forming Machine, a state-of-the-art solution for producing metal roof tiles. With its ability to transform metal sheets into refined glazed roofing tiles, this machine proves to be a game-changer in the industry.Redefining Metal Roofing:Dahezb's Glazed Tile Roll Forming Machine is designed to cater to the specific needs of customers looking for robust metal roofing solutions. Capable of molding metal sheets ranging from 0.3mm to 0.6mm in thickness, this machine delivers top-notch precision and durability.Key Features and Benefits:1. Enhanced Efficiency: The Glazed Tile Roll Forming Machine operates with remarkable efficiency, allowing for smooth and continuous production. By eliminating the need for manual tile cutting, this machine saves time, labor, and material costs.2. Customized Solutions: Dahezb understands that every customer has unique requirements. Therefore, the Glazed Tile Roll Forming Machine offers flexibility in terms of tile shapes, sizes, and profiles. Whether it is a traditional or modern design, this machine can adapt to produce the desired glazed tiles for any roofing project.3. High-Quality Output: The Glazed Tile Roll Forming Machine ensures impeccable quality, maintaining consistency in tile thickness and dimensions. With precise control and advanced technology, it guarantees an aesthetically pleasing finish, giving metal roofing a sophisticated appeal.4. Durability: Metal roofs are known for their longevity, and the tiles produced by this machine are no exception. The Glazed Tile Roll Forming Machine manufactures tiles of exceptional strength, able to withstand harsh weather conditions and provide long-lasting protection.5. Advanced Automation: The machine's automation features streamline the production process, reducing the chances of human error. With user-friendly controls and easy-to-understand functions, operators can swiftly adapt to the machine's operations.6. Environmentally Friendly: Contributing to sustainable construction practices, the Glazed Tile Roll Forming Machine minimizes waste generated during production. By optimizing material usage and reducing scrap, it aligns with the industry's increasing focus on eco-friendly solutions.Growing Demand for Metal Roofing:The demand for metal roofing has been steadily rising due to its numerous advantages over traditional roofing materials. Metal roofs offer superior durability, remarkable energy efficiency, and significant cost savings in the long run. Additionally, they are fire-resistant and require minimal maintenance, making them an attractive choice for homeowners and businesses alike.Company Introduction: Dahezb Metal is a renowned manufacturer and provider of high-quality roll forming machines. Their expertise lies in designing and producing roofing and construction machinery that meets the evolving industry requirements. With a strong commitment to innovation and customer satisfaction, Dahezb Metal continues to be a trusted collaborator for businesses worldwide.Conclusion:With its cutting-edge Glazed Tile Roll Forming Machine, Dahezb Metal is revolutionizing the metal roofing industry. This advanced technology not only saves time and facilitates efficient production but also delivers outstanding quality and durability. As demands for eco-friendly and sustainable construction practices increase, Dahezb's Glazed Tile Roll Forming Machine stands as a valuable solution for any roofing project.
Machine for Making Corrugated Iron Roofing Sheets
Corrugated Iron Roofing Sheet Making Machine Revolutionizes the Roofing IndustryIn the ever-evolving world of manufacturing technology, the introduction of the Corrugated Iron Roofing Sheet Making Machine has completely transformed the roofing industry. With its advanced capabilities and high efficiency, this innovative machine has redefined the way roofing sheets are produced, offering numerous benefits to both manufacturers and consumers. The Corrugated Iron Roofing Sheet Making Machine, developed by a leading engineering company, has already made waves in the industry due to its remarkable features and cutting-edge design. It is renowned for its ability to produce high-quality corrugated iron roofing sheets at an unprecedented speed, making mass production a reality for manufacturers worldwide. One of the key advantages of this machine is its versatility. It is capable of fabricating different profiles and designs, ensuring that manufacturers can meet the diverse needs and preferences of their customers. Whether it is a residential project or a large-scale commercial development, the Corrugated Iron Roofing Sheet Making Machine can adapt to the required specifications effortlessly, allowing for seamless production of customized roofing sheets. Moreover, this state-of-the-art machine significantly reduces human intervention in the production process, enhancing overall productivity and efficiency. With its automated functionality, it minimizes the risk of errors and the need for manual labor, thereby optimizing time and resources. Manufacturers can now accomplish more in less time, fueling the growth of their businesses and meeting tight project deadlines with ease. The Corrugated Iron Roofing Sheet Making Machine is also lauded for its exceptional durability and reliability. Constructed with high-quality materials and utilizing the latest technological advancements, this machine boasts a prolonged lifespan, making it a sound investment for manufacturing companies. It can withstand heavy loads and prolonged usage without compromising on the quality of the output, thereby ensuring the longevity and integrity of the produced roofing sheets. Furthermore, this machine addresses environmental concerns, as it incorporates sustainable practices in its operation. With its energy-efficient components and reduced raw material wastage, it contributes to the promotion of eco-friendly manufacturing processes. Manufacturers can now partake in sustainable initiatives while efficiently fulfilling the demands of the market, resulting in a win-win situation for both businesses and the environment.The introduction of the Corrugated Iron Roofing Sheet Making Machine has not only revolutionized the manufacturing industry but also impacted consumers positively. The availability of roofings sheets produced by this machine ensures higher quality and durability, offering enhanced protection to homes and infrastructures. Additionally, due to its efficient production process, the cost of these roofing sheets is significantly reduced, benefiting consumers by making home improvements more cost-effective. The company behind the Corrugated Iron Roofing Sheet Making Machine, as a pioneer in engineering excellence, has always been committed to developing innovative solutions that address the needs of the construction industry. With its unwavering dedication to producing cutting-edge equipment, this company has become a trusted partner for manufacturers seeking reliable and state-of-the-art machinery for their production processes.As the demand for high-quality roofing sheets continues to grow, the Corrugated Iron Roofing Sheet Making Machine remains at the forefront, paving the way for the future of the roofing industry. Its unrivaled capabilities, streamlined production process, and commitment to sustainability have made it a game-changer, setting new standards for manufacturing practices. With this revolutionary machine, manufacturers can achieve higher levels of efficiency, productivity, and customer satisfaction, positioning themselves as leaders in the competitive market.
High-Quality Floor Decking Roll Forming Machine Available in China - Wholesale and Export to Worldwide Market
and China Manufacturers.Floor decking roll forming machines are becoming increasingly popular in the construction industry. These machines are used to create floor decking panels, which are then used as a base for flooring systems in construction projects. These machines are capable of producing high-quality, consistent panels that are cost-effective and durable. If you are looking for a reliable and high-quality floor decking roll forming machine, then you should consider purchasing from China manufacturers.China manufacturers of floor decking roll forming machines offer a wide range of machines with varying specifications and features. These machines are designed to cater to the needs of various construction companies, ranging from small to large-scale operations. These machines are made using high-quality materials and are manufactured with precision, ensuring that they are durable and long-lasting. They are also easy to operate, which makes them an ideal choice for businesses that want to increase their productivity.When purchasing a floor decking roll forming machine from Chinese manufacturers, there are several important factors to consider. Firstly, you should consider the quality of the machine. You should look for machines that are made from high-quality materials and are manufactured with precision to ensure that the machine is durable and efficient. Secondly, you should consider the features and specifications of the machine. You should look for machines that have the features that you need for your specific business requirements. Finally, you should consider the price of the machine. You should look for machines that are competitively priced and offer good value for money.In conclusion, if you are in the market for a high-quality floor decking roll forming machine, then you should consider purchasing from China manufacturers. Chinese manufacturers offer a wide range of machines that are made using high-quality materials and are manufactured with precision to ensure that they are durable and efficient. These machines are also easy to operate, which makes them an ideal choice for businesses that want to increase their productivity. When purchasing a machine from China manufacturers, you should consider factors such as the quality of the machine, its features and specifications, and its price. With these factors in mind, you can find the perfect machine for your business needs.
Plastic Corrugated Roof Tile Making Machine for Efficient Roofing Tile Production
If you are considering venturing into the roof tile manufacturing business, then it might be a good idea to invest in a plastic corrugated / glazed roof tile making machine. The equipment is versatile and can produce a range of roofing tiles with different styles and designs.At Jiangsu Acemien Machinery Co., Ltd. (ACEMIEN for short), we offer state-of-the-art PVC+ASA co-extrusion roof tile making machines that are designed to meet the demands of modern roofing tile production. Our machines are compact and efficient, and can produce tiles with high quality and accuracy.One of the primary advantages of our corrugated roll making machine is that it uses PVC and ASA materials in the co-extrusion process. PVC (polyvinyl chloride) is a plastic material that has excellent toughness, chemical resistance, and weatherability. ASA (acrylonitrile-styrene-acrylate) is a thermoplastic material that combines the properties of acrylics and styrene plastics.When the two materials are co-extruded, the resultant roofing tiles exhibit superior resistance to weather, UV radiation, and impact. They are also easy to install and maintain, which makes them a popular choice for homeowners and commercial property owners alike.Our PVC+ASA co-extrusion roof tile making machines can produce tiles with various shapes, sizes, colors, and textures. The corrugated roll forming machine can create tiles with a corrugated or waved surface, while the glazed roof tile making machines can generate tiles with a smooth or glossy finish.Our machines are equipped with advanced PLC control systems, which enable the operator to control the various parameters of the production process. The machines also come with automatic cutting and stacking devices, which facilitate a smooth and efficient production workflow.At ACEMIEN, we prioritize the quality and durability of our machines, which is why we use high-grade materials and components in their manufacture. Our machines are designed to operate continuously for long periods, and they have low maintenance requirements, which means that they can help you save time and money in the long run.In conclusion, if you are looking to invest in a high-quality plastic corrugated / glazed roof tile making machine, then ACEMIEN is the right company for you. Our machines are versatile, efficient, and reliable, and can help you meet the demands of the modern roofing tile market. Contact us today to learn more about our PVC+ASA co-extrusion roof tile making machines, and let us help you take your business to the next level!